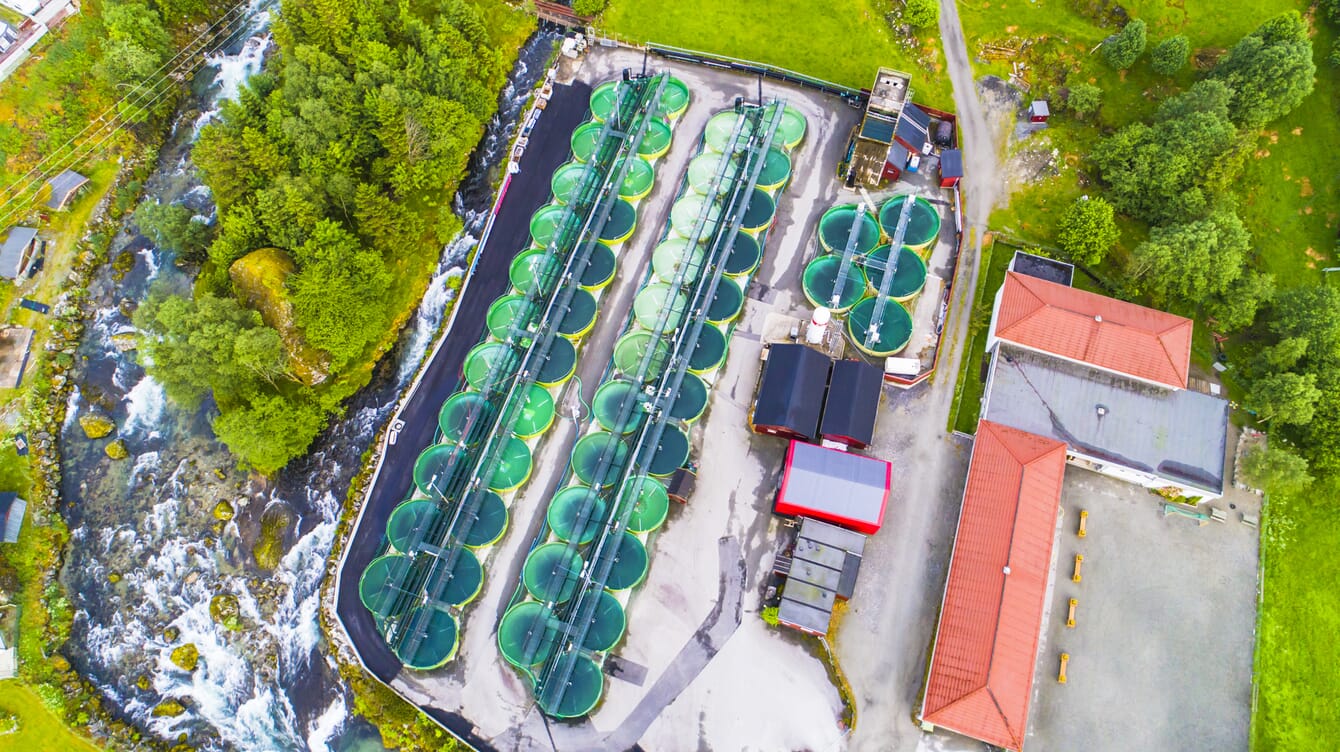
However, their ability to effectively produce market-sized fish such as salmon is still the subject of debate
In a typical recirculating aquaculture system (RAS) a series of treatment processes are used to maintain the level of water quality needed to sustain the cultured species, while simultaneously maintaining a very low water exchange rate. A key aspect of the treatment process is biofiltration.
How biofilters work
Biofilters use nitrifying bacteria to convert ammonia into nitrate and to further break down dissolved and leftover particulate matter. Biofilter activity is influenced by many factors, including substrate type and water quality. Fortunately, most contemporary systems are automated to keep these key factors at the correct predetermined levels and prevent any rapid changes.
Bacteria form a biofilm on the surface of a carrier, so called biomedia. The opening size, specific surface area, mechanical shear resistance and filling fraction (percentage of an empty biofilter volume) are a big part of how well the biofilter performs.
To increase efficiency of the biofilter, solids are removed from the process water first, reducing the biochemical oxygen demand, nitrogen and phosphorus loading of the system. Methods for rapid solid removal include screening, sedimentation, flotation, flocculation and adsorption. These techniques reduce clogging of the biomedia and accumulation of settleable and suspended particles in the biofilter.
Adoption of biological filtration in aquaculture
Biological filtration has been widely used in recent decades because of its relatively simple maintenance and effectiveness in removing nitrogenous pollutants from the process water in aquaculture.
The technique has been adapted from wastewater treatment plants, where a flocculent culture of microorganisms called activated sludge is used to process the water. In aquaculture, instead of activated sludge, artificial biomedia are commonly used as the bacterial carriers. Biomedia come in many forms and sizes and are usually made from food grade polyethylene or polypropylene. Shape and opening sizes in the biomedia are dictated by the organic loading rate and type of biofilter that it is used in.
The two most common forms of biomedia biofilters used in RAS are moving bed bioreactors (MBBRs) and fixed bed bioreactors (FBBRs). FBBRs boast lower energy use and higher phosphorous and denitrification rates, while MBBRs have higher volumetric loading rates and lower solids buildup (Choi, Lee, & Lee, 2012).
Other types of biological filtrations have been used in aquaculture such as biofloc, wetlands, integrated multi-trophic aquaculture, fluidised sand beds and ion exchange membrane bioreactors. However, none has made it into successful industrial aquaculture operations so far, mainly because they tend to raise operations costs and bring higher risks of failure.
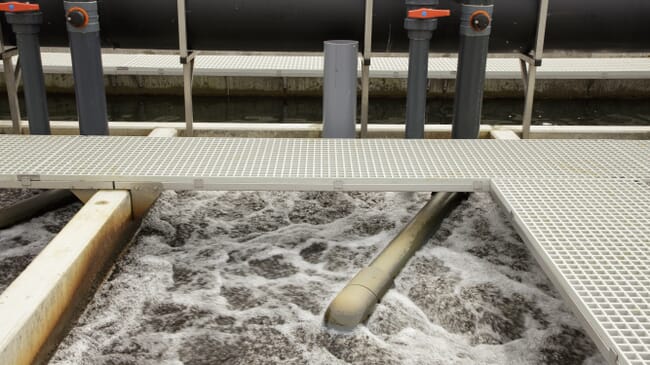
Limitations and challenges of traditional biofilters
One of the main obstacles in biomedia biofilters is that their efficacy changes with substrate type, and depends on the levels of dissolved oxygen, organic matter, temperature, pH, alkalinity, turbulence and salinity (Qi, Skov, de Jesus Gregersen, & Pedersen, 2022). Any rapid change of these factors affects bacterial communities and in turn the effectiveness of filtration. On top of that, the biomedia can also host pathogens and off-flavour producing bacteria.
Furthermore, the bacteria in biofilters use a considerable amount of the total oxygen demand in RAS (20-30 percent) and excrete CO2 and other metabolites. This increases the required capacity of degassing and oxygenation equipment as well as the operational cost in terms of energy demand and maintenance.
Alberto Monteleone, R&D facilities manager at AquaBioTech Group in Malta, who oversees research trials in over 30 RAS facilities – meaning he has over 30 biofilters to maintain and restart regularly – explains that water exchange, temperature fluctuations and pH changes have an adverse effect on the recovery time of biofilters.
“One of the big issues is the long and unpredictable startup period which makes planning of research trials exceptionally difficult, but crucial for success,” he observes.
Monteleone expects that more reliable water quality sensors will become available to identify issues that can lead to collapse of bacterial communities in the biofilters.
Biofilters also have some quite big challenges from an engineering point of view. Often the designs need to be integrated into existing structures, which brings limitations like structural loads and dimensional constraints. These can then negatively affect the ultimate efficacy of the biofilters. Another issue is that aquaculture operators can change feeding rates and stocking densities, which provides challenges to designing a stable and efficient biofilter.
Michele Gallo, who is in charge of aquatic research facility design at AquaBioTech, explains: “To tackle spatial constraints, computational fluid dynamics simulations are used to deliver designs that offer the most adequate hydrodynamic profile for the given needed outlets and space available.”
In addition, microparticle filtration, through methods such as protein skimming, are used to improve biofilter performance.
To complement the design, production plans need to be optimised in a way that provides smooth transitions between different growing periods and minimise biofilter loading fluctuations.
Gallo also notes that he has seen rapid growth in AI technologies being implemented in farming management software where data collected by monitoring systems is analysed with AI models to improve decision making processes for the operators and control systems.
New developments in filtration
In recent years, a few relatively new technologies have emerged as alternatives to conventional biofiltration, although these have not yet been implemented at scale.
1. Electro-oxidation
Electro-oxidation occurs in a reactor, using an electric current to drive the formation of nitrogen gas from ammonia (thus, minimising nitrate formation) while removing organic matter and reducing pathogen counts as well.
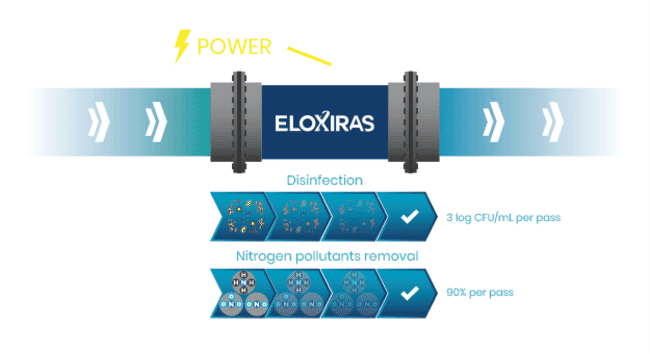
© Apria Systems
Electro-oxidation promises low energy use in marine aquaculture systems, even at high stocking densities.
“We reached a disinfection capacity of more than a 3-log (99.9 percent reduction of microbial population) even for bacteria with a higher level of pathogenicity,” says German Santos Bregel, R&D senior engineer from Apria Systems, a company that specialises in electro-oxidation technologies in the aquaculture sector.
The most significant advantage of electro-oxidation is that it can be started and stopped without a notable impact on the production cycle in a RAS.
“A notable advantage is the ability for the process to work at full capacity, even with temperatures as low as 5 °C,” says Bregel. Removal of multiple pollutants in one process also means that capital expenses can be reduced for RAS, since the need for ozone and UV treatment can be greatly reduced or even eliminated.
One of the biggest downsides of this process is the formation of trihalomethanes (THM) – byproducts toxic to aquatic organisms. There are two post-treatment processes need, degassing and adsorption of byproducts. Degassing already exists in conventional RAS, while the adsorption process is done with granular activated carbon and is an additional component that needs to be put into consideration in terms of investment and operation.
"We are currently in the process of obtaining the first references in the sector, as the industry remains dependent on traditional filtration methods. However, our technology has already been implemented in aquaculture facilities involving multiple species, including lobster, gilthead sea bream, sea bass, and salmon,” explains Sara Domínguez, chief commercial officer (CCO) at Apria.
This system seems most promising for marine RAS, since their effectiveness is dictated by the salinity level of water.
2. Electro-coagulation
The fundamental process in electro-coagulation is electric current passing through electrodes made of the same material and submerged in processed water or some other electrolyte. In this process, metallic oxides, hydrogen and oxygen are formed. Metallic oxides attract pollutants and have a high tendency to form flocs with them. The lighter flocs then float to the top of the water column with the help of hydrogen and oxygen gas which is produced in the electrolysis process. The flocs can then be easily removed by skimming. The heavier flocks sink to the bottom and are then removed as sludge with settling or even mechanical filtration (Boinpally, Kolla, Kainthola, Kodali, & Vemuri, 2023).
In the realm of RAS, electro-coagulation is interesting from two aspects: aiding in removing particulate matter and oxidising soluble pollutants like various sulphur compounds and ammoniacal nitrogen. Another benefit is also the fact that the electrolysis cell can easily adapt to varying conditions like feeding rates and temperature changes by applying less or more current to the electrodes.
The method does have its challenges, which come in the form of varying pollutant removing efficiencies due to several factors like pH, temperature, water velocity and current density in the cell.
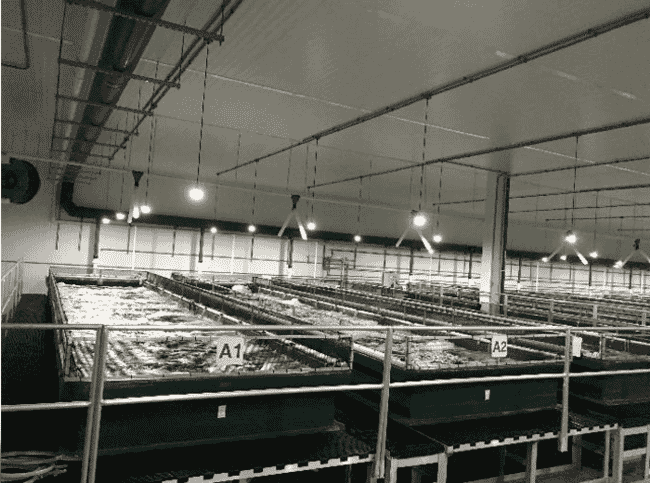
© NaturalShrimp Inc
In a recent development this technology was implemented in a shrimp RAS by a company called NaturalShrimp. Their main aim was to increase the size of total suspended solids so that they are able to remove them with micro drum filters. The process has also increased the removal efficiency for chemical oxygen demand, ammonia and nitrite (Ben-Asher & Lahav, 2016). To tackle the ever-changing environment in aquaculture water they measure water turbidity and then vary the current applied to the electrodes accordingly.
The company aims to conduct several smaller trials with local shrimp farming companies in order to further validate their technology.
3. UASB reactors
Another potential process that has been recently developed for RAS is the upflow anaerobic sludge blanket reactor (UASB). It is used to treat wastewater that leaves the RAS facility (end of pipe treatment) or as a polishing step for water to be returned to the system.

UASB integrates a bioreactor and sedimentation tank, making it very compact in the realm of anaerobic reactors.
“A significant advantage is the ability to decouple the hydraulic retention time from the sludge retention time, enabling different filtration goals. For instance, maintaining a solids retention time of around four days facilitates the production of volatile fatty acids that aid in denitrification. Shorter retention times promote organic acid production, which helps in solubilising nutrients for aquaponic or integrated multi-trophic aquaculture (IMTA) applications. Longer retention times are useful for biogas production. Additionally, the flow through the reactor can be controlled while retaining the sludge, allowing for optimisation of removal rates and outlet concentrations for specific parameters.” says Carlos Espinal, innovation director at Landing Aquaculture, an engineering and consultancy company focused on land-based intensive fish farming.
The performance of the reactor depends on the temperature. If operated in suboptimal temperatures (below 20 and above 35°C), the bacterial community changes and a community that is more suited to the given temperature populates the sludge blanket. To sustain nitrogen removal rates, the temperature needs to be in the optimal range and temperature changes should be gradual. If a significant temperature drop is expected the reactor must be properly sized to accommodate those variations.
In addition, Espinal highlights the issue of bulking sludge in freshwater reactors and high initial cost of the automation equipment that is needed for proper control and monitoring. To prevent this, Landing Aquaculture is using automatic flushing and a specific outlet design. Where cost of additional automation is prohibitive, manual monitoring and operation of these reactors can be done.
Unlike electro-oxidation, UASB is already being implemented in the sector.
“These systems have been used in the Netherlands as end-of-pipe treatment in fish farms and are among the recommended practices from the Dutch Standard for Sustainable Aquaculture,” says Espinal.
Future outlook
As it stands, it looks like the conventional biofiltration is here to stay, due to its long tradition and proven effectiveness. Electro-oxidation and electrocoagulation have the potential to replace biofilters or at least attenuate the shortcomings of filtration methods used in RAS. For now, it appears that no other technology apart from these two are able to compete with the very specific role that nitrifying bacteria play in biofilters. Improvements in traditional biofilters in the form of improved biomedia and better flow profiles of biofilters are expected.
UASB reactors will most likely find their place as end-of-pipe treatment as environmental standards become more stringent and RAS farms grow larger, making these types of reactors more viable. Further developments in water quality sensors will offer better insights into the welfare of bacteria and give farmers more opportunity to employ corrective measures.