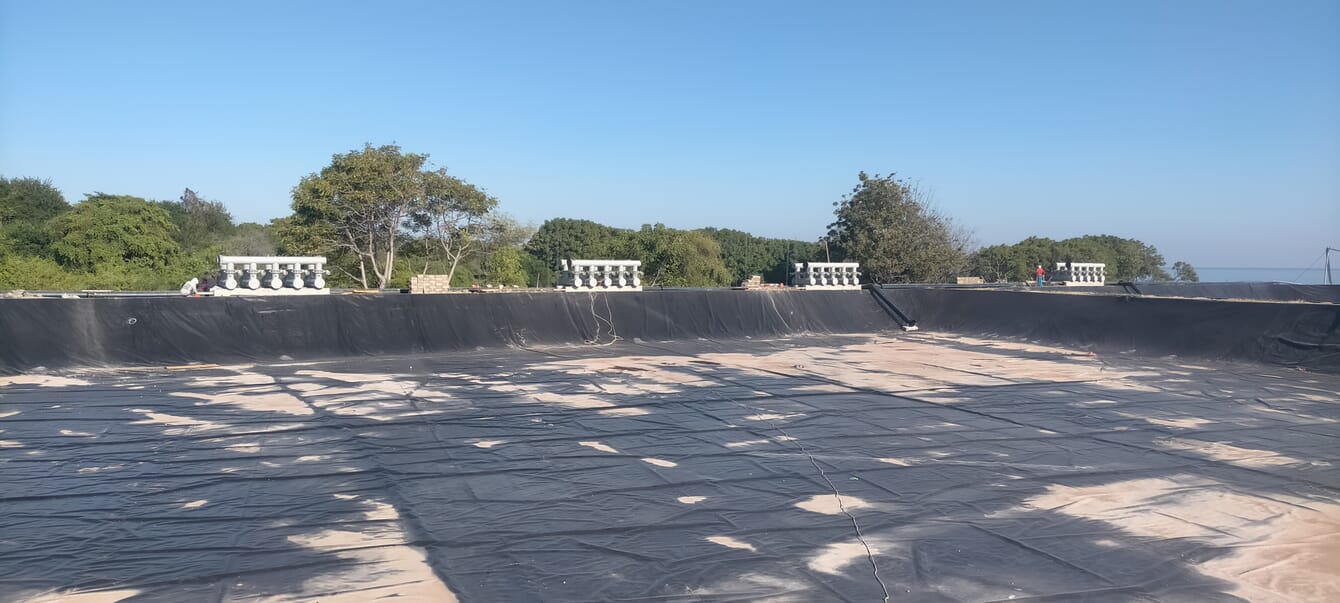
UVC – a specific type of UV – is effective as a disinfection treatment due to its ability to kill pathogens by damaging their DNA structure, therefore preventing them from replicating and losing their ability to cause diseases © ATD Suri Tani Pemuka
After being successfully used as part of water disinfection and sterilisation systems in shrimp hatcheries in Indonesia, ultraviolet (UV) technology is now being considered for use in shrimp grow-out ponds too.
The reasons for considering UV technology include enhancing biosecurity, decreasing prevalent shrimp diseases, reducing long-term water management expenses, and adopting an eco-friendly practice.
These factors are weighed against the conventional use of chemicals, such as chlorine or hydrogen peroxide (H₂O₂), which have been the primary disinfection choices for shrimp ponds so far.
Success in Bali
Several Indonesian farmers have begun experimenting with UV technology, including Sidiq Bayu Kurniawan, a shrimp farmer from Bali. He has been using UV technology from FisTx Indonesia over the last two cycles. According to him, UV treatment has significantly reduced the presence of Vibrio compared to the water he sources from the sea.
In addition, he says that employing UV technology brings efficiencies in terms of both space and expenses. Previously, the production system required a specific pond for chlorine treatment. But with UV, Bayu can treat all intake water directly with UV and channel it straight into the production ponds without needing a separate treatment pond. This method doesn't need a lengthy wait to prepare the water before it's ready for cultivation. Furthermore, the UV system is integrated with a sand filter which can enhance water clarity and maximize UV effectiveness.
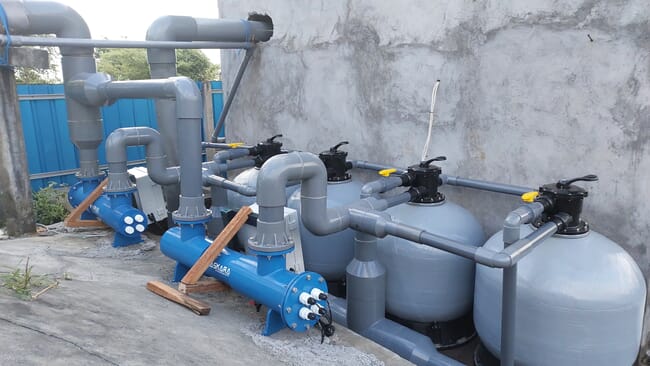
Combining UV and sand filters enables direct seawater intake, eliminating the need for a reservoir © FisTx Indonesia
Looking at costs, Bayu claims that there are substantial long-term savings. Although the initial investment in UV technology is significant, he notes that it substantially reduces ongoing production costs for chlorine and H₂O₂. He says that the expenses incurred using chlorine over two cycles is nearly equal to the initial UV investment cost.
The Aquaculture Technology and Development (ATD) PT Suri Tani Pemuka, subsidiary of Japfa Group, is actively exploring the development and implementation of UV technology in ponds. According to ATD manager, Muhammad Fuadi, chlorine tends to leave residues and leads to resistance in pathogens, necessitating increased doses in subsequent applications.
As Fuadi explains: "For responsible aquaculture practices, we're considering UV as an alternative to chlorine or other chemicals that could compromise the quality or balance of our ecosystems. Meanwhile, UV does not produce residue.”
A layered approach
However, it's important to note that UV disinfection solely represents a biological approach, with chemicals such as chlorine still forming a necessary part of the sequence of water treatments to maximise its effectiveness.
Ideally, UV treatment is applied post-physical treatment and before being distributed to the pond. UV's limitation lies in its need for specific water quality, primarily in terms of turbidity parameters, to ensure that UV rays penetrate microorganisms.
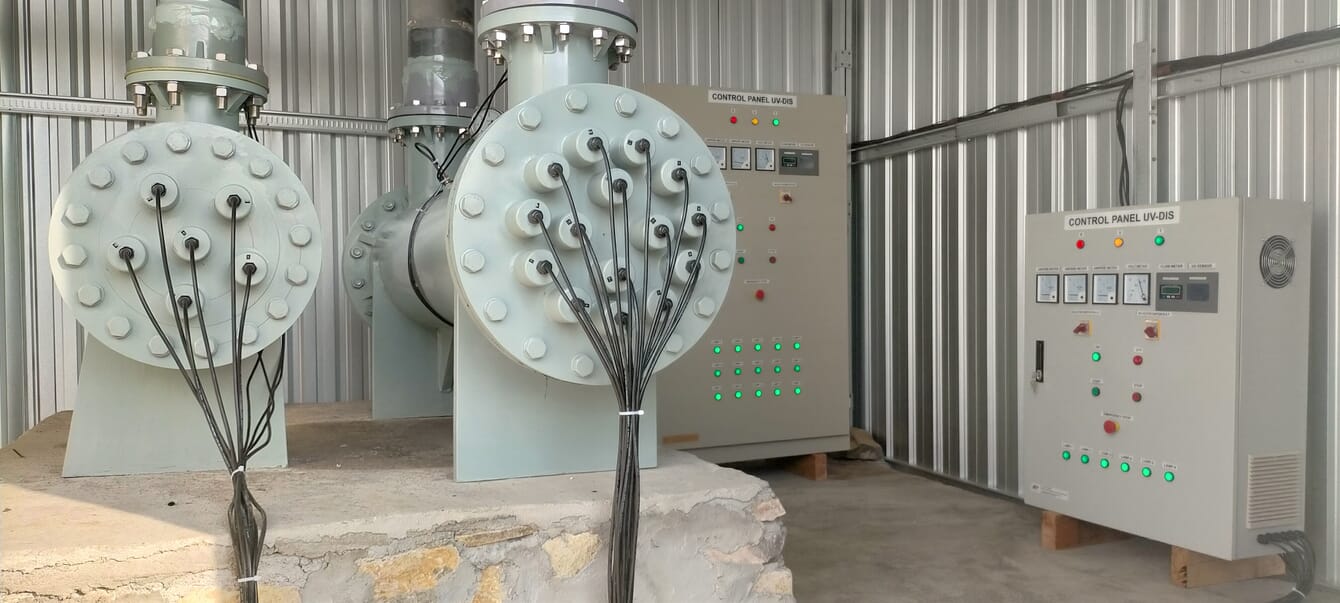
Although initial costs are high, installing a UV treatment system is highly cost effective in the long run, with farmers able to reach a break-even point within three cycles © ATD Suri Tani Pemuka
Ensuring treatment efficacy
UV is a type of electromagnetic radiation with a wavelength shorter than visible light but longer than x-rays. When it comes to disinfection, a specific type of UV, called UVC, with a wavelength between 250 and 265 nm, is utilised. UVC is effective in killing pathogens by damaging their DNA structure, preventing them from replicating and losing their ability to cause diseases. Importantly, it doesn't destroy the cell walls, ensuring that toxic substances within the microbial cells do not escape into the water.
Several companies have developed UV systems suitable for treating pond intake water – the two main options are the open channel and the enclosed system. Both have distinct pros and cons.
The open channel system, which is designed to work with gravity-based ditch setups, tends to be more cost-effective for both installation and maintenance. In this system, chambers are typically set up to follow the water path from the reservoir or directly from the sea to the cultivation pond. However, relying on gravity alone might not push the water effectively, leading to settling and inadequate disinfection. Moreover, the open setup means that disinfected water flowing into the pond could potentially be exposed to pathogens.
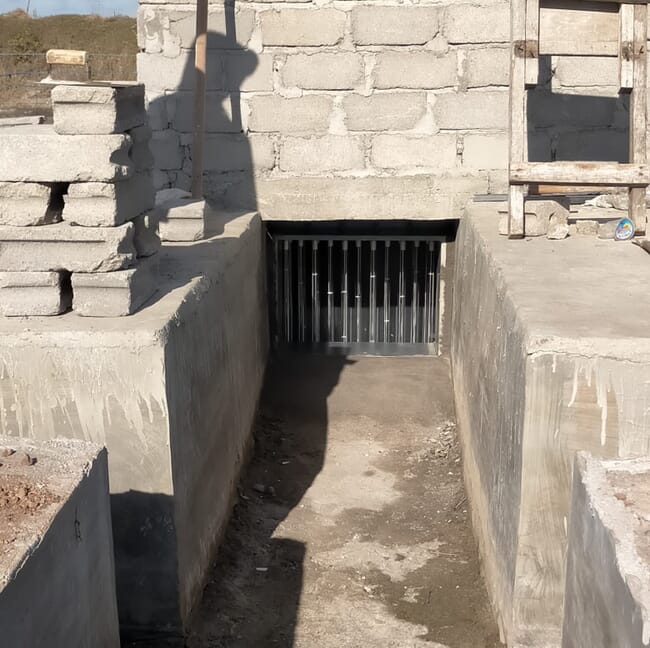
The open channel system is designed to work with gravity-based ditch setups, in which chambers are set up to follow the water path from the reservoir or directly from the sea to the cultivation pond © ATD Suri Tani Pemuka
On the other hand, in a closed system utilising pipes as chambers, a pump generates high pressure to move water efficiently through the chamber housing the UV lamp. This method avoids issues with pathogens splashing or untreated water. Nonetheless, the high water pressure might affect the durability of UV lamps. Additionally, long-term calcification of pipelines can cause blockages and increased water pressure.
As Fuadi explains: "Excessive pressure can harm the UV system, especially the sleeve and UV lamp. Typically, this pressure concern can be addressed by placing the UV system far from the pump or close to the cultivation pond."
He indicates that, besides the type of UV system, a number of factors impact the effectiveness of UV treatment. These include the application dosage, which involves the UV intensity and retention time of the water, which should be correlated with pathogen targets.
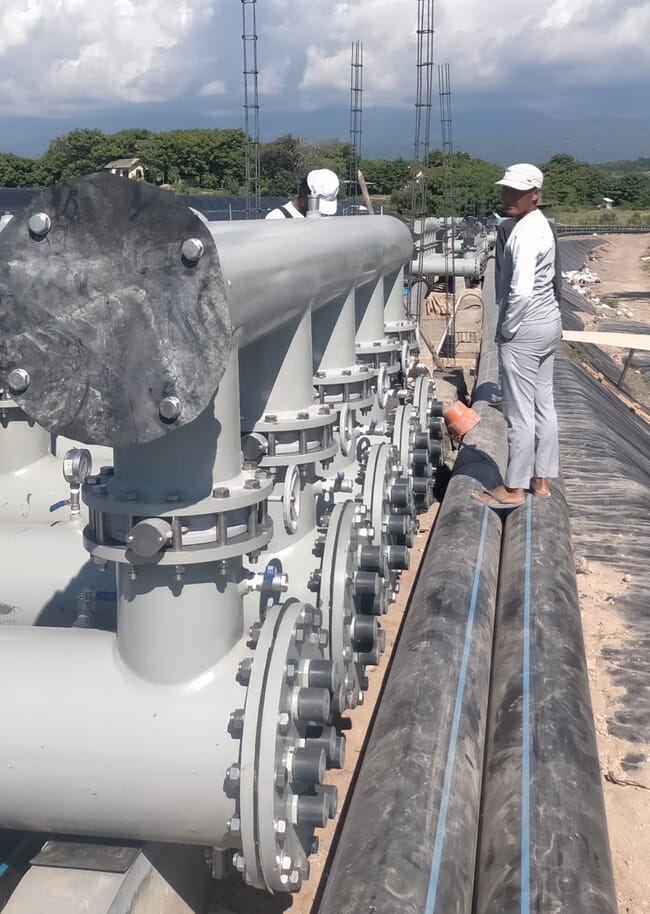
According to ATD manager, Muhammad Fuadi, using UV technology is around 16 times more cost-effective compared to chemical disinfectants © ATD Suri Tani Pemuka
For instance, he says that combatting Vibrio parahaemolyticus (the causative agent of EMS/AHPND) typically necessitates 70-100 mJ/cm2 for effective treatment, but some farmers prefer to use up to 300 mJ/cm2. Within Fuadi’s company’s own farms, he even operates at levels up to 1000 mJ/cm2 due to the lack of an international standard.
“In our analysis, we often encounter varying suggested dosages for the same organism across different journals. Therefore, we usually lean towards assuming the higher dosage, considering the consistent chemical and physical profile. While this decision generally doesn't cause issues, it might increase the required investment,” Fuadi states. "Typically, we use 300-350 mJ/cm2."
Additionally, he notes the importance of pre-treatment strategies such as maintaining turbidity below 15 nephelometric turbidity units (NTU) , total suspended solids (TSS) below 20 mg/l, and chemical oxygen demand (COD) below 20 mg/L.
Long-term efficiency
Fuadi agrees with the farmers’ statements regarding the cost-effectiveness of using UV. Based on his calculations, UV employment is around 16 times more cost-effective compared to chemical disinfectants.
"Even though the initial capex [capital expenditure] is significant, in the long run, it only requires electricity expenses in terms of opex [operational expenditure]. This opex is much cheaper than the costs of using 30 ppm of chlorine or TCCA [trichloroisocyanuric acid] in each cycle. UV maintenance is not significantly high, mainly concerning the UV sleeves or lamp containers, as they tend to degrade over time when exposed to seawater," he explains.
"So, if we compare head-to-head between chlorine or TCCA and UV, to reach the break-even point, it can be achieved within three cycles. Roughly in a year, assuming the average survival rate is around 80 percent," he adds.
Cost efficiency also depends on the dosage, as tailored to the farmer's needs. Determining the right dosage and investment value relies on the pond's condition and its history of diseases. The intensity of the UV lamp isn't constant as it needs to adapt to different locations affected by varying water compositions, past farming methods, previous disease occurrences, and the rate of water circulation. Hence, the installation should always be customised, according to specific needs.
Mindset challenges
Sidiq Bayu Kurniawan notes that using UV technology doesn't present significant issues overall. The primary challenge revolves around technical maintenance, particularly with components like the sleeve, due to a lack of familiarity with this new technology.
From the producer's standpoint, the key hurdle is educating farmers or farm managers about this technology. Some pond managers or technicians tend to stick to the status quo, even if the owner expresses interest in adopting UV. Conversely, some farmers have higher expectations for UV. But Fuadi always stresses that while UV offers various advantages, it's just one part of the production system. Other factors like nutrition, seed quality and biosecurity play equally crucial roles.