Can you discuss your background and how you came to iCell Aqua?
I hold a BS in mechanical engineering and spent 20 years in the water industry, a majority as an executive with General Electric (GE). At GE Water, I learned about water treatment, membranes and protein fractionation – using different membranes to remove and sort proteins and other substances from a water stream. I also learned about system designs, how to build them and how they operate.
In 2009 I ventured out on my own and joined some others to start Bluewave Marine Ingredients, an international fish protein business. That business used membranes to fractionate, refine and purify liquid fish protein streams for the ingredient industry. Bluewave was sold in 2015, at which point I joined the iCell group, to help them grow internationally.
iCell Aqua integrates food-based wastewater treatment and recirculating aquaculture systems (RAS) to create a zero-waste food and aquaculture system. The technology underpinning iCell was developed by two scientists, Andy Logan and Seth Terry who sit on the board of the company.
They recognised the heavy loads of food particles in water expelled from food processing plants and they suggested that instead of making wastewater and destroying it, why don't we use that as a nutrient? They developed a biological process for the carbon, nitrogen and ammonia in the water that can be fed to a variety of bacteria species. Those bacteria can then be harvested and converted into a single-cell protein (SCP) that can be used as a feed ingredient. This process was different from the thousands of water treatment plants that use bacteria to clean water – none of them create a sellable protein product that can be used for the animal feed industry.
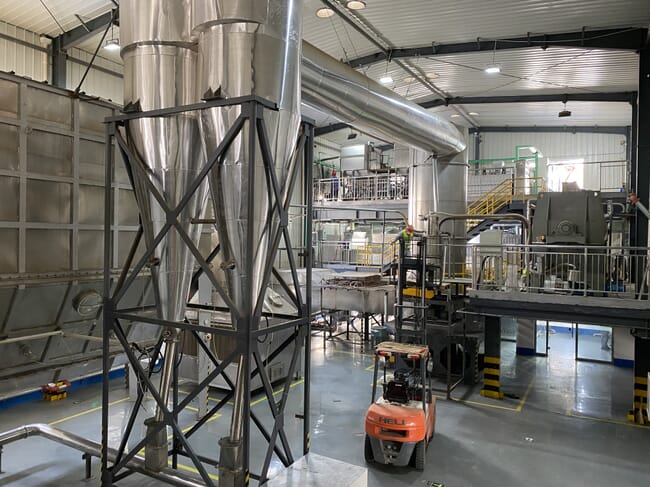
What drove iCell to look to integrate with aquaculture?
In 2019 at our iCell board meeting, I shared with the team that the iCell nutrient recovery could be applied much broader than just cleaning food process water and making SCPs – I told them that it could be integrated with aquaculture, specifically recirculation aquaculture.
So we created the model to combine iCell wastewater treatment with aquaculture – which solves the “last mile” problem of aquaculture. In this case, the last mile is all the sludge from faeces and uneaten food that is generated during production. We found that the system can support a wide variety of fish species – the nutrient load coming out of the iCell system (faeces and uneaten feed) are the food supply to the bacteria.
We don’t destroy nutrients while we clean the water in the system. iCell is designed for larger nutrient loads and injects far more oxygen into the RAS water to feed the SCPs while they grow. All of the components are coming together in the integrated system. When originally invented, the iCell process and concept was a bit before its time – before sustainable protein was the message and food wastewater was a big issue – today the world is ready and in need of the approach.
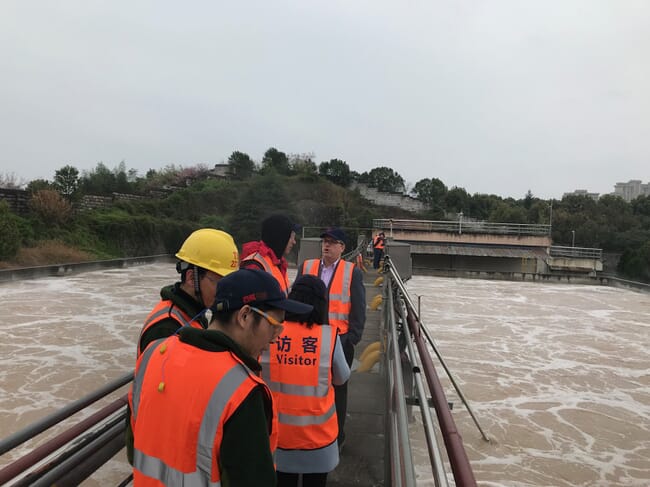
What challenges did you have to face as you commercialised iCell?
iCell has been running for years, so from day-one we knew the technology worked for RAS. We have multiple full-scale systems up and running in Asia that work on food process water from beer, sugar and seafood. We’ve piloted dozens of different applications – commercialising RAS is what needs to move faster.
The sites we're working with are all greenfield – they’re plots of land with nothing operating. So before we can operate, we have to build the RAS and iCell process from scratch. Getting funding for that kind of project is a real impediment. Everyone wants to invest in a running business, fewer people want to invest in a greenfield site.
When developing greenfield sites, the discharge permits are the key first step. We reduce the permitting issues, address the waste and sludge issue and make RAS fully circular. iCell eliminates the need for large volumes of water to be sent into the environment, which can accelerate the permitting process, but the hesitation and difficulty in funding these projects prevented us from moving forward. We saw that there are a lot of plans for RAS projects – but many of them are not breaking ground.
Can you explain how you integrated the water treatment process with a recirculation system?
We had some challenges to overcome when we were integrating the iCell system with RAS. The projects require engineers from two different disciplines and it needs them to think differently to solve problems.
The traditional approach during the design and build process is to minimise operating expenditures and capital expenditures for the water treatment system. Usually, engineers would view the water treatment as a process that destroys biological waste. We had to get the team to see that the water treatment component of iCell is a “second RAS” that grows the single-cell protein. Viewing the water as an additional revenue stream was a huge breakthrough.
For RAS specifically, we learned that “dirty water” is the number-one issue that caused fish die-offs in the system. iCell “overdesigns” the water treatment aspect of traditional RAS and we have the capacity to manage heavier nutrient loads than many traditional recirculation designs. Our RAS can cope with larger swings in the biological load, giving us a safety advantage.
Working to create a more robust water treatment method for the RAS was a direct result of viewing the process as an additional revenue stream. The single-cell proteins could cover the capital expenditures and operating expenditures needed to improve the method. We were able to address both sludge and water quality at the same time.
How have investors reacted to iCell Aqua’s concept?
We get lots of interest to invest in the iCell intellectual property (IP) company, but we aren’t interested in diluting that – we can self-fund our IP development. We’re more focused on helping recirculating aquaculture projects get funded by providing a more sustainable approach to RAS.
Our focus for the last 12 months has been helping investors understand how adding iCell makes RAS different. Initial discussions show that investors love our technology and see its benefits – they see our ESG status is a result of sound engineering and biology. They know that it’s not greenwashed marketing. We want to reducing the permitting issues, address the waste and sludge issue and making RAS fully circular. We’ve embarked on new projects in the US and Europe as well.
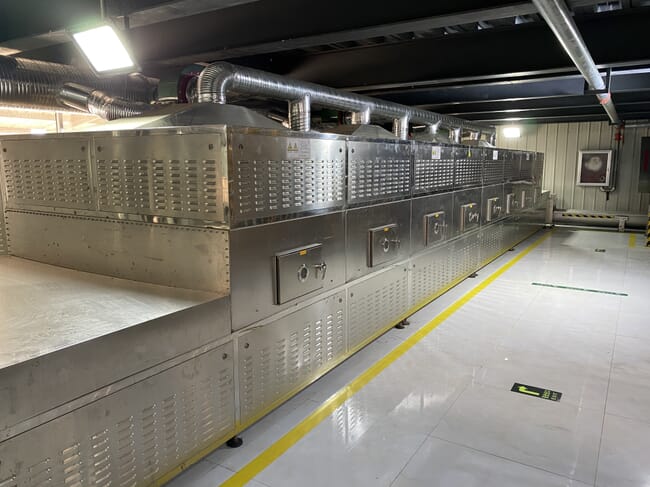
What will you be speaking about at the forthcoming Animal AgTech Innovation Summit and why are these events important to startups like iCell?
The Animal AgTech Innovation Summit allows companies to share solutions with the industry in an efficient and pragmatic manner. iCell Aqua’s presentation will be around helping the industry understand that a 100 percent circular economy approach is now available for aquaculture.
When it comes to an aquaculture business, there are plenty of customers for the final fish product – but cleaning water and addressing the environmental aspects of production are the biggest operational challenges of the RAS business model. When operations suffer, fish die and RAS businesses fail. We can help RAS avoid that.
The Animal AgTech Innovation Summit is an excellent platform for the investor community. While I’m there, I want to understand what it would take for them to invest in greenfield RAS and why there isn’t more of it. I want to know what the investment community really needs and what they need to know in order to make a leap of faith. Each element of iCell has been done somewhere before, we’re just bringing it all together in a new site. It's not magic – it’s a better mousetrap.
Learn more about iCell Aqua here.
*Mark Rottmann will be speaking about iCELL at the Animal AgTech Innovation Summit, which is being held virtually on 19 to 20 October.