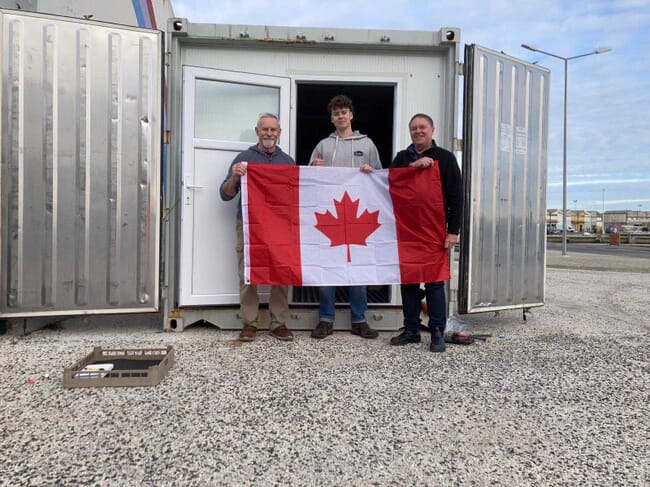
© Clean Valley
The system, developed by Clean Valley, has already proved its potential for reducing the footprints and enhancing the bottom lines of recirculating aquaculture system operators, and is now starting to gain traction in the insect farming sector too.
As Nicholas LaValle, founder and CEO of the Canadian startup explains, it’s all about finding opportunities for other people’s waste. And in this case, he is focused on using the nutrients contained in the wastewater from indoor farms.
“That water, rather than being dumped down the drain, trucked away or treated by the municipality, can easily be treated by the same mechanisms that are in the ocean, lakes and rivers: algae and oysters,” LaValle observes.
Clean Valley’s system is housed in standard 20 ft shipping containers which can easily be attached to existing farming operations. Wastewater is channelled through the containers, fuelling the growth of algae and oysters, while generating valuable co-products: the former for human consumption and the latter for animal feeds. At the end of the process, the water should be clean enough to be reused.
According to LaValle, it’s a system that can save money for farmers, as well as diversifying their product ranges and improving their green credentials. As he explains, it can help them avoid the “three pillars of pain” associated with indoor farming: namely fines and levies that companies face for wastewater disposal; the concern from consumers that indoor farming is unnatural; and the high carbon footprints (especially when considering carbon-equivalents) that indoor farmers face.
The latter might even have potential to be monetised, as Clean Valley has developed a carbon calculator linked to their units and have found a company that is able to verify and sell the credits that their system generates.
While initially developed with land-based aquaculture in mind, LaValle notes that it’s also applicable to any other industry that produces wastewater with high nitrogen or phosphorous levels – including insect farms.
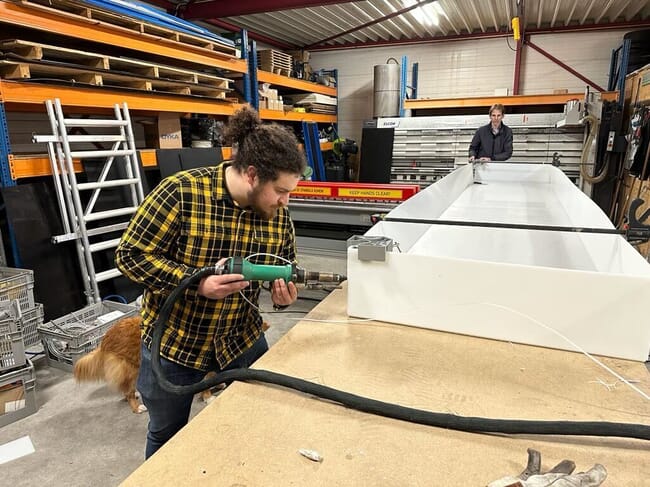
© Clean Valley
Why fly farmers should be interested
This synergy with fly farmers might come as a surprise to Fish Site readers, given the minimal volumes of water needed to produce insects. However, their exoskeletons contain phosphorous, which can leach into the wastewater.
“During the moulting stage – when either the larvae or the flies are shedding their skin – it generates a bit of phosphorous which then ends up on the equipment and substrates. So, when the fly farmers wash that equipment down, that water is very phosphorous-rich. It’s not part of their daily operations, but it’s part of their weekly cycle,” LaValle explains.
This year Clean Valley initiated a trial with Oberland Agriscience, a black soldier fly producer that’s also based in Nova Scotia – a trial that showed the algae were very effective at reducing the water’s phosphorus levels.
Not only that, but he found that the algae fed on the phosphorus-enriched water could then be processed into feed for the soldier flies themselves, closing the loop on the industries wastewater .
“In our pilot we were using their phosphorus to grow our microalgae and then feeding that back to their soldier flies as a high nutritional supplemental feed,” LaValle explains.
Since then he has lined up upcoming trials with Infinite Harvest – who want to grow algae in the same sealed unit as their soldier flies, thereby also making the most of the carbon dioxide the insects release – and NRGene, which is setting up a soldier fly production facility in Saskatoon and plans to assess the nutritional levels of the algae.
Meanwhile Clean Valley are waiting for the algae to be approved by the Canadian Food Inspection Agency (CFIA) for use as a soldier fly feed.
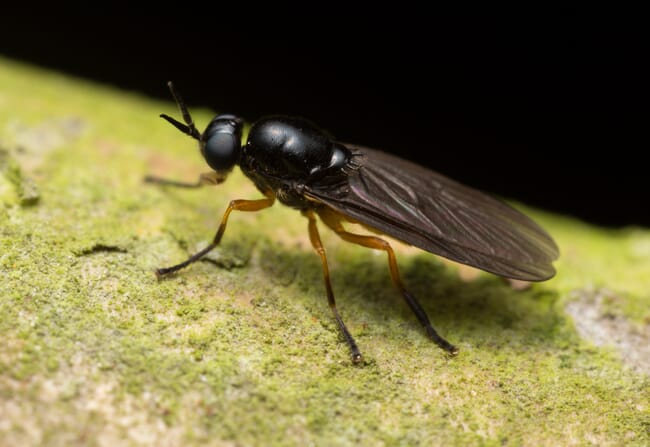
Closing the loop for black soldier flies
Over 30 companies – including household aquaculture names like Cooke Aquaculture, Atlantic Aqua Farms and SEAentia – have now signed contracts or letters of intent to test the concept on Clean Valley’s farms. And the startup is now offering an opportunity for insect farmers to trial their system in exchange for a small deposit and a testimony on whether the system helped to reduce their phosphorus levels and whether the algae produced allowed them to reduce the volumes of feed they provide to their insects.
“We’re offering three-month pilots in which their wastewater will be fed into our units, we’ll grow the algae, we’ll de-water it, and then the algae can be used in a feed trial that can be run at the site,” explains LaValle.
“If they don’t like it that’s A-OK. It’s easy to decouple the system and we’ll take it away. But if they like it, we can move to more commercial setup. The idea is to offer them the chance to try it before they buy it,” he adds.
In terms of practicalities, Clean Valley’s systems can be used in conjunction with conventional biofilters and can be bolted on to any existing RAS or soldier fly facility. What’s more, their hardware as a service (HaaS) model means that the farmers can leave the operational side of the units to Clean Valley’s technicians.
“Once it’s set up on a site, the only thing that the farmer needs to worry about is if we send them an alert – for example if the phosphorous levels are getting high – they might want to add additional water. The whole point of the HaaS model is that our technicians are on call and the farmer can concentrate on their farm,” notes LaValle.
Get in touch
Insect producers who are considering a trial of Clean Valley’s systems are encouraged to contact Nicholas LaValle via nhlavalle@cleanvalleycic.com