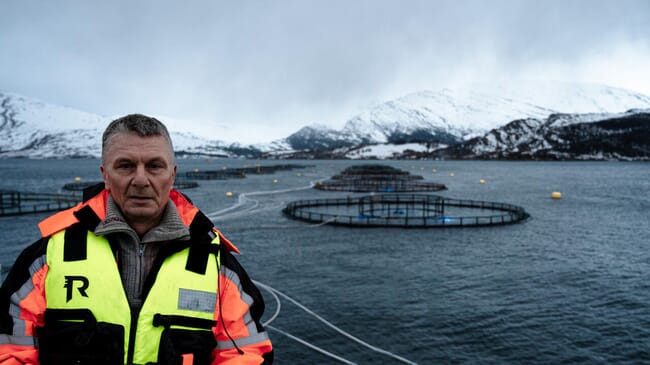
The aquaculture industry generates up to 12,000 tonnes of plastic waste annually, most of which can be recycled or reused. © AKVA group
Aquaculture equipment specialist AKVA group has been on a mission to prove that plastic from previous fish farm facilities can meet Norwegian regulatory requirements for the industry. AKVA already uses recycled materials and plastics in the walkways of net pens but is hoping to decrease its use of virgin plastic. With this in mind, they’ve been collaborating with groups like Plasto and Oceanize to investigate how recycled plastics could work in aquaculture systems. Initial feasibility studies have been promising – but suggest that manufacturers must control the quality of recycled plastic before it can be incorporated into net pens.
In February 2023, Nova Sea started collecting discarded plastic pens and bringing them to a collection point on land. Oceanize deconstructed the pens and transported them to Rørvik for granulation. The granulate was sent to Plasto to produce staples and then to AKVA group's facility in Mo i Rana to produce pipes. According to a news release from AKVA, the company plans to assemble a full net pen made from recycled plastic and deploy it with a customer.
"By establishing short, national value chains with all players in Norway, AKVA group is helping to reduce the environmental impact of the fish farming industry... By using recycled plastic in the production of pens, we are utilising discarded pens in a high-quality way and reducing CO2 emissions from pen production by two-thirds," says Jøran Strand, an engineer and sales manager for AKVA.
The aquaculture industry generates up to 12,000 tonnes of plastic waste annually which can be recycled or reused. By handling plastic waste nationally, it can potentially reduce greenhouse gas emissions by up to 50 million kg CO2 by preventing combustion and export of resources.
Comprehensive testing
According to Dag Ove Antonsen an engineer for AKVA group, tests show that clamps made of recycled plastic provide good strength – and that they are actually better than those made of new material. In addition, pipes extruded from recycled material show good strength and flexibility and are easy to produce.
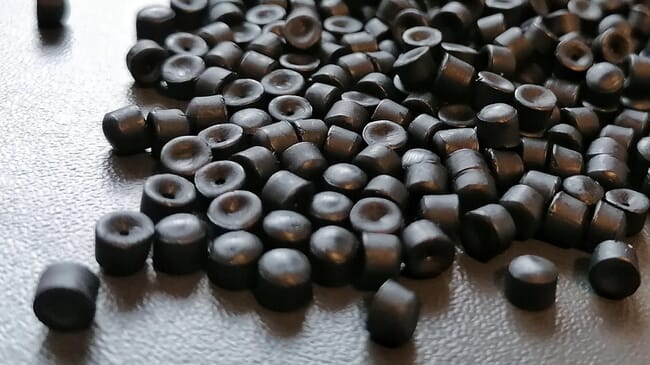
Pilot tests show that clamps made of recycled plastic provide good strength – and that they are actually better than those made of new material. © Oceanize
Extensive quality control measures and quality assurances are needed before using recycled plastic, and it can be difficult to know what the precise plastic quality the industry is working with. Some plastic components are better suited for recycling than others. Feed hoses that are full of fat and certain walkway plates with a different plastic type are examples of parts that are less suitable. In floating pipes, PE80 was used until around 2007 when it was replaced by PE100 which provides higher strength and stiffness.
"For every process where the plastic is heated to its melting point, there is a breakdown of additives. To ensure that the plastic is suitable for recycling even more times, new additives such as antioxidants and UV protection are added to achieve the best possible plastic quality," says Antonsen.
AKVA group aims to give plastic eternal life. Although the recycled material often becomes a mixture of PE80 and PE100, it turns out that the material quality is well suited for floating pipes, clamps, walkways, railings and other components.
"This is a key component in the company's long-term sustainability strategy. I look forward to joining the journey ahead," says Strand.