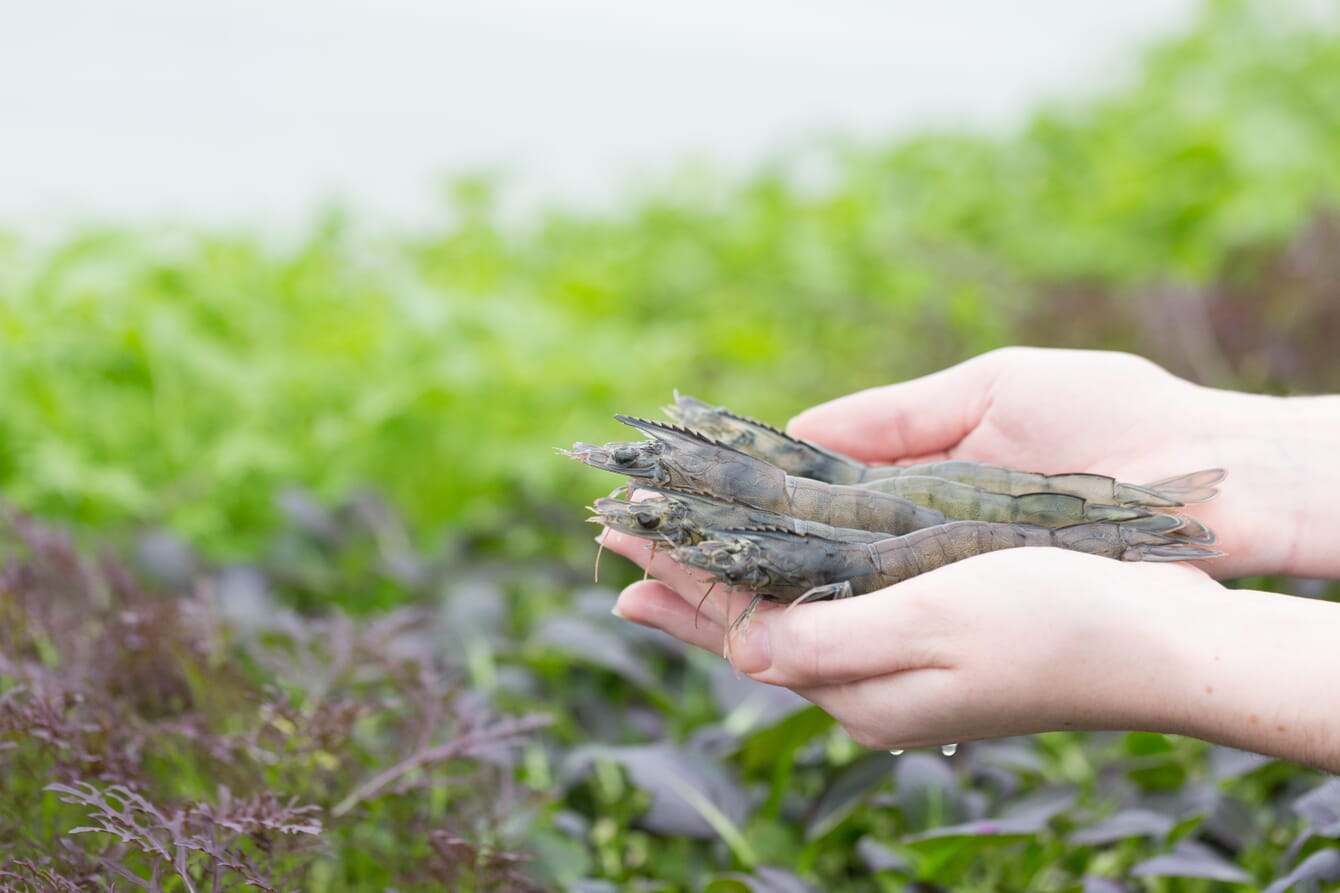
© Agriloops
Jérémie Cognard, Agriloops’ chief executive officer, and Romain Vandame, chief technology officer – who specialised in plant production and aquaculture respectively – met while studying at L’Institut Agro Rennes-Angers – a French grande école with a focus on agricultural and environmental sciences.
From early on, the pair envisioned creating a synergistic farming model.
‘’We were always thinking about the principles of a circular economy, and one day we discovered the technique of aquaponics, which combines aquaculture and plant production. This was just at the end of our studies, and that's when we really wanted to get started,’’ Cognard explains.
Agriloops was launched in 2016. From the beginning, the founders questioned why aquaponics wasn’t more widespread in France and elsewhere.
‘’The aquaculture part is often the most technical part, but at the time it was somewhat undervalued. So we said to ourselves, how can we move towards species with higher added value, where there are real markets? When we started digging, we realised that shrimp are one of the world's leading aquaculture markets,’’ Cognard recalls.
Shrimp consumption in France is high – the country is the second-largest consumer in Europe, with an annual market of around 100,000 tonnes. However, most of these shrimp are imported frozen and transported thousands of kilometres in refrigerated containers. This long supply chain contributes to substantial carbon emissions, while the conversion of mangroves into shrimp ponds that might happen in the tropics reduces biodiversity and undermines coastal protection.
© Emma Barbier
Faced with this reality, the founders had a vision – creating a more sustainable, locally produced alternative to imported shrimp. But choosing shrimp came with a major technical challenge: working with saltwater in an aquaponics system. Over the years, the team has gradually overcome the hurdles associated with salinity, eventually developing a patented technology. These efforts led to the launch of Mangrove #1 earlier in the year – the company’s first commercial-scale saline aquaponics facility.
Saltwater synergy
As Cognard explains, Mangrove #1 combines 2000 m2 of aquaculture area and a 5000 m2 greenhouse. The facility’s first shrimp are set to spend ten days in quarantine to verify that they are free from disease and so they can acclimatise. Once confirmed healthy, the post-larvae will be moved to the nursery area for one month and then to the on-growing area.
The farm operates a clear-water recirculating aquaculture system (RAS) that includes mechanical, UV and biological filtration stages. These systems reduce freshwater use and eliminate the need for coastal access – Mangrove #1 is located over 100 km from the sea.
A small percentage of the RAS water is diverted to the vegetable production section. Remarkably, this fraction covers the water needs for the plants, dramatically reducing consumption compared to conventional farming. The key innovation is that this water is not desalinated. Although saline water is typically toxic to many crops, Agriloops has turned this challenge into an advantage: they have found that the salinity actually enhances vitamin C and sugar levels in their tomatoes.
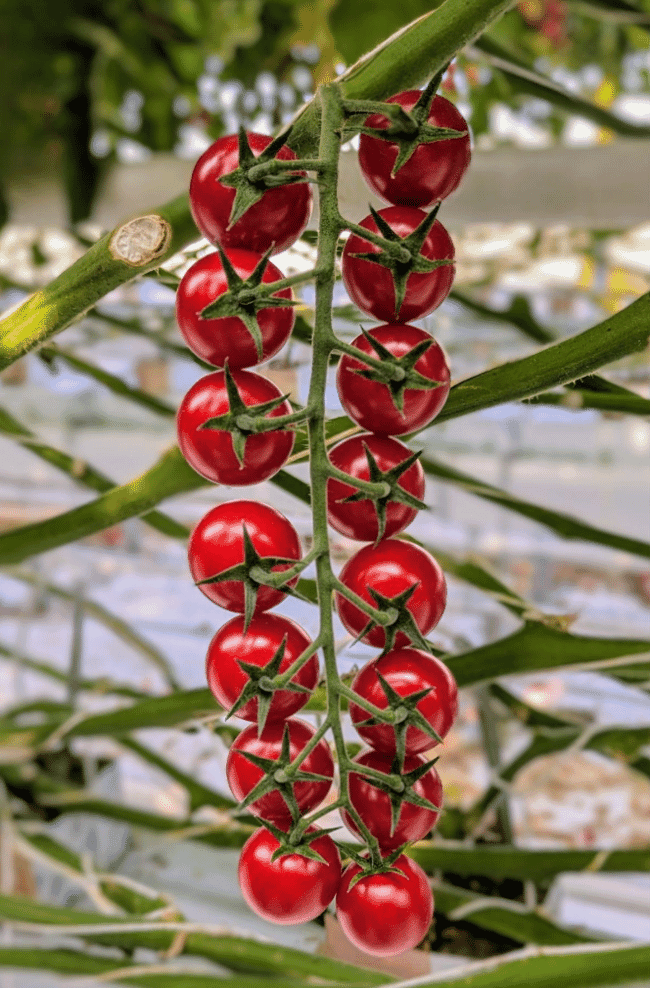
© Agriloops
‘’We have a system that is more resilient, more resource-efficient, as it's based on the principles of the circular economy. We use less water and almost no fertiliser, because the fertiliser comes from the aquaculture production part,’’ Cognard explains. ‘’The disadvantage is that we have two workshops, so at the start there are more things to master and develop. It's an added complexity, but once you've mastered it, it's a win-win situation.’’
Mangrove #1 is equipped with technology specific to both production areas. In the aquaculture section, automatic feeders, water sensors and digital monitoring programmes ensure optimal growth. The greenhouse features a central control room with a climate computer, which automatically cools the space through natural ventilation or shading when temperatures exceed set thresholds.
As vannamei shrimp are tropical animals, the system often requires heating. Staying true to their circular approach, Agriloops uses locally-sourced wood biomass from the surrounding bocage landscape – a patchwork of fields and hedgerows that's characteristic of Brittany. Wood is purchased from farmers within a 50 km radius, supporting local economies and encouraging bocage restoration. The boiler is considered carbon-neutral, and the farm also collects rainwater and powers its offices using solar panels.
© Emma Barbier
Built to flow
Agriloops began by testing its concept at lab scale in Paris, but the team quickly ran out of space, especially as they prepared to launch a pilot farm. The two engineers searched their network and contacted their former agricultural school, which offered space at its Rennes campus. Aside from benefiting from the school’s support, the city’s strong ties to French Tech helped the startup integrate into the local innovation ecosystem.
As the team grew and their ambition grew, they chose to stay in the region – relocating 20 km away to Bréal-Sous-Montfort to build Mangrove #1.
The project, combining cutting-edge technology with years of field experience, soon attracted investor attention. In early 2024, Agriloops closed a €13 million funding round – a mix of equity, grants and crowd investing – to support the construction of Mangrove #1.
‘’We went through the lab stage, proof of concept, then pilot, privatisation of the technology and several dozen batches where we gradually increased productivity. We managed to show that we had mastered the biological model and also the economic model. I think it is all the experience we have had that has reassured our investors,’’ Cognard reflects.
The team expects to deliver its first harvest from Mangrove #1 in the last quarter of 2025. Once fully operational, the facility aims to produce 50 tonnes of shrimp and 70 tonnes of vegetables per year.
‘’When you're at a stage of scaling up and ramping up, there are always lots of little problems to deal with, lots of things to discover and improve – we're in that phase. After that, we have the hindsight, the experience and the teams to solve all these problems. We're well armed but need to be patient and that's why a ramp-up has to be done intelligently. You can't just rush in with huge productivity, lots of animals and so on. You need to go step by step,’’ Cognard explains.
All processing and cold storage is handled in-house to ensure freshness and reduce transport-related emissions. Over the course of their pilot operations, Agriloops built a client base that includes SMEs, supermarkets and buyers at Rungis, the second-largest wholesale food market in the world. The company has already launched its cherry tomato range under the Yodée brand, and a branded shrimp product is set to follow.
When asked how Agriloops can compete in a market dominated by low-cost imports, Cognard remains optimistic.
‘’It is true that in general there are problems of inflation, low prices and so on. Despite all this, we can see that there are premium products on the shrimp farming market that still exist and with significant volumes: organic shrimp, Label Rouge shrimp – all quality products. If we manage to offer a quality product that stands out on the market, there is an opportunity to be on the premium end of the price scale. We're here to offer a high-quality French product. We know there's a demand for that. So, if the quality is there, the demand will be there.’’
Just the beginning
Despite its steady growth, Agriloops has no intention of stopping at a single site.
‘’We are calling our first site Mangrove #1 because our aim is to have other Mangroves... The big challenge with Mangorve #1 is to demonstrate that our technologies work on a large scale, that we can produce well and that we can also market our products well. And once we've done that, the aim is to duplicate the technology with other partners,’’ says Cognard.
One of the model’s major advantages is that it doesn’t need to be near the sea. The only geographic constraint is to access the heat solution. Otherwise, the Mangrove model could be implemented in many parts of France, Europe and beyond.
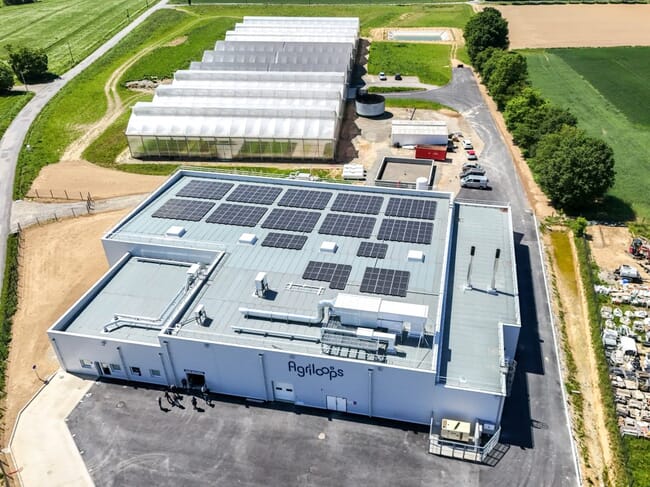
© Agriloops