The company has recently been renamed Oceanloop, following a merger with Crusta Nova.
Wecker, who has been involved in aquaculture for two decades, has spent the last eight years fine-tuning his clearwater RAS pilot farm, near the port of Kiel, for vannamei shrimp. And he is shortly due to dramatically ramp up production from its current level of 5 tonnes a year, following a merger with Crusta Nova - another pioneering German shrimp producer - which led to Neomar being renamed Oceanloop.
From aquaria to seafood
After completing a PhD in aquaculture, followed by a course in business administration, Wecker went on to work for Sander developing water treatment systems for zoos and aquaria all over the world.
“We developed our Oceanloop RAS concept over 20 years ago – it was quite unique at the time and we thought, why not use this kind of recirculation technology for seafood production?” he explains.
“We thought it seemed obvious – there were declining fisheries stocks, and there were environmental concerns about open water aquaculture systems. So we started to look into how to adapt the technology from aquaria to make it both feasible and profitable to produce first fish and then shrimp,” he adds.
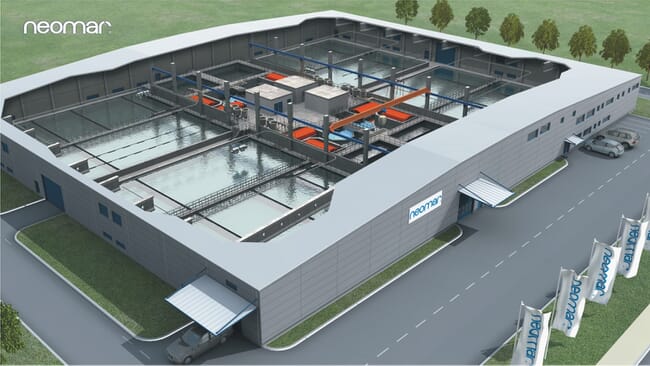
Wecker used his knowledge of operating aquaria when designing the Oceanloop system for indoor aquaculture.
As a result Wecker decided to found his own company, Neomar and began producing sea bream and seabass, before diversifying into a range of other species, including yellowtail kingfish, before focusing mainly on shrimp from 2015.
In the meantime his colleagues from Sander had been developing protein skimmers and ozone generators, for use in the rapidly-expanding salmon RAS sector – with customers including Danish Salmon, Jurassic Salmon and Atlantic Sapphire – and their own farm is the perfect place to test their new technologies and fine-tune their designs.
“The farm is really a demonstration and research tool. We develop a lot of our own technologies around shrimp and fish farming and we’re currently in the middle of developing a biomass detection system – we have cameras taking pictures every minute, counting the shrimp,” he explains.
“As shrimp are cannibalistic, they eat the dead ones, so it’s very hard to count the numbers – you need a detection system to have a live track on the environment. If you don’t it’s quite hard to get the feeding right and hard to predict your harvest,” he adds.
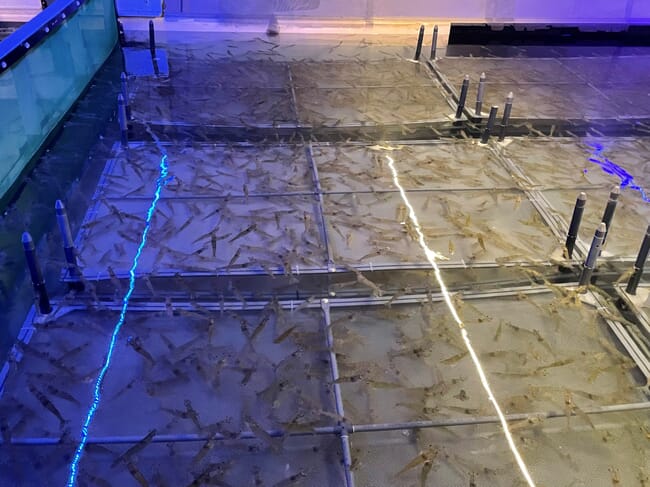
Neomar stocks shrimp at around 10 kg per cubic metre
The farm itself is, according to Wecker, very different from standard RAS designs, being based around a raceway system that is separated into a series of compartments.
“It’s a u-turn raceway, which means we don’t need pipes to take the water to a water treatment system, which saves a lot of energy,” he explains.
“We do continuous stocking and harvesting but the design allows us to gently shift the shrimp through the raceway as they get bigger. We tend to use three to five compartments for each grow-out cycle, depending on how many harvests we want to do. It’s totally different from all the other designs in land-based aquaculture because it’s allowing you a lot of flexibility if the growth rate is different from what you expected,” he explains.
It is also a system that works for a range of species.
“We can use it for fish, we can use it for shrimp and our design for a farm with the capacity to hold 10,000 m3 of water can be operated by six to eight people and produce up to 2,000 tonnes a year of species such as grouper which you can stock at 100 kg per m3 of water. For shrimp we stock at around 10 kg per m3, so the output would be around 400 tonnes,” he explains.
Wecker believes that the market potential for land-based shrimp farming is stronger than land-based salmon.
One of the reasons that Wecker opted for recirculation is due to Germany’s strict regulations regarding use of – and discharge into – natural seawater.
“Even here, on the Baltic Sea, it’s hard to get permission to get the water in and to discharge it. I don’t believe that Germany will change and I’m pretty sure that other European countries will become more strict,” he predicts.
After his foray into bass and bream farming he now believes that shrimp will be the company’s best bet.
“There’s a lot of competition in seabass and sea bream from cage farming, so we decided to concentrate more on exotic species like giant grouper and shrimp. Shrimp we do have competition from all the imports and we currently produce for a much, much higher cost. But our system can be profitable because we have high sales prices as the quality difference is so outstanding. The potential for land-based shrimp is much higher than for salmon – we’re now at the tipping point and we believe we will see a scale-up in land-based shrimp, like we already see with salmon farms, soon because there’s a huge demand from the market side,” he argues.
However, he also warns that there’s a shortage of skilled personnel in the RAS sector.
“Land-based farming is not really truly professional yet. Everyone tries by themselves, mistakes are repeated, there’s still some way to go before achieving a professional mindset in every company. But our system is really different – it’s outside the box – and avoids many of the negative aspects of conventional RAS designs,” he notes.
He also believes that too many shortcuts are made when setting up RAS farms – with protein skimmers, for example, not being used enough.
“They were first used in aquaria in the 1970s, to ensure high visibility, today nobody is doubting the need for them in modern RAS, but there’s a way to go before everyone has a skimmer with the right capacity,” he argues.
Clearwater vs biofloc
Although he has trialled both biofloc and clearwater systems on his farm, Wecker is a firm believer in the latter, as he likes to be able to observe the shrimp as closely as possible.
“It might not make a difference for the shrimp, but if you can’t see your animals you can’t be a good farmer,” he argues. “Especially today, as we have a lot of camera vision and artificial intelligence systems monitoring the shrimp and you can’t use those in turbid water.”
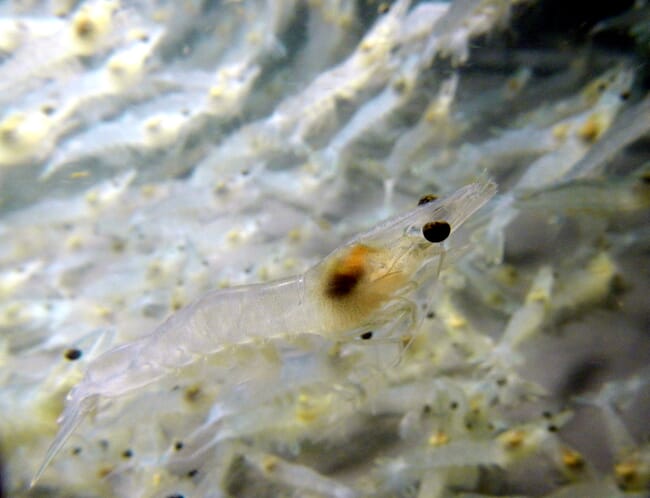
Wecker has opted for a clearwater RAS to give him better visibility of his shrimp.
Interestingly, he notes that trials he undertook to compare the health status and performance of the shrimp were very similar in both biofloc with clearwater. He also notes that taste of the shrimp produced in the two systems is surprisingly similar.
“Turbidity can cause off-flavour, but in a well-managed biofloc the organic matter is alive and active, not dead, so doesn’t create off-flavour,” he explains.
Despite the similar performance of the two systems – and the comparatively high cost of the clearwater version – Wecker had no doubt which one he preferred to operate.
“The cost benefits of using a clearwater system are not that easy to calculate, but when you add up all the pros we are certain that it makes sense. Both me and my farm manager decided it was horrible to operate the biofloc system, we could see nothing. We couldn’t see mortalities, whether we were overfeeding or underfeeding, it was even hard to see any disease problems until right at the end when we were harvesting the shrimp,” he explains.
However, he believes both versions will play an increasingly important role.
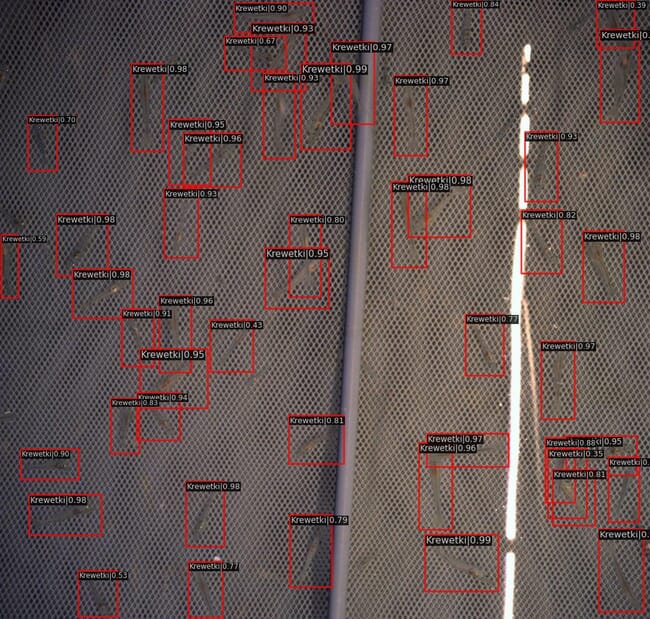
Wecker found that the health status and performance of shrimp raised in biofloc and clearwater systems were very similar.
“I think there will be different larger-scale shrimp producers popping up across Europe and the US – some using biofloc some using clearwater. Biofloc is attracting more investors because of the much lower Capex and Opex, but we will have to wait and see which proves more profitable. Maybe we will see both used side by side – because each has their advantages and disadvantages,” he reflects.
Future plans
Wecker is keen to scale up his operations in the near future.
“Our calculations show that a certain scale – above 1,000 tonnes – we can be profitable and compete with the branded shrimp products in retail stores. And when you have a locally-produced shrimp for the same price and better quality it will make a big, big difference,” he reflects.
He notes that the market is there – Europe alone imports 800,000 tonnes of shrimp each year and the number in the US is similar – and he is adamant that the taste of the fresh shrimp is significantly superior.
“Back when we were producing seabream and seabass, when we compared the fish from our RAS with those from cage farms we could see a 20 percent quality improvement, based on the freshness and on harvesting on demand. When I first ate a shrimp from our R&D system I thought it tasted like another product, another species. It’s hard to believe,” he recalls.
According to Wecker this is not due to the fact that most imported shrimp have been frozen, but is related to the difficulties of maintaining an effective cool chain in the remote parts of tropical countries where the shrimp are conventionally farmed.
“Shrimp are almost pure protein, so the deterioration starts immediately after harvest, especially in temperatures of 30° C. If the cool chain is not there you lose quality every second, which is why they put so many additives on them, such as phosphates and antioxidants, which is why the quality is so different,” he explains.
Foundations for growth
Key milestones that have been achieved to put Wecker in a position to expand include the development of the company’s own feed, which is produced in Germany and is licensed to be used within the EU, unlike the shrimp feeds produced by the major players in the conventional shrimp farming regions. This is available to the wider shrimp farming sector and includes a proportion – under 10 percent, according to Wecker – of insect protein produced by Protix in the Netherlands in lieu of krill meal.
Another is the dramatic improvement in grow-out rates, which he has reduced from 180 days in 2015 to 90 days in 2022, thanks to improvements in feed and genetics.
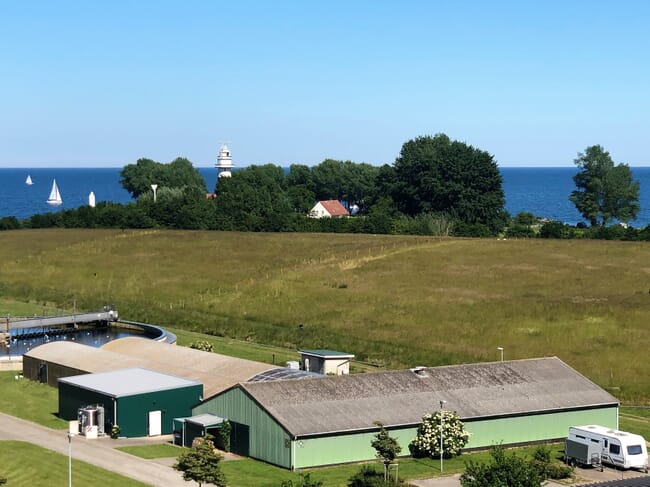
Neomar has developed its own shrimp feed and is seeing dramatic improvements in grow-out rates.
However, he is also aware that the drive for faster growing animals has also led to a reduction in disease resistance, with bacterial diseases being a particular issue due to the difficulty of vaccinating shrimp.
Intriguingly, while many of these diseases – such as AHPND – are attributed to Vibrio, Wecker thinks that the causes might be more complex.
“My personal belief is that the Vibrio problems are more a secondary effect. I think that the primary bacteria are different and might in fact be the chitin eating bacteria that thrive on the moulted shrimp shells,” he explains
If this can be solved, Wecker believes that the survival rates – which are much lower than in fish farming – could be improved considerably.
“In fish farming if you have mortality rates above 10 percent you are a bad farmer, but in shrimp if you have mortality rates below 50 percent you are doing well. We started with survival rates of 20 percent, but are now at about 60 percent, which is similar to ponds, and I’m pretty sure we’ll soon be at 70 percent, thanks to our better feed. We use a lot of additives to help the shrimp reduce stress and improve their immune response. It’s quite expensive but we get good effects on survival rates, so it’s valuable to do so,” he explains.
Merger with Crusta Nova
Most recently, as announced on 24 March, Neomar merged with Crusta Nova - a Bavarian land-based shrimp producer, which also sells a range of high-end seafood. The end result is the formation of two new companies: Neomar and Crusta Nova's shrimp will be produced by a new entity called Oceanloop; while the end products will be sold under the Honest Catch brand.
The merger is set to lead to the expansion of Oceanloop's farming capacities, in conjunction with the construction of a dedicated hatchery for the production of shrimp larvae. Internationalisation of Oceanloop farms to other import-dependent markets – such as the USA, Middle East or Japan – is also planned.
This process already has the backing of a German impact investor, while Oceanloop shareholders are currently actively approaching investors and aim for a total investment of about €150 million, which is expected to be completed by 2024.