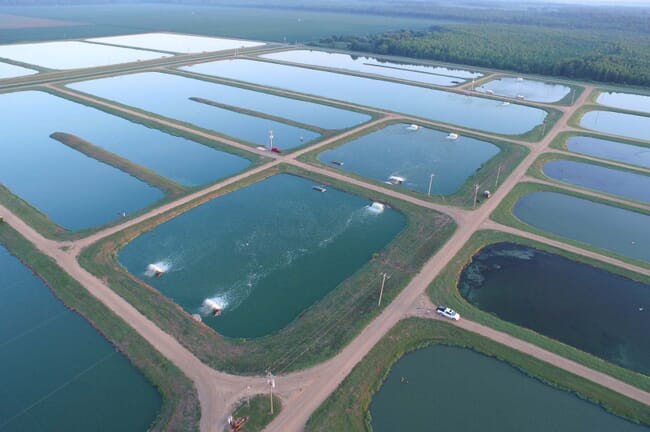
© Mississippi Agriculture and Forestry Experiment Station
Industry advocates point out that the country’s catfish farmers are now producing their fish on less land for lower costs, while also reducing environmental impacts.
Early beginnings
Many of the pioneers in US catfish farming were already aquaculture veterans, having been involved for years in pond culture of buffalo fish in Arkansas and surrounding states. By the late 1950s at least two buffalo farms in Arkansas had also started producing channel catfish. Over the following years more buffalo producers began switching to channel catfish, and interest in farming this species was widespread throughout the southern US. In 1964, Texas A&M’s Cooperative Extension Service published a bulletin by Wallace Klussmann titled Channel Catfish Farming. Over the next decade, states as far afield as Maryland and California developed their own guidance for would-be catfish producers. Today, however, over 96 percent of the US catfish industry is located in Alabama, Arkansas, Texas and Mississippi – with Mississippi accounting for over half of the harvests and acreage.
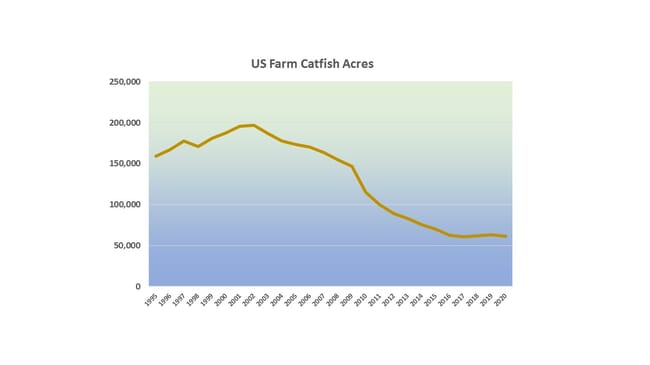
In the early years, single-batch stocking and complete harvesting was the norm. A crop of fish was stocked in late spring, fed through summer and fall, overwintered, and then fed to harvestable size (around 1 lb at that time). Recommended stocking rates of 1,500 to 2,500 fish per acre were the norm in the early 1960s, but production densities and yields gradually increased over time. This eventually led to the development of aeration machinery to allow further intensification. At first, farmers were reliant on tractor PTOs to power their aeration needs, but permanently placed electrical units soon appeared throughout the industry. Aeration designs improved and yields and stocking rates increased even further, as did feeding rates. Intensification resulted in many more disease problems than had been experienced in the early years. As a result, floating feed became the norm in order to monitor appetite and feed consumption as early indicators of impending disease problems.
Intensification also led to high levels of dissolved nutrients, and blue-green algae blooms and associated off-flavour problems throughout the industry. The frequency of blue-green related off-flavour posed significant cash flow risks for producers. If all of a producer’s ponds with harvestable fish were off-flavour at the same time there were no sales until the situation improved or the fish in on-flavour ponds grew to marketable size. Multiple batch stocking was adopted as a way to increase the odds of having some amount of harvestable size fish somewhere on the farm on any given day. In this production strategy, some portion of harvestable fish are removed from a pond and this partial harvest is followed by adding smaller fish. The result over several seasons is a population with a more-or-less continuous size distribution of fish, from very small to very large.
This harvesting strategy worked well because channel catfish are scale-less and their heads are the widest point on their bodies. They actively squeeze through the mesh of harvesting nets when concentrated into grading socks (live cars) attached to seines pulled by tractors and hydraulic reels. When harvesting channel catfish, farmers can determine what size fish they retain for sale by selecting the proper mesh size for the sock attached to the net. Undersize fish wiggle their way out and remain in the pond undamaged to continue growing and feeding. While this new approach provided farmers with more flexibility in marketing and maintaining cash flow in response to off-flavour incidences, a number of associated problems resulted. These included poor feed conversion ratios (FCRs), inventory inaccuracies, longer grow-out periods and high mortality levels. Annual harvests from multiple-batch ponds typically ranged from 4,000 to 7,000 lb per acre.
This was the prevailing reality for the catfish industry in the early 1990s – when ethanol production for use in gasoline suddenly became popular in the US. As the federal government mandated the inclusion of ethanol in gasoline supplies, corn inventories were diverted from feed production to ethanol plants. Corn prices rose rapidly and this in turn increased prices for soybeans. Although price impacts were somewhat less severe in some regions, in Louisiana floating catfish feed went from $225 per ton to $485 per ton in less than two growing seasons. Many smaller and less efficient operations could no longer turn a profit. As the numbers of catfish acres and farming operations both began to decline throughout the country, seafood importers took notice. The spike in prices and reduced domestic supply prompted some traditional farmed catfish customers to seek out other products, such as pangasius from Vietnam and channel catfish from China, as substitutes.
Relentless economic pressure, inefficient production practices, disease losses and deferred maintenance combined to force many producers out of the business. The industry gradually became concentrated in the hands of larger and more progressive producers who saw it as a business rather than a way of life. And, while the original catfish farming pioneers and their successors had often exhibited mistrust – or outright disdain – for research-based recommendations, the surviving segment of the industry openly embraced the promise of new practices and technologies as economic life-savers.
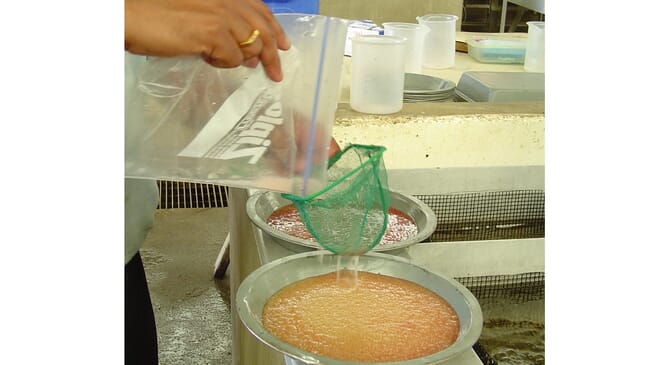
© Prof C Greg Lutz
Hybrid vigour
Currently, the industry and the researchers that serve it are focused on improving production efficiency and reducing production costs to strengthen producers’ competitive positions against imported substitutes. The mission is to produce more fish on less land, with less water and at a reduced cost. One major innovation has been a shift from pure channel catfish to channel catfish x blue catfish hybrids, which currently account for roughly 75 percent of production. Some advantages displayed by hybrids include faster growth, better feed conversion, higher carcass yield and a generally higher tolerance of crowded conditions and low oxygen levels. Hybrids are also more resistant to some of the more common pathogens on catfish farms.
However, hybrids also present some challenges. They are difficult to mass produce in hatcheries, because blue catfish and channel catfish rarely hybridize of their own volition in open ponds. Hybrid catfish production requires artificial fertilisation, with eggs being stripped from hormone-injected female channel catfish and testes dissected from blue catfish males and subsequently macerated. This approach is both labour- and equipment-intensive, with significant room for improvement in terms of fertilisation and hatching rates. And, as is the case with pure channel catfish, hatchery managers must operate within a limited spawning/hatching season, usually beginning in May and ending by late June. Ongoing research involves improved protocols for maturation and strip-spawning of channel catfish females, selection of individuals from both species that are more inclined to hybridize in open ponds, and genetic improvement of both species, with a focus on growth rate, carcass yield and disease resistance.
Perhaps an even bigger problem with hybrids is their incompatibility with grading socks. Their heads are smaller than the anterior half of their bodies, which discourages squeezing through the sock mesh and results in many fish being “gilled.” They also react to confinement in socks by becoming lethargic rather than actively seeking their way back into the pond. As a result, multiple-batch stocking and harvesting simply doesn’t work for these fish, and producers have been forced to go back to a single-batch management strategy. Fortunately, off-flavour is not as big an issue as it was when producers were initially forced to adapt multiple-batch stocking strategies, thanks to advances in algae control. The US Environmental Protection Agency has approved three compounds to reduce the blue-green algae responsible for most off-flavour problems in catfish farming.
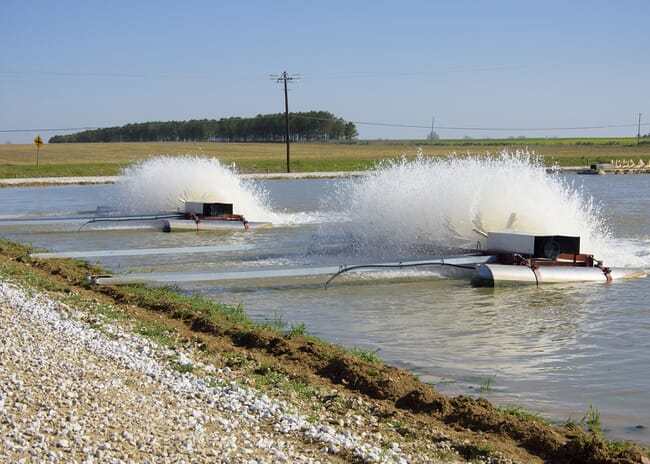
© MSU Extension Service
Nonetheless, when using single-batch management producers face seasonal oversupply at the end of the second growing season, even with staggered stocking dates and densities. Hybrids that are not sold upon reaching market size (approximately 1.5 lb) continue to put on weight fairly rapidly, and holding and feeding costs become significant considerations. If fish become too large, processors may be reluctant to purchase them or may offer a reduced price per pound. Although rapid growth in larger hybrids can be reduced to some extent by withholding feed, this significantly reduces fillet yields, making it even harder to find a buyer for late-season warehoused fish. One strategy being evaluated to cope with these seasonality constraints involves a three-phase grow-out cycle, similar to that used in many large tilapia farms and in hybrid striped bass production in the US and elsewhere. This approach is limited to some extent, however, by the cold winter conditions experienced roughly halfway through the production cycle.
Innovation
Innovative production systems are becoming more widely adopted across the industry – specifically, split-pond units and intensive aeration in traditional ponds. Split ponds are easily configured from existing production ponds. Ponds are divided into two separate sections in a ratio of roughly 80:20. The small section is used to raise fish, while the larger section serves to break down and cycle wastes generated throughout the grow-out process. As a rule, overall pond size should not exceed 4 to 5 hectares. A means of circulating high volumes of water between the two sections is required, as is a return channel or culvert. Once the pond is up and running the smaller section is stocked with the same number of fish that would normally be put into the entire pond area. Raising catfish hybrids in split-pond or high-aeration grow-out systems has been shown to increase production to 15,000 lb per acre and occasionally as much as 22,000 lb per acre. Producer interest in split-pond units is growing. Apart from allowing higher yields, they appear to also be more efficient at cycling and breaking down the wastes that result from intensive catfish production.