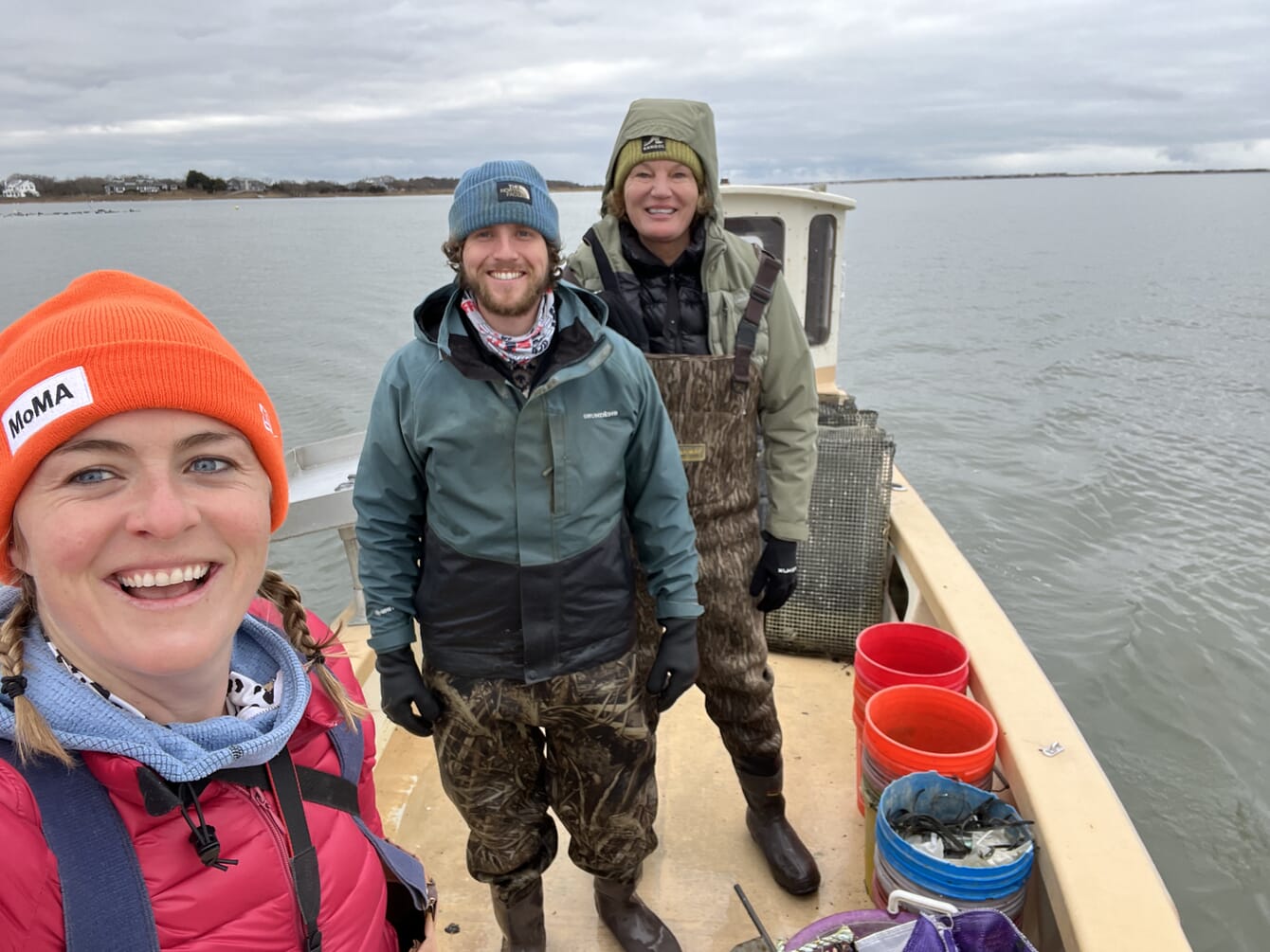
Alexandra Talty visiting Sue Wicks' oyster and kelp farm © Alexandra Talty
Standing tall in her insulated camouflage waders, Sue Wicks motors for 20 minutes across steel-blue water in her Pickerel clamming boat. During the winter, this is Wicks’ weekly commute to check her kelp lines on Long Island’s Great South Bay. There’s likely to only be an inch of growth, but Wicks checks in on her crop at least every week until it is time to harvest in the spring.
“In my heart of hearts, it is all about water quality,” says Wicks, founder of Violet Cove Oysters, an oyster and kelp farm in New York. She was inspired to start farming kelp when she learned about the seaweed’s ability to fight ocean acidification and eutrophication.
“I have a spot in my heart for the baymen out there,” Wicks reflects, using the local term for commercial fishers who earned their living clamming, scalloping, fishing and oystering on Wicks’ beloved bay during her childhood.
Wicks first ventured into seaweed in 2019, when she began working with Stony Brook University to trial sugar kelp farming. At the time, marine scientists at Stony Brook University wanted to see if they could grow kelp in Long Island’s shallow waters. They thought it could be a good additional revenue stream for the island’s oyster growers and would help improve local water quality. One of two participating oyster farmers, Wicks worked closely with the scientists and quickly fell in love with kelping.
“Not only does the addition of seaweeds provide oyster farmers like Sue with an additive revenue stream, it can also help protect oyster crops from the effects of ocean acidification,” says Michael Doall, associate director for shellfish restoration and aquaculture at Stony Brook University.
Doall helped devise the shallow water kelp-growing technique that Wicks trialled and now uses on her farm. Lines are inoculated with sugar kelp spores, laid close to the sandy bottom and tied off between two stakes. Prior to Doall’s innovation, it was believed that sugar kelp could only grow in deep water.
After a two-year wait for a permit, Wicks became New York State’s first commercial kelp farmer in 2023 and would now like to see other Long Island oyster farmers follow her lead.
She is part of a growing wave of seaweed farmers across the United States; in 2024, there were 108 active farms according to Connecticut Sea Grant, up from a handful in 2015.
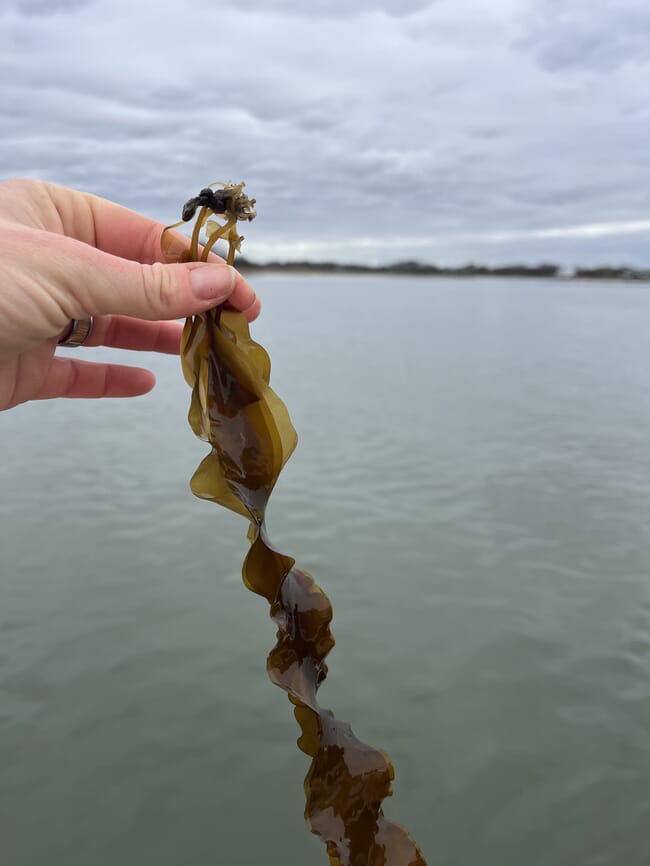
© Alexandra Talty
But becoming the first commercial kelp farmer in New York had its challenges. In addition to the lengthy permitting process, involving both the state and US Army Corps of Engineers, Wicks needed to build processing infrastructure and a market for her product.
Sugar kelp processing can be quite expensive: Atlantic Sea Farms, the leading kelp food company in the US, recently invested over $2 million into their drying facilities – a figure that Wicks couldn’t justify.
As a result, she decided to work with the non-profit Lazy Point Farms, Suffolk County and the Town of Brookhaven, in a bid to build something that was low-cost, as close to net-zero for energy input as possible and could be shared with other kelp farmers in the region.
In order to keep energy costs down, she designed a drying rack where kelp could air dry - losing 80 percent of its original volume. Kelp would then head to her dehydrator, which was built out of an old shipping container. It uses solar panels to power the header, exhaust fan and dehumidifier. In total, it cost $50,000.
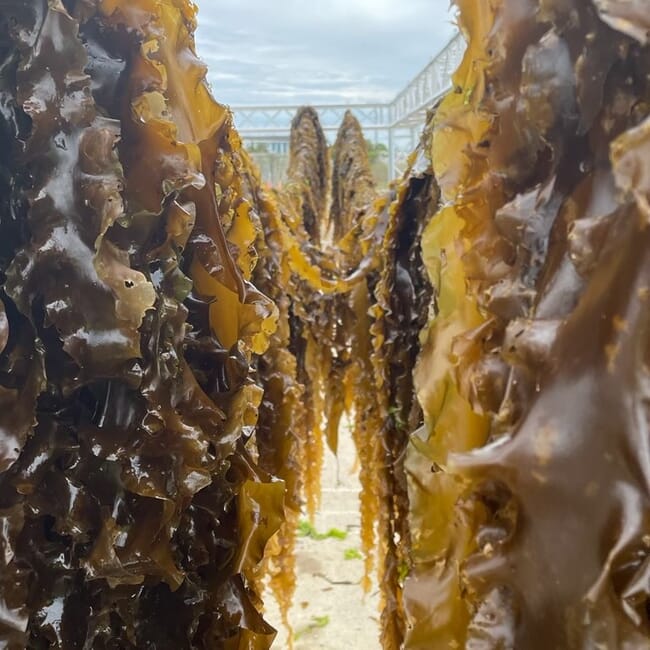
Initially air dried on a unique drying rack, Wicks' kelp is then transferred to a specially designed low-energy dehydrator © Sue Wicks
“The most important part - we have tried to do this zero net energy,” says Wicks. Pointing out that the design is economical and possible to reduplicate, she says the system was created with “the intention that others may use it as well.”
“We put together a business… with a not-for-profit, with organised labour, with two different governmental agencies… in approximately six months and got it done… in government work, that’s lightning fast,” said Suffolk County legislator Jim Mazzarella. “There’s really one reason for that: because all the players really care deeply about what it is that we are trying to accomplish here - expanding this amazing industry, the sugar kelp industry.”
A sporting pedigree
Wicks became an oyster farmer eight years ago, after retiring from a successful career playing professional basketball in the WNBA. Her family has long ties to Long Island’s South Bay - she is the tenth generation of Wicks to live and sustain themselves on these waters. After witnessing the decline of the bay in the 1990s, she was inspired to start farming in the waters where her ancestors fished.
The 151 square mile bay once produced the most hard shell clams in the world, but its fortunes declined over the course of the 20th century, thanks to a combination of warming waters, over development and pollution.
When Wicks applied for her four-acre lease, she had to prove to New York State that her plot was not usable for commercial fishing. Although it was her father’s favourite clamming spot, by the 2010s, it was quite desolate. But Wicks knew she could build something there.
Once she started farming, she saw rapid improvements in water quality. “The oyster cages have a nursery effect and provide habitat,” says Wicks, who has witnessed an increase in marine life like flounder, seahorses and hard shell clams. “When we did kelp I saw even more.”
With her dehydrator built, Wicks is making a kelp fertiliser out of her 2024-2025 crop.
“This year, we’re building on the success of our first commercial harvest, expanding our kelp fields with hopes for a bumper crop,” says Wicks. “We’ve doubled our planting and are expecting a substantial harvest this year, which will help fuel our ongoing experiments in bioplastics and expand our production of both dry and liquid fertilisers.”