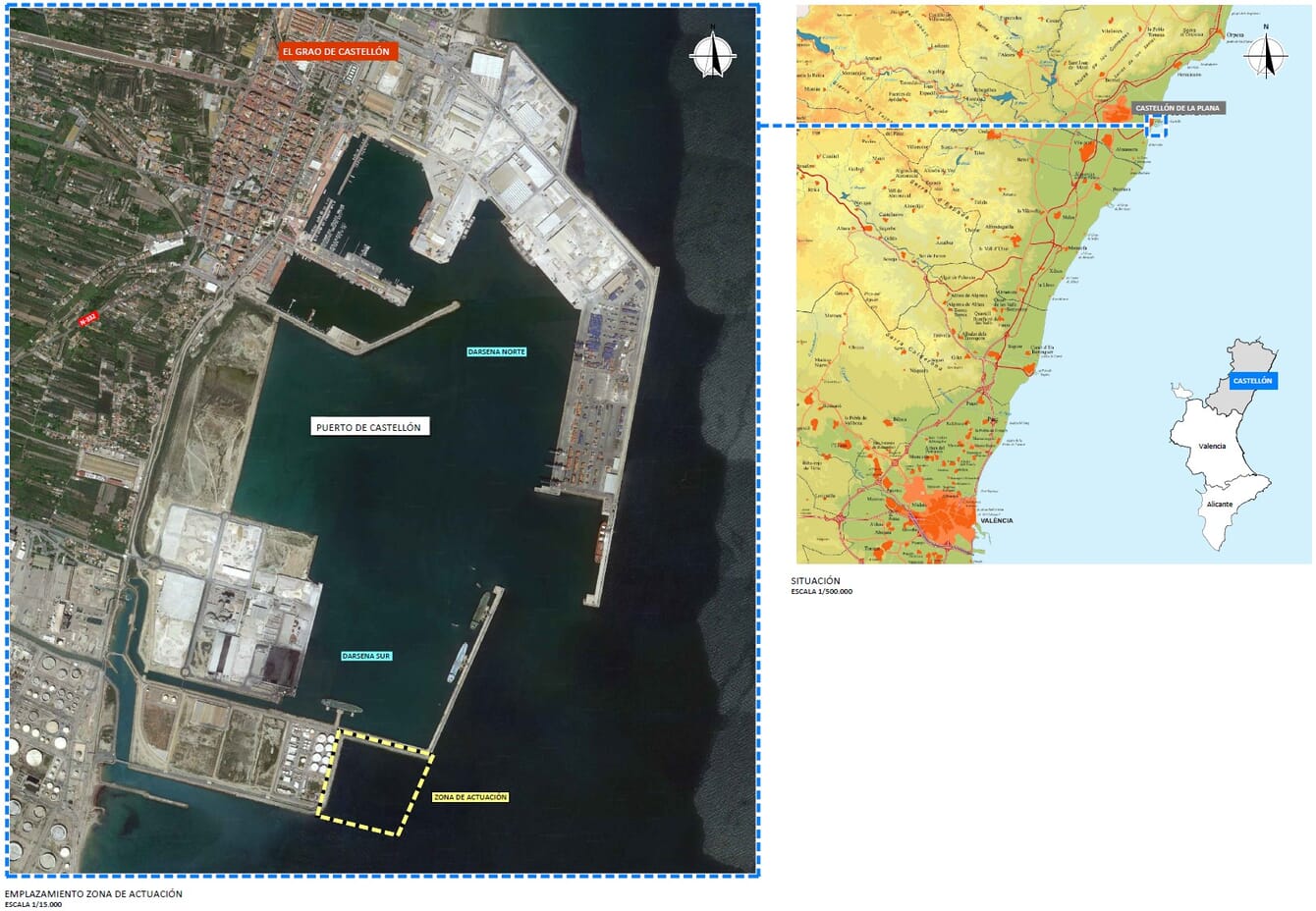
Paul Sindilariu founded Next Tuna in 2020 and is building a modular, floating RAS that will bolster the bluefin tuna sector © Next Tuna
The audience at a presentation by the Spanish Institute of Oceanography (IEO) at Aquaculture Europe in 2017, may have been limited in number – it took place in the graveyard shift that is a Friday morning. However, their talk – on the use of a RAS for Atlantic bluefin reproduction – fired the imagination of Paul Sindilariu to such an extent, that it inspired him to spend the next five years working on a plan to help the concept bear fruit.
Despite possessing the realism acquired from two decades in aquaculture – with a PhD in the subject, and extensive experience of planning, building and operating recirculation systems – Sindilariu was taken by the possibilities that IEO’s research could open up.
“If they were on the way to produce a recirculating system for tuna I thought it might be something about to come up in the near future and began to look more closely into this – and that’s how the whole story of Next Tuna started,” Sindilariu recalls.
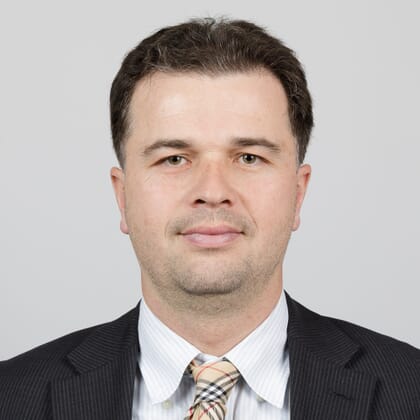
Sindilariu has been developing plans for a bluefin tuna RAS since 2017 © Next Tuna
Having been involved in the construction of over 20 RAS around the world, he began to develop the idea of farming tuna in RAS and – in 2020 – founded the company, with three partners. Within a year they had landed financial support from EIT Food, as well as backing from private investors.
“Since then we have been working seriously on developing this project, with the clear target to start on implementation next year,” explains Sindilariu.
“We are not the first ones to be looking into producing tuna in RAS, but most of the previous projects have had to stop. As their infrastructure was not designed for tuna, they had to release juveniles too early – leading to low survival rates when fish were transferred to open water,” Sindilariu adds.
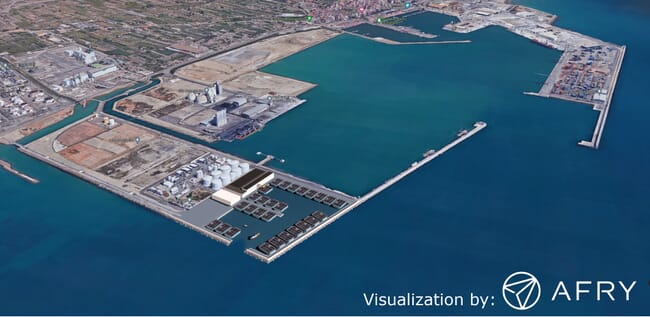
Previous Atlantic bluefin tuna RAS projects have had to be mothballed, but Sindilariu believes he can crack the code © Next Tuna
“From a biological perspective this makes sense: tuna is the only warm-blooded fish species and they need some time to develop this internal heating system, which starts to take place when they’re two kilos and bigger. Before they reach that size we need to really be in control of water quality and water temperature – and where are you able to control that better than in a RAS?” he asks.
“That’s why we opted for RAS to hatch the fish in this vulnerable stage, under controlled conditions,” he explains.
The company aims to grow the tuna to between 2 to 10 kg before selling them to existing tuna on-growers. These companies currently rely on a supply of around 600,000 wild-caught tuna juveniles a year. However, not only do they struggle to fill their quotas, but they also face criticism for the potential impact that removing this volume of wild juveniles has on the future of Atlantic bluefin.
The ongrowing process
The fast growing nature of bluefin means that they juveniles will be produced remarkably quickly, according to Sindilariu’s calculations.
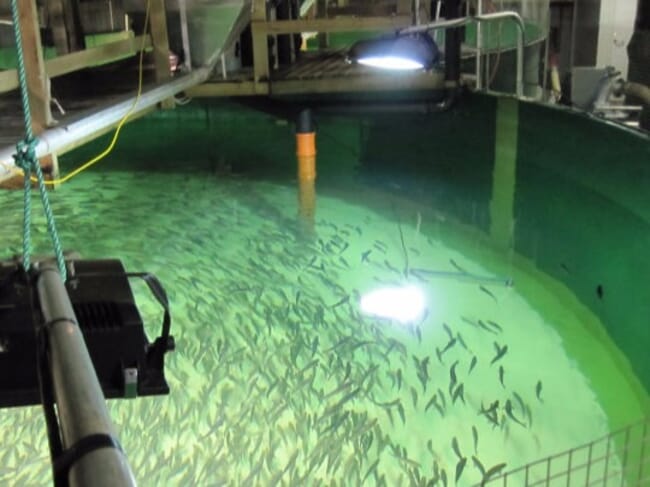
Atlantic bluefin tuna are fast-growing and warm-blooded © Next Tuna
Currently wild Atlantic bluefin stocks are increasing and – if the trend continues – this is likely to have an impact on the demand for farmed tuna, but the team is not overly concerned given their conviction that sustainable aquaculture has a key role to feed 8 billion people.
In terms of the likely customers, existing ranching operations are the most likely targets and the startup has been in discussions with the ranchers in the Mediterranean.
According to Sindilariu, IEO and Next Tuna are now working together to try to mimic the conditions in which the successful spawning took place in a RAS rather than repeat the feat in a net pen.
“We want to really do aquaculture, and that means being in control of the reproductive cycle, so we want to have our broodstock fish in RAS, work with a breeding programme, select the fish, select the replacement breeders, work with traits like feed conversion and growth rates. We want to do it properly,” he emphasises.
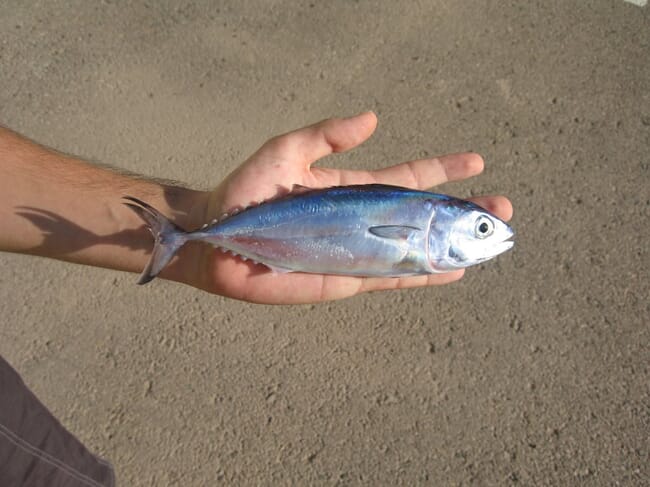
IEO and Next Tuna are now working together to try to mimic the conditions in which the successful spawning took place in a RAS © IEO
RAS… with a difference
Next Tuna have been working on a unique RAS design with a Norwegian partner, Seafarming Systems. In order to make the logistics of the transfer from the nursery to the cages smoother, they decided to design a floating system.
“It’s the size of a net cage, giving the advantages of a net cage, but is a completely closed RAS,” Sindilariu explains.
According to Next Tuna’s plans, the modules will float in a sheltered harbour, and each will be connected to land most of the time – allowing effluents to be treated, waste to be removed and inputs provided. But there will also be the possibility to disconnect each individual module – allowing the module to be taken out of the water and serviced after each cohort, while the fish can be transferred directly from the modules into the customers’ net pens.
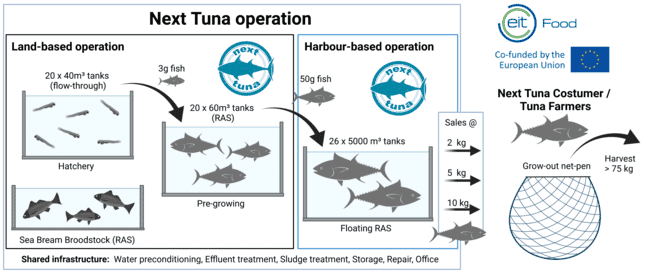
Next Tuna plans to use floating modules to produce tuna and believes that the design could work with grouper and salmon © Next Tuna
They also believe that the design could work well for other high value species, such as grouper, seriola or salmon. “It definitely won’t be as expensive as a land-based system – you get rid of all the groundwork, you don’t need to do anything in concrete and everything is accessible after you’ve built it as you can lift it out of the water,” says Sindilariu.
The modular nature of the system also means that producers don’t have to commit to a major expenditure but can gradually build up the number of modules, as their budget permits.
While the floating RAS might be the most innovative component of the design, these modules will be situated at a site – in Port de Castellon, north of Valencia – that’s set to include a hatchery, feed storage units, a workshop, a service area for the modules and an effluent treatment area.
“We expect the provisional concession by the beginning of next year, and the final concession in the second quarter of next year after the environmental impact studies have been completed,” Sindilariu explains.
“We believe that if we pull this off it has the same potential as salmon – if you’re the first to bring sustainably certified Atlantic bluefin tuna to market it’s a game-changer and we believe we have the team and the partners and the setup to do it,” he explains.
“Let’s not forget that we have two products – the tuna part of it is a longer shot, while the floating system should have a shorter lead time,” adds Sindilariu.
And, as well as the founders’ experience, the Next Tuna team is pleased to be working with some of the leading organisations in the sector – including Wageningen University, EIT Food, IEO and ASC.
Looking ahead
Beyond the hurdles posed by closing the breeding cycle in a RAS facility and raising the capital required to progress, other issues still to overcome include developing a feed that meets the specific requirements of tuna juveniles. However, the startup recently signed a cooperation agreement with Skretting to achieve this as an alternative to using baitfish. Moving away from baitfish does not only eliminate a biosecurity risk, it also is crucial to improved food conversion ratios, and thus both the ecological and ecomonic sustainability of the tuna industry.
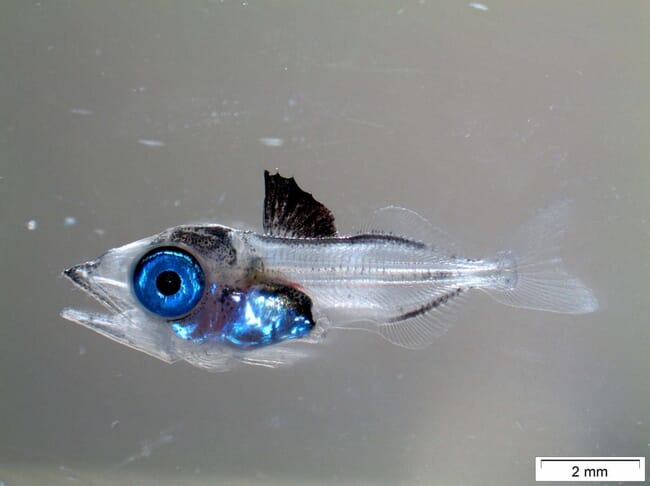
Next Tuna is developing a feed that meets the requirements of tuna juveniles in a recirculating aquaculture system © IEO
“In Japan they grow Pacific bluefin to a small size in the [hatchery] and ongrow them in very, very specific areas where they know they have the right water temperature to grow them to 2 kg, when they are less sensitive and can be distributed to the grow-out facilities. This model works but it’s not scalable because you need these very specific natural areas which are very limited,” explains Sindilariu.
“Our approach – the RAS model – you can implement it anywhere. At a later stage we’d like to establish satellite hatcheries where we can ship the eggs from our broodstock, copy the process, do the production of juveniles, then sell the fish to net cage operators in different parts of the world. Which makes this concept really scalable,” he concludes.