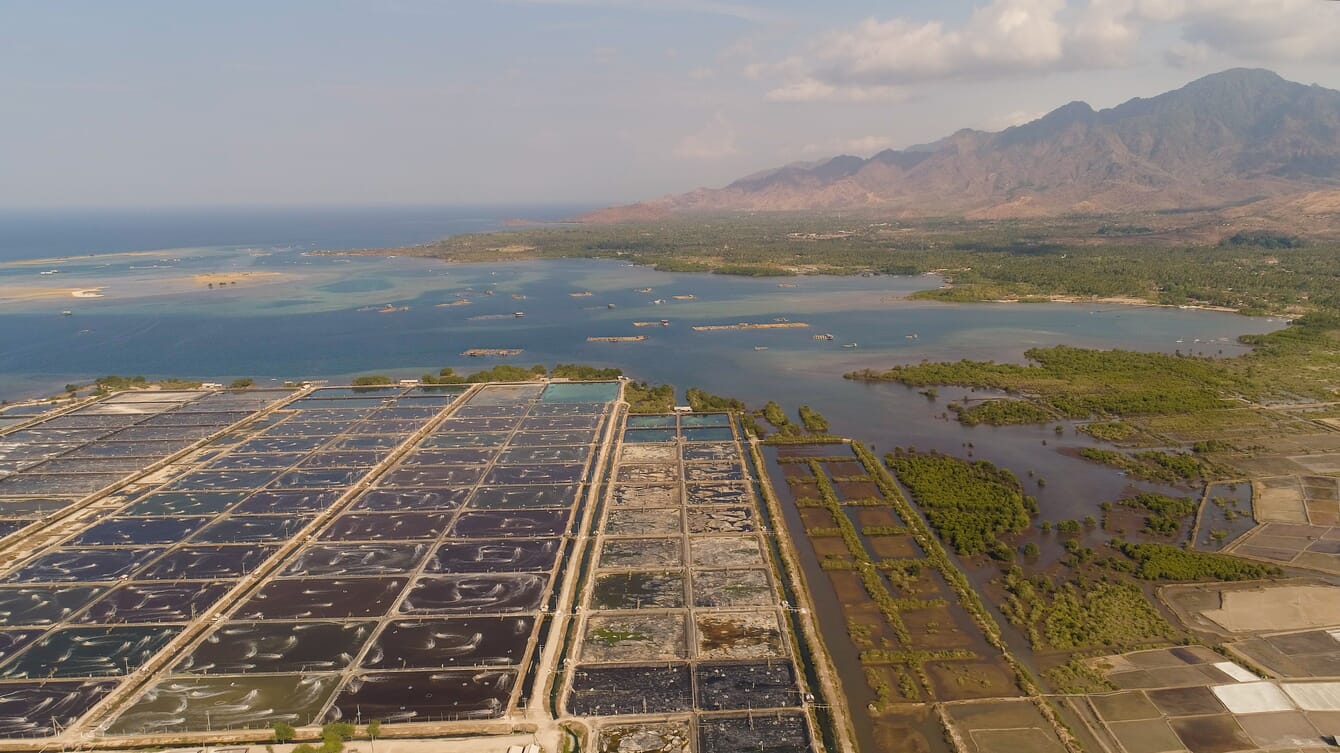
From 2002 to 2010 shrimp production in Asia increased from 1 million tonnes to 2.5 million tonnes, largely due to farms adopting technology to support growth © Shutterstock
Over the last few decades, as shrimp farming has evolved, there has been a general trend towards higher and higher stocking densities to increase production. In Latin America, the term “technification” is often used to describe this process – through which, the adoption of various forms of technology are used to increase stocking densities.
When it works, the process of technification increases shrimp production per unit farmed area, resulting in greater global volumes of shrimp. However, it is only profitable when it increases the efficiency of shrimp production and thereby – most importantly – decreases the production costs.
This was successful in Asia during the 2000s, and it’s currently working well in Ecuador. But it’s not a policy without risks.
From 2002 to 2010 shrimp production in Asia increased from 1 million tonnes to 2.5 million tonnes, while the cost of production on a typical farm in Thailand was reduced from 175 baht/kg to 90 baht/kg. During that period, farms implemented technological solutions to support the growth: including aeration, automatic feeding, nurseries, SPF stocks, genetics, improved nutrition and feed management and exclusion biosecurity.
More recently, Ecuador has followed a similar trajectory, with increases in production resulting in lower costs, even at a time when inflation was increasing.
Ecuador has essentially been applying the same technologies that Asia applied successfully early on. They also closed their ponds, so they didn’t depend on lunar cycles for harvests: thereby allowing everyday harvesting which permitted more shrimp to be processed. Through the application of technology, they have reduced their costs while increasing productivity – similar to what Asia did in the early 2000s.
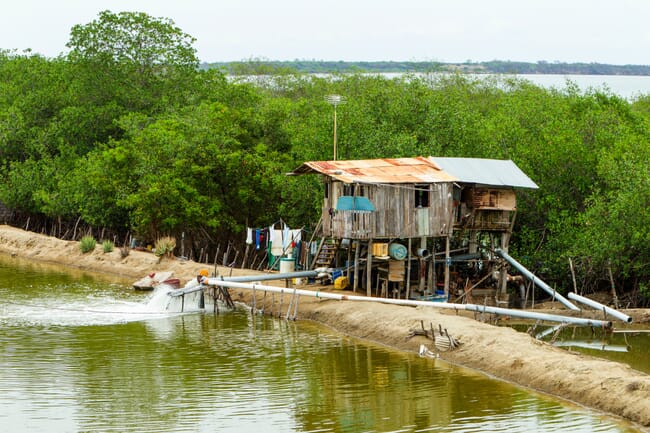
More recently, shrimp farmers in Ecuador have started to apply more technology to reduce costs while increasing productivity, similar to what Asia did in the early 2000s
The turning point in Southeast Asia
The epidemic of APHND (previously known as EMS) in Southeast Asia in the early 2010s resulted in the stagnation of world shrimp supply for two years and inspired India and Ecuador to step up their own production, albeit with relatively low density techniques.
Meanwhile, in a bid not to fall behind these newcomers, countries such as Thailand, Vietnam, Malaysia and China decided to develop more intensive culture models, with more controls, in increasingly small culture units with the objective of increasing production and overcoming the issues of disease.
Stocking densities increased from 100/m2 to sometimes over 300-400/m2. In order to achieve this, chemical disinfectants, more and more probiotics, and what became known as functional feeds were thrown into the equation.
Can new technologies be cost-effective?
The highly competitive export market is what drives innovation and quick reactions in the shrimp farming sector. Many farmers now look at technology to turn farms that are not competitive today into competitive farms tomorrow.
We are hearing much about AI, about IoT, about automation as ways to increase efficiency, and – yes – maybe some technologies will increase efficiency. However, adoption must be accompanied by understanding and evidence that the additional costs will provide more efficiency and a return on investment.
Caution is required: if technology is haphazardly adopted for the sake of it, then this could result in losses instead of improvement in the financial condition of the farm. Successful technology must be deflationary.
Never exceed carrying capacity
Additional thought is required in regions that have increased the density and intensity beyond the carrying capacities – be it of individual ponds, the farm as a whole, or even the entire geographical area.
Exceeding carrying capacity results in the loss of an environmental capability to support a healthy culture system. Many products and technologies promise to overcome the issues brought on by exceeding carrying capacity, but many of these promises turn out to be false. Exceeding the carrying capacity results in increased disease outbreaks and pathogen loads. Thailand, Vietnam, Malaysia and China have seen the consequences of exceeding carrying capacity and have suffered from the belief that technology alone will reduce the issues.
Technology might “nurse” overloaded systems to continue, but it’s likely to incur into a cost which reduces the chance of being competitive on the world market. Failure to compete will be faced unless, as part of any intensification scheme, there is an understanding that there are limits and that these limits must be respected. Adding more and more technology to regain competitiveness might be more harmful than healing.
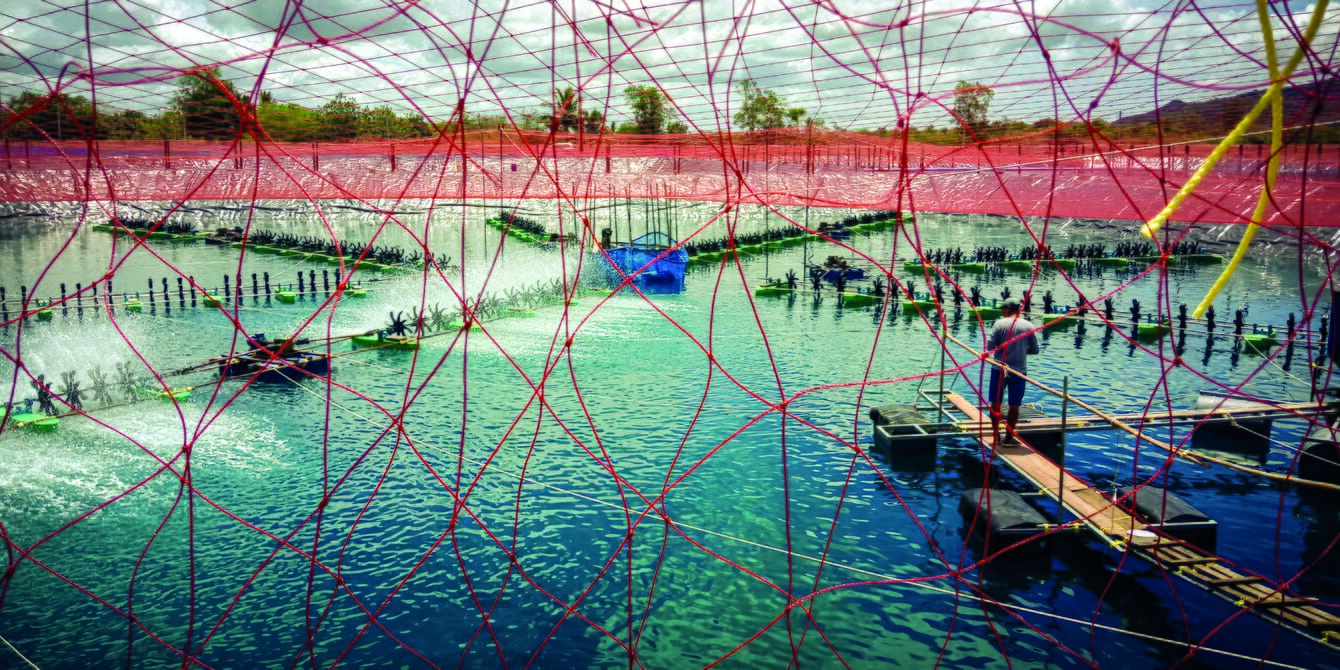
Technologal advances helped to recover production volumes in the Thai shrimp industry, but they also increased the cost per kilo of shrimp produced © FAI
In the case of Thailand, on one level, the use of technology was a success, as production volumes did recover – albeit not to previous highs. However, the added technology actually increased the cost per kilo of shrimp produced, while the increase in world shrimp volumes led to a reduction in prices.
If technification results in lower costs, farms that have gone down that route have traditionally succeeded. However, with the continued trend of lower prices, as world production continues to increase faster than consumption, two scenarios are developing. Scenario one is that of exporting countries. If these countries cannot produce shrimp more efficiently they will no longer be able to supply shrimp at commodity prices. Examples of this include Thailand and Vietnam, which must now add value to those shrimp they are looking to export.
Scenario two involves those countries with a strong domestic market, such as China, Brazil, Australia, and Malaysia (Singapore), which have been able to continue to grow their industries, despite competitive export prices.
For most of the history of industrial shrimp farming; it has been assumed that there will be a market for all shrimp produced. There were cyclical ups and downs in price, but the assumption was that if you build a new farm you’ll sell the shrimp; increase the production and you’ll still sell the shrimp. This is no longer the case and farms must be concerned with their production costs.
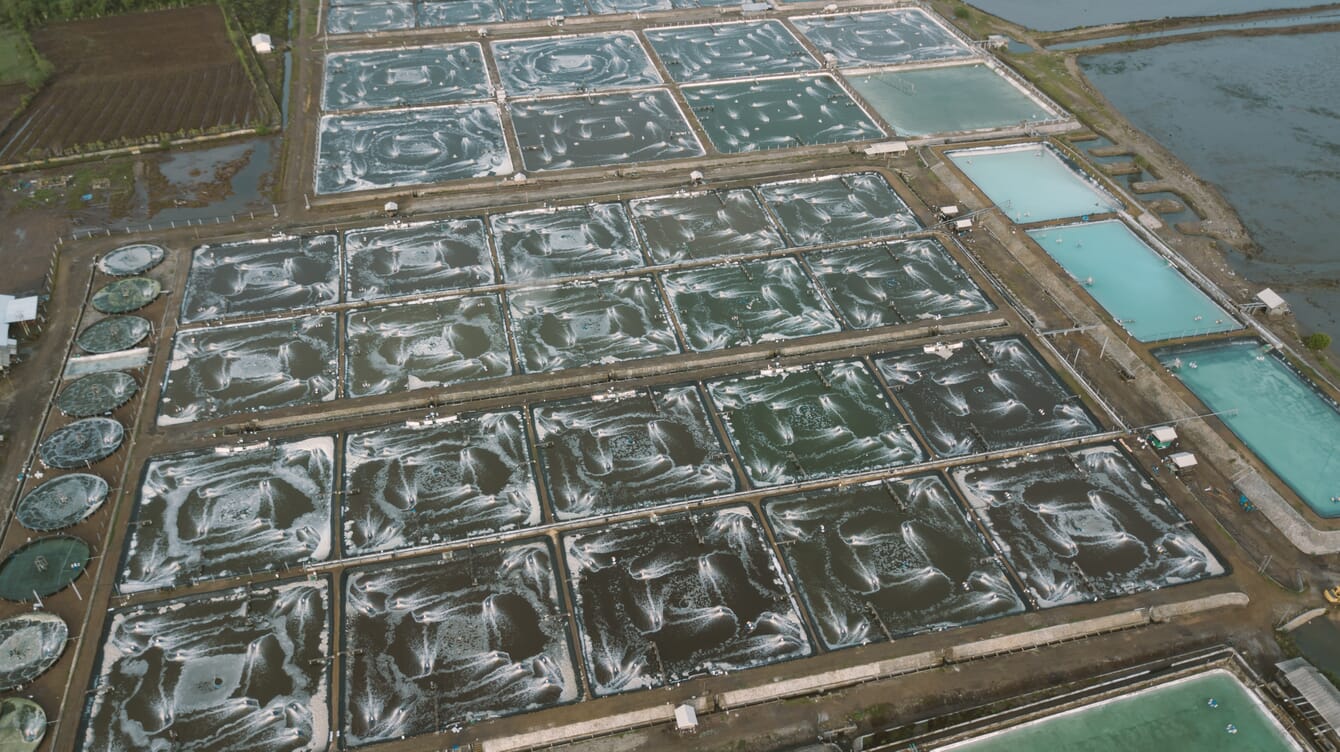
While intensification has proved successful for farms like this one, others have had to reduce stocking densities and improve management protocols © Delta Marine Group
Possible solutions to the problem
The question is how to heal areas that have exceeded carrying capacity and are now burdened by excess pathogen loads and deteriorated water quality.
The answer is straightforward, but very difficult to implement.
Culture intensity must be reduced to levels that do not exceed carrying capacity and a disease-free stock SPF programme must be implemented. And if the issue is affecting an entire geographic area then there must be cooperation across the farms in that area to reduce stocking levels. There must be an understanding that water quality is the basis of all aquaculture and, if the natural waters deteriorate from the release of too much waste – either from shrimp farms or other agrarian or industrial activities – growing shrimp will become more difficult. Poor quality water reduces the effectiveness of the shrimp’s innate immune system, thereby allowing shrimp to become infected more easily and then to spew more and more pathogens into the environment. A feedback loop starts and it becomes increasingly difficult to raise shrimp efficiently.
This is all too apparent with the microsporidian disease EHP. Anyone who monitors the outside environment will today find spores in the water, and since these spores are difficult to “kill”, infections continue in hatcheries or farms without the implementation of very expensive technology.
Examples of success
Some farms in Thailand, Vietnam and Malaysia are learning how to become successful again by not exceeding their carrying capacities. The formula has been to stock fewer shrimp (back to the pre-2012 level, when culture in Thailand averaged 100/m2); providing sufficient aeration for the new fast-growth genetics; maintaining clean pond bottoms to remove substrates for vibrio; using certified EHP-free post-larvae; and removing disinfection from management protocols.
There is still scope for the prudent use of probiotics and nutrient-balanced feeds – meaning those with protein levels applicable to the growth needs of the shrimp being grown.
The good news is that farms that have extensified have become profitable. And the even better news is that with the improved genetics now available, they can reach larger sizes in shorter periods of culture, reducing pond costs and feed costs (lower FCR), and achieving pond yields of 25-30 tonnes per hectare per crop. This is both sustainable and profitable in today's competitive world.
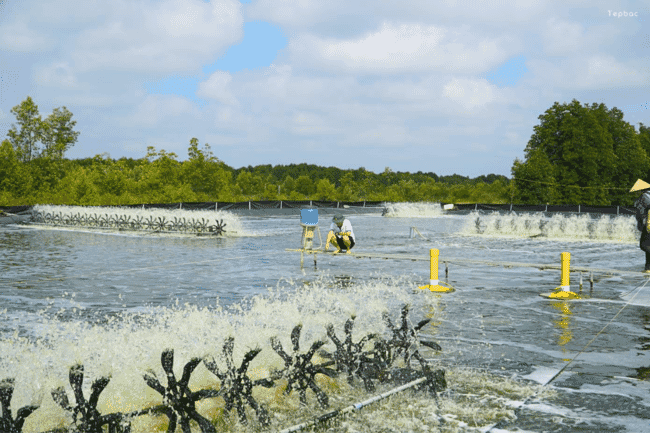
© Tebpac
Conclusions
Ultimately, if shrimp farmers are to be consistently commercially successful on a global scale, more countries must increase domestic shrimp consumption, reducing the pressure on export markets. But they must also stay within the carrying capacity of their culture systems and within the carrying capacity of an area connected by shared water.
Every company and every country wishes to improve its shrimp revenues. Blind intensification is not the way. Adding density is an accounting shortcut and does not have anything to do with the real world which is ruled by carrying capacity.
Improved genetics will provide one of the answers, but not the way most people think – it will not increase the carrying capacity of a given system or geographic area. Genetics is a vital and important tool for increasing efficiency, but it is not a solution to problems.
Instead of increasing shrimp stocking density to increase yields, improved genetics can reduce the grow-out time, which results in more cycles per year and decreases the FCRs – thereby increasing annual output and revenue while reducing costs. Genetics increases the size of shrimp, improving the revenue seen in the marketplace. Genetics is also the technology to increase specific disease tolerance and improve the innate immune expression levels in shrimp.
My wish is that lessons are learnt, and that Latin America learns from the Asian experience where over intensification has increased production costs. They must find the boundaries for profitability and remain within them.
Containing and disposing shrimp waste and protecting source waters from becoming eutrophic will reduce the pathogen load and consequent pressure. Now is the time to start monitoring the environment and creating awareness.