Phosphorus is essential for all life and is required for optimum growth, feed efficiency and bone development. Whilst an essential nutrient in aquaculture feed it also has an environmental impact and is responsible algal growth and oxygen depletion in many lakes and rivers.
Global salmon and trout production in 2019 was estimated to be 3.25 million tonnes per annum. This production is dominated by Atlantic salmon at 2.6 million tonnes, of which approximately 50 percent is produced in Norway. Salmonid production historically, like most farmed animal species, does not have a great track record in terms of environmental impact, although huge amounts have been done by the industry to clean up its image. The salmon industry in Norway produces ~1.3 million tonnes of salmon and ~1.7 million tonnes of salmon feed. This industry is also the third largest importer of inorganic phosphorus (P) (16,500 tonnes), even surpassing domestic P fertiliser usage.
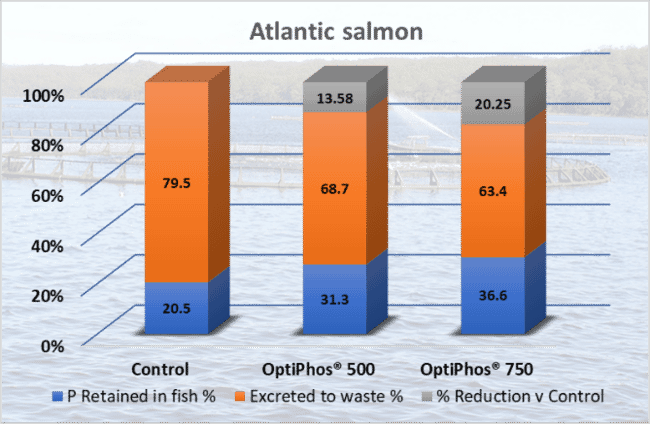
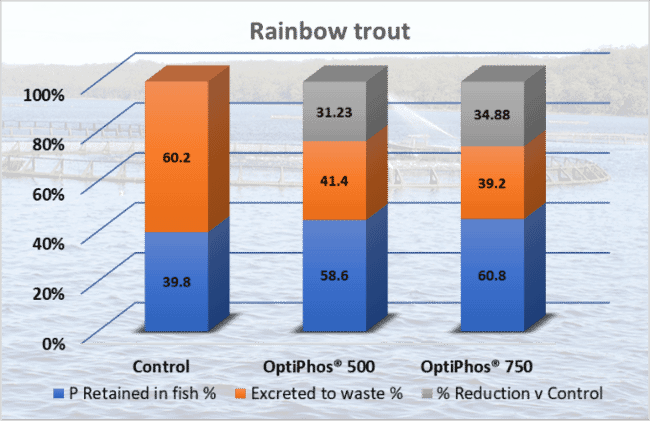
The salmon aquaculture industry in Norway is estimated to discharge ~9000 tonnes of P into the environment and this is deposited into the ocean, causing eutrophication, which contributes to coastal algal blooms. These can have crippling environmental effects and cause self-inflicted financial hardship to the farms through loss of stock, as the algae can also be responsible for salmon production losses.
The goal of sustainable aquaculture production is still far from being achieved, with fish retaining only ~40 percent of the phosphorous content of modern commercial fish feeds. Reduction of phosphorous levels in feed without impacting growth, feed efficiency and health is key to the development of low pollution diets. This is currently being achieved by the use of low-ash fishmeal, highly available phosphorous supplementation, but there are other more cost-effective strategies. Phytase enzymes that efficiently release unavailable phosphorous from the increasing inclusion of vegetable ingredients have a very important role to play.
Large amounts of organic phosphorous bound in phytic acid are present in modern day salmon and trout diets but these are poorly utilised. This represents an opportunity to utilise OptiPhos, a globally recognized phytase enzyme to help reduce environmental impact to the salmonid industry.
Recently conducted rainbow trout (Onchorhynchus mykiss) and Atlantic salmon (Salmo salar) trials demonstrated that phosphorus levels in the feed can be reduced significantly (range 2.5 – 3.5 g/kg) and that in some cases added inorganic P sources could be eliminated completely. This not only has the potential to reduce the environmental discharge of P by ~3200 tonnes in Norway alone,
There are also financial benefits in implementing an OptiPhos strategy. Increasing digestible energy (DE) levels in salmonid feeds has a significant impact on space in formulations. Competition for space can add significantly to formulation cost so any opportunity to optimise space utilisation will provide a significant cost benefit. OptiPhos, by reducing the necessity for phosphorous supplementation can offer formulation cost savings of up to €15 per metric tonne, a win for both economic and environmental sustainability. This excludes any opportunity the farmer may have to increase production volumes and make better use of production biomass consents, which could be significant.
Key facts
- OptiPhos at 500-750 OTU/kg significantly reduces P discharge in trout and salmon.
- OptiPhos can significantly reduce the current usage of MAP/MCP in salmonid feeds.
- OptiPhos helps minimize the environmental impact of salmonid aquaculture into water courses and significantly reduces carbon footprint of inorganic phosphorus production and transportation.
Feed application of OptiPhos
The application of OptiPhos to extruded feed is an important consideration to ensure optimum performance and to avoid loss of activity of this heat sensitive enzyme due to high extrusion temperatures. OptiPhos is therefore supplied in a liquid form and supplied in 1,000 litre IBC’s to allow for post extrusion application during the fat coating phase of production.
As well as IBC’s, Huvepharma have developed a new and fully automated enzyme application system called Huvematic which allows the use of highly concentrated water-soluble powder enzymes (WSP). The Huvematic machine produces liquid enzymes onsite and on-demand, operates fully automatically, and can be incorporated in the feed mills automation and oil addition system, allowing feed production to be truly optimised.
The Huvematic enzyme dosing system
Producing liquid enzymes on-site replaces the need for shipping, storage and receiving liquid enzymes in IBC containers, resulting in cost savings, added labour and warehouse space and drastically reducing your carbon footprint.
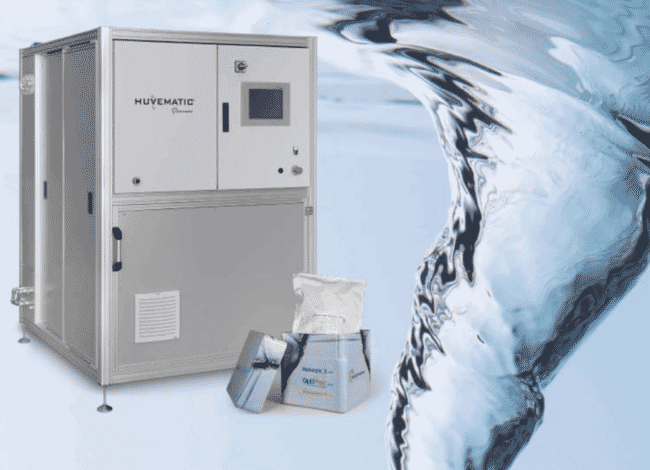
For more information on OptiPhos or other Huvepharma products and applications, please contact Robert Serwata, global product manager enzymes at robert.serwata@huvepharma.com