
The UK-based startup has designed a smart sensor for use by seaweed growers, and is in the process of developing an entirely smart “flat-pack” farm. Samudra is also venturing into the production side of the business, with licences for two of its own sites in Jamaica another two in western Scotland.
“In Scotland we’re just doing sample testing this season – not a lot, about 20 or 30 tonnes – but are planning to grow thousands of tonnes. We’re also going to buy a dryer: while local buyers might get raw biomass, our global buyers will get dried biomass. The global demand is different than the UK demand. The UK demand is capped by whatever has been invested in the biostimulants market, but the global demand is high, which is why we’re getting a dryer,” Das explains.
“We’ve also registered for carbon credits with the likes of the Kiloton Fund, so we will also try to turn the seaweed into biochar and stuff like that. The eventual goal is to produce 500 jobs in the region within five years and grow to a production capacity of a couple of thousand tonnes,” she adds.
Looking ahead, Das says that they aim to scale up to 20 farms around the world and produce 5,000 jobs within seven years – which would put them right in the upper echelons of the global seaweed sector.
An engineer's perspective
Das brings engineering experience to the industry, having worked for Cisco in Silicone Valley as an electronics and instrumentation engineer, as well as in the space industry. But she also brings a conservation angle, having been raised by parents who were conservation botanists.
“My mum taught me seaweed sampling in the oceans before I was four years old. And, even now, our house is still full of samples in bathtubs and jars. It’s in my DNA,” she recalls.
“Combining that with engineering, it just makes sense that we look at amplifying natural capital in the ocean that also provides employment,” she adds.
Samudra’s first innovation was to develop a device to give seaweed farmers a clearer picture of conditions at their sites remotely.
“The first step is measurement – if you can’t measure you can’t improve it – the next step is data and only then you can do anything else,” Das emphasises.
The device in question is a robotic sonde, which measures parameters such as salinity, temperature and pressure and transfers these readings to a smart buoy, which then beams the data into the cloud.
“The farmer can just look at their dashboard: they don’t have to burn fuel, use manpower or spend money on monitoring,” explains Das.
However, the startup is now looking to establish farms that are largely automated, with trials underway to assess the most effective designs.
“We’re looking at automating the entire structure, and are trialling a couple of hectares in Aberdeen. It’s then due to be tested at our own farm in Scotland in November,” Das explains.
If the farms can be automated, she argues, the growing lines could be closer together, as boats wouldn’t be needed to seed, service or harvest them, which would allow for more intensive production.
“Because there’s an existing rope infrastructure for about 20 tonnes [at their Scottish Farms], we’re starting out by deploying our robots [sensors], but in parallel we’re using the farm for various experiments as a test bed. And by next year it will be completely smart,” Das notes.
So far, eight early stage operators around the world have signed up to the concept – four in Canada, one in Mexico, one in Oman, one in Hawaii and one in Sri Lanka.
“The common problem with seaweed aquaculture is that everything needs to be done in the water. And that’s hard and dangerous – you need more people, there’s mortality, you’re more dependent on weather and tides, it does not scale,” Das observes.
As a result, she’s trying to develop a radically different system to the fixed rope structures that currently dominate production. The flatpack farm is likely to consist of either 40 x 8 foot or 20 x 8 foot panels that can be joined together to create a size and shape that suits the customer’s needs. Once assembled onshore the farm can be folded into a shipping container and transported to the growing site to be deployed.
While Das is not yet ready to divulge the precise design, as Samudra are awaiting confirmation of several patents, she notes that it’s a “mixed structure” that is likely to largely consist of ropes and steel, while other materials such as coated aluminium are also being tested.
“All the harvesting and the seeding could be done on shore. It’s very similar to space – if you build a rocket you build it here, not in space – as it’s a hard enough environment to even have a product survive in,” she reflects.
“That’s the ethos I want to bring to aquaculture. How about we do the seeding and harvesting on a foldable structure on the quayside. You just tow it to the growing region where it stays and then tow it back for harvest. Maybe tow it back once during the growing season for biofouling and servicing,” she adds.
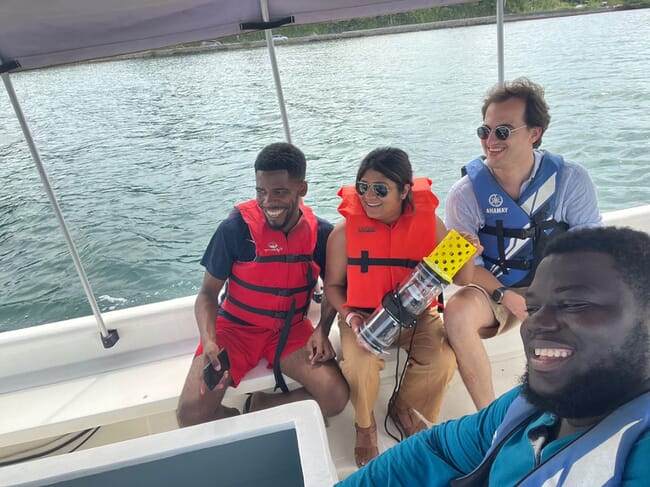
© Samudra
Economic viability
Das says that the sensor units cost between £10,000 and £20,000 each and come with a 5-year warranty – an offer that she says makes them well within the grasp of small-scale producers.
However, she envisages that the capex for the smart farms will require 30-year cashflows and therefore need to be funded by banks or private equity. However, she believes that farms that are able to produce over 1,000 tonnes – which should be feasible with a footprint of 40 hectares – could generate revenues of up to £10 million per year.
“It’s kind of like the solar farm ethos, as there will be three or four sources of revenue: there’s biomass sales, there’s blue carbon credits, there’s a part that will be converted into biochar, there could even be biodiversity credits for always keeping part of the farm intact as a habitat for others,” she explains.
“But, you won’t break even in the first or second years – it’s a five to 10 year commitment to scale up production,” she adds.
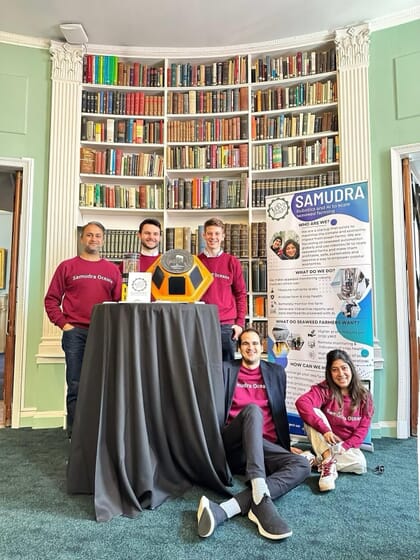
© Samudra
A startup’s milestones
Despite being only 18 months old, Samudra has been making impressive progress and already has 150 hectares for growing seaweed in Scotland and 200 hectares in Jamaica.
In terms of their technology, their first breakthrough was the validation of their sensors in the field – an achievement that was made possible by the European Space Agency, which provided a grant, office space and access to its satellites. The next was deploying their units at a functioning farm, in Cornwall.
“We did 22 tonnes there and saw there was huge demand for the seaweed, which we pre-sold six months ahead of time, which meant it was totally de-risked. And we’re currently sitting on huge LOIs [letters of intent] from across the world for quantities that could potentially de-risk every seaweed farm in the UK,” notes Das.
“The first season proved everything – market demand, our product actually helped, it sent back data, it lives in the water, it survives and you can scale up,” she adds.
The next challenges to meet relate to improving their sensors and deploying their first flatpack farm – which they aim to do before the end of the year.
“My suspicion is that it will be like our first product – some things will work, some things wont work at all, but by next year both our products will be super stable, and you will be able to have a fully smart farm or just some smart modules,” Das predicts.
“We want to have a few lines of products every few years that are pushing people along the automation journey in aquaculture,” she adds.
Key bottlenecks
Given the scale of Samudra’s ambitions, it’s little wonder that they are also facing numerous challenges. And Das says that she finds the amount of time required to thoroughly test the hardware quite frustrating – both for her and for potential investors.
“This is a plan that needs at least 10 years, so it’s a different type of investment and mindset needed – for a tech company not to have a 5-year exit strategy is quite strange,” she notes.
Working with the many variables of nature is another challenge.
“It’s possible that one of our farms could be wiped out by biofouling or changes in El Nino. The way we deal with that is by hedging, that’s why we will have so many large-scale farms around the world. We’re trying to see if our overall revenues are good enough to take one or two hits every year, because that is going to happen,” Das predicts.
Samudra has largely been funded by a combination of grants and VCs to date, but Das says that they are now looking towards development banks who are prepared to invest in infrastructure projects lasting 20 to 30 years.
As a serial entrepreneur – this is Das’s fourth venture – she has found it much easier to raise investment, with many of her previous investors prepared to trust her judgement. However, she admits that – despite this advantage – it’s not been straightforward.
“It’s 100 times harder than trying to raise for AI or SaaS [software as a service]. I now have to do 100 meetings to raise half a million,” she reflects.
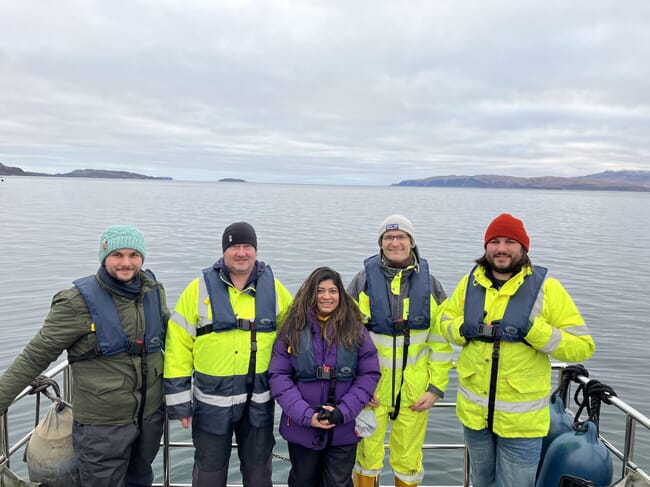
© Samudra
The blue carbon conundrum
While seaweed’s role in sequestering carbon for a meaningful length of time is debatable, according to Das the “steady state theory” suggests that the constant production of seaweed across multiple farms in multiple geographies really can have an impact.
“In five years’ time we want to have all of our farms up and running at a steady state. Which would mean we were constantly soaking in, let’s say, 10 megatonnes of carbon. It’s going into short-term cycles but if we’re keep all these farms on all the time – so, not matter what cycle they get in, there’s still 10 megatonnes of carbon taken out of the air compared to before we started. It’s like a factory – we’re constantly putting it out, but it’s also going through,” she explains.
It's an idea that, after six months of deliberation, Google Impact is now prepared to certify, according to Das.
Meanwhile, she adds, they are also looking at producing biochar and bio oils from at least some of their seaweed.
“That is what will feed into the direct blue carbon credits, which is what we’re selling now – it’s a very quantifiable form of carbon. We’ve just done a minor sale with the Kiloton Fund in Silicone Valley, and will probably do a lot more in the coming years. We’ll have 7-10 years to fulfil them and we can do this from any site. It’s a global scale,” Das explains.
“Right now the unit economics don’t work for the seaweed industry, as you’ll get paid max $600 per tonne, but at large scale automated seaweed production it will work for us,” she adds.
However, Das believes that there’s not a one-size-fits-all policy for seaweed producers.
“I don’t think we’ll do carbon credits in the UK for a long time, because the energy costs for processing biochar or bio oil doesn’t make the unit economics sensible. But I think we’ll be able to do it in the hotter countries like Jamaica, where there’s no drying costs and there are a lot of renewables, It’s possible we’ll do the carbon credits from Jamaica, Sri Lanka, India and Oman, while the cold waters of Canada and the UK we’ll just sell the seaweed biomass,” she concludes.