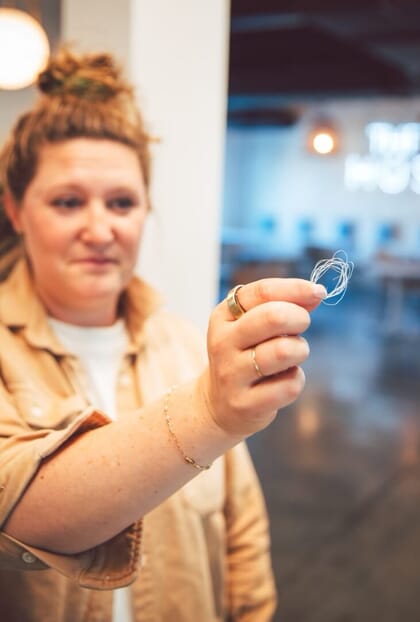
© Viable Gear
Can you tell us about the inspiration behind starting Viable Gear and your personal motivation to reduce petroleum-based plastics in our oceans?
In 2017 I watched the documentary A Plastic Ocean that asked viewers to take the plastic pledge for 30 days, which I decided to do. After 30 days I was so into it that I just kept going to see how much plastic I could mitigate from my day-to-day life. At this time, I got really into the global plastics crisis and started educating myself more about how plastics impact our health and our food system.
When I moved back to Maine in 2019, I was looking for a change in my career, which was in management consulting at the time. I was visiting an island that I grew up going to and was shocked at how much plastic debris was there compared to previous years. We picked up over 100 pieces of plastic – most of it ghost gear (abandoned fishing gear) – which inspired me to do something that would help reduce plastics in our ocean.
At this time, I became interested in seaweed and all the good that it does for our ocean. I assumed someone was making plastic out of it, but back then there weren’t many companies who had announced that they were using seaweed to replace plastic. I thought if no one else seemed to be doing it, then I might as well try! And that’s how Viable Gear was born.
How do you envision seaweed-based polymers making a significant impact on reducing ocean pollution caused by fishing and marine farming gear?
Right now, there are no good solutions to the traditional farming and fishing gear made from plastic and we hope to provide a solution to that. Having a material that will degrade after a span of time will be significant for ocean pollution. Not only does seaweed not shed toxic microplastics into the ocean, but our material will biodegrade, which will mean less marine species entanglements, and if ingested by a marine species the material can be digested and won’t be fatal.
Microplastics that shed from marine gear (and all other forms of plastic that end up in our ocean) get into our food system and can cause harmful health effects. Our seaweed-based material will help reduce microplastics that humans ingest through our food systems and clean up the sustainable protein sources that come from our ocean.
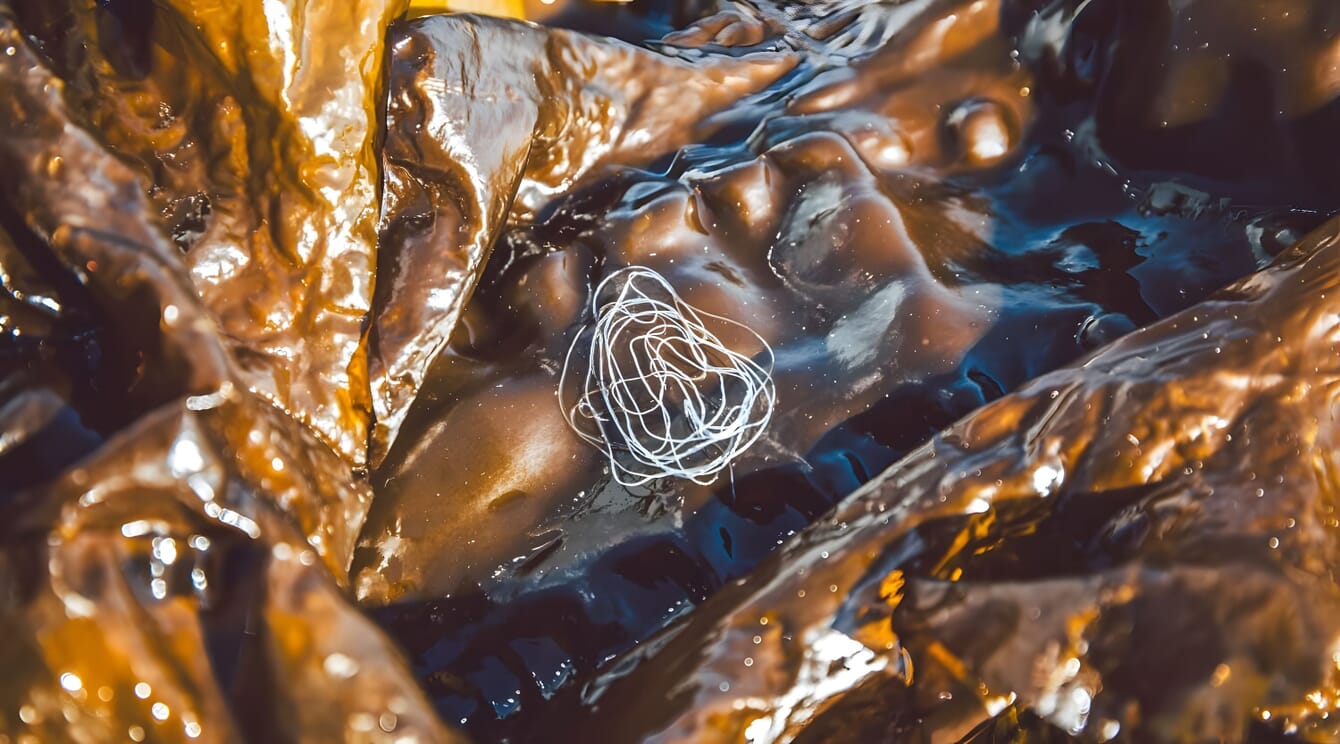
If everything goes well with this pilot product, Weiler plans to scale-up to produce bait bags for the lobster industry as Viable Gear's first product to market © Viable Gear
What’s the market opportunity for Viable Gear’s seaweed material products, specifically in the marine farming/aquaculture industry?
We are currently focused on our pilot product, which is a seeding twine made from kelp for use in seaweed hatcheries. This product will be part of the circular economy, as the cultivated kelp used to create our material will go back out to the farm at sea as seeded twine to grow more kelp!
If this pilot product works, then we will scale-up to produce bait bags for the lobster industry as our first product to market. There are an estimated 23.9 million bait bags used annually, from Massachusetts up through eastern Canada, with a market value of roughly $55.1 million, therefore it would be a huge opportunity for us to capture a percentage of that market.
Beyond bait bags for the lobster industry there is an opportunity for bait bags for the crab industry, mussel socking, scallop lanterns, and other tubular mesh gear.
As a startup, what stage are you at with the development of usable and marketable products for commercial use specifically in the marine farming/aquaculture industry?
Viable Gear is an early stage startup. We are still in the R&D stage, working on the best material formulation for use in the marine environment. We hope to pilot the seeding twine material in kelp hatcheries this coming autumn, which is contingent on funding and hiring a part-time polymer scientist.
What challenges are you encountering while developing the technology to produce marine farming gear from seaweed, and how are you overcoming them?
The biggest initial challenge for Viable Gear was finding the right engineer to work on the material. There have been a few paths of work with different consultants and a grant that directly went into the University of Southern Maine Composite Engineering Research Lab (CERL), which helped accelerate our R&D work. We were also introduced to Maine-based science and engineering company Everything Seaweed, who have over 30 years of seaweed engineering experience and have been a great consultant and partner in this work.
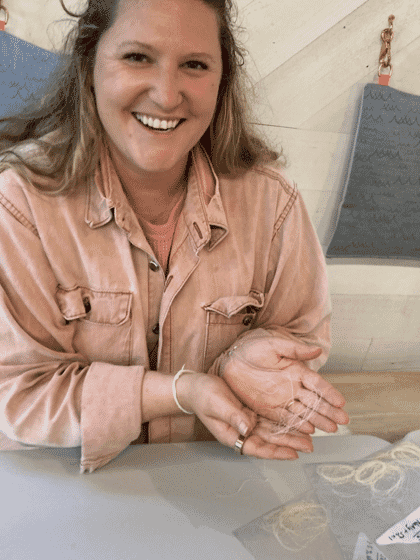
With natural polymers having a reputation that they aren’t as durable as traditional plastics, Weiler and her team are working on a formula that will prove that assumption wrong © Viable Gear
How does the durability and performance of seaweed-based polymers compare to traditional petroleum-based plastics commonly used in marine farming gear?
The biggest difference is that seaweed polymers are derived from a renewable resource and aren’t chemically manufactured, unlike the traditional petroleum-derived plastic polymers that are used in aquaculture gear today. Seaweed polymers aren’t toxic and when they biodegrade in the ocean the material breaks down naturally without repercussions, whereas petroleum-based plastic breaks down into micro- and nanoplastics and never ever fully goes away.
The actual gear performance is what we are working on right now in R&D. Natural polymers have a reputation that they aren’t as durable as traditional plastics, but we are working on a formula that will prove that wrong. We know the gear needs to be strong and last for a long time, until it would need to be replaced. The goal of our material is to ensure that it can be composted rather than discarded at the end of the gear’s life.
What steps is Viable Gear taking to ensure the sustainability and scalability of seaweed sourcing for the production of your products? Who are you collaborating with to source the raw materials needed to produce your products?
As we move forward, Viable Gear has scaling and sourcing at the top of its mind. We want to create demand for more seaweed cultivation off the coast of Maine and New England, but for that to happen we need a better and faster system for leases to be approved for farmers who want to grow seaweed.
Our material also depends on a biorefinery process and there currently isn’t one on the east coast of the US, so we are working with the UK right now. Fellow Maine-based company Everything Seaweed has a goal of building a biorefinery in Maine and we’re working with them directly, so that is very promising for our supply chain and the carbon footprint of the product. Transporting the seaweed to a local biorefinery and then manufacturing the products in the same area is the ultimate goal to really reduce transportation impact.
How do you plan to collaborate with other stakeholders, such as governments, environmental organisations, and the aquaculture industry, to accelerate the adoption of seaweed-based polymers in the sector?
Viable Gear has been trying to stay connected and get involved with the aquaculture sector since we started in 2021. Our goal is to stay as close to this industry as we can as partners and beneficiaries of this important and growing seaweed space, as well as others in the oyster and scallop industry, to learn as much as we can about the gear they use and how we might be able to make something equally as good – or better – for their fishing and farming practices.
Viable Gear is connected to NOAA and has applied for grants from them that tie into their mission around plastic debris and growing aquaculture. We’ve also had some interaction with our state government to start cultivating a connection, so when we do get a product to market, we might be able to work together around stipends that would make the initial product more affordable for fishermen and farmers to transition over to using.
From the start I've always said the more people we can talk to the better. We continue to connect with individuals from other startups using seaweed materials and to lobstermen who’ve been in the industry their whole lives. We have an established fishing gear distributor, Brooks Trap Mill, who is ready and willing to distribute our bait bags for us when the time is right. Once we get our material on the market we want people to know about it and believe in it, therefore getting the trust of distributors and fishermen is a great place to start.
How do you anticipate the aquaculture industry embracing the use of seaweed-based polymers in their farming practices?
The products are going to need to be price competitive and work the same as gear made from petroleum-based plastics – those are the two most important elements we’re focusing on. A lot of lobstermen are growing seaweed in the winter, so they support the industry and want to see it continue to grow. I think if we hit those first two elements then the industry will really embrace our product.
What sets Viable Gear apart from other companies in the market working on similar solutions?
Most companies that are working on replacing ghost gear are using land-based crops for their materials. But we are using macroalgae, which doesn’t require the land or water input needed to grow crops on land, therefore we have a lower carbon footprint. In addition, seaweed acts as a carbon sink and helps fight ocean acidification, and with the Gulf of Maine warming 99 percent faster than the rest of the world’s oceans we need all the help we can get!
There are many hugely inspiring companies – such as Loliware, Sway, Notpla, and Keel Labs, to name a few – who have seaweed-based products on the market that reduce land-based plastics. However, Viable Gear is creating a product to replace the plastics that are made to go directly into the ocean, so we aren’t directly in competition with these companies. There is so much plastic mitigation and replacement that is needed that we are excited about anyone who is working on this mission!
What is your long-term vision for Viable Gear?
Viable Gear is hoping to get a few products on the market – starting with kelp seeding twine and bait bags – and prove that our material works to replace nylon used in the marine environment. Once we have that stream of work, we hope to be able to make enough material to sell to other extrusion plastic companies so they can make products out of Viable Gear’s material and we can start replacing more plastics across other product lines and industries.
Viable Gear has a future product goal to replace zip ties that are heavily used across fishing, aquaculture and recreational marine industries, but that will require some changes to the manufacturing and the material formulation – they’ll be more about that in the future!