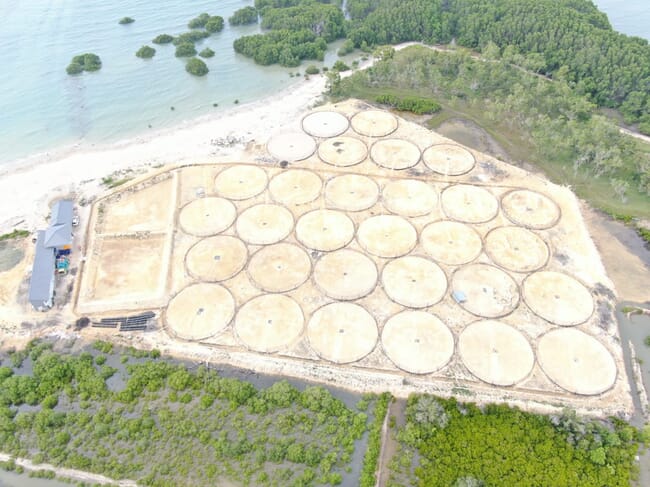
© Rizky Darmawan
Indonesia is one of largest shrimp producers in Southeast Asia. Initially, in the 1980s, black tiger prawn (Penaeus monodon) was the most widely cultivated species and most farmers favoured the use of large rectangular ponds, with an average area of 2,500 – 5,000 m2.
When most changed to vannamei production in the early 2000s, due to whitespot (WSSV) disease outbreaks that hit monodon horribly, the type of shrimp pond changed little, other than the addition of HDPE linings or concrete to the ponds.
However, in the last decade the shrimp farming model has begun to vary, including the construction of some smaller ponds, of 1,000 m2 or less. The popularity of these mini-ponds was a response from those who want to be involved in the sector but have limited capital and land. Originally, these small ponds adopted the traditional rectangular shape, based on a very simple construction using bamboo as the frame and tarpaulin as its lining. This type of pond was developed by farmers in Madura, East Java, in their backyards.
Recently, the trend of small-sized shrimp ponds has shifted towards circular designs, typically with a diameter of 5 to 30 metres. This type of farm is popular among young farmers, while the government and private companies are also participating in developing this kind of pond as a pilot for millennials and small-scale farmers.
Finding the best way
One of the farmers who has been experimenting with circular ponds is Rizky Darmawan. This millennial farmer, who is also the chair of the Indonesian Young Shrimp Farmers (Petambak Muda Indonesia/PMI) has been developing circular designs since 2019 at his existing pond area in West Nusa Tenggara (NTB). He was inspired by Erwin Budiman from Medan, North Sumatra, a fellow farmer who had started using this design in 2016 and is now the chair of Shrimp Club Indonesia (SCI) Medan chapter.
"We built our first two circular ponds in 2019. Our ponds are now entering the fourth cycle. Initially, we decided to build circular ponds to fill the narrow strip of remaining land in our pond area. At the same time we did it to conduct R&D at our location,” he says.
He’s also trialling using the circular ponds for his shrimp nursery, as he can easily transfer the juveniles to the large ponds for grow-out.
He currently operates 10 circular ponds, with an average diameter of 20 metres (3.140 m2 of productive area). He also has been building an additional 35 units in two different locations.
Generally, circular shrimp ponds are constructed using wire mesh or bamboo as the frame and HDPE as the inner lining. However, there are also those who use combination galvanized steel and fibreglass. The diameter of the ponds varies from 3 to 30 metres.
Given their comparative novelty, circular ponds have not been fully understood and mastered by shrimp producers and that are still many more things to be learned and adapted in managing this pond system.
In his research process, Rizky did not apply a standard system, but instead trialled different production methods. "We just decided to try it and see what the results are like. If it works, we can increase the efficiency of our ponds," he explains.
According to Rizky, the advantages of the circular design include the ease of ensuring water circulation, so the waste is more easily removed through the central drain. In addition, a smaller pond size makes it easier to combine with new technologies, such as RAS (recirculating aquaculture system).
Meanwhile the challenge is that the farm technicians have to try to focus on several different types of ponds in one area. While one hectare traditionally contains 2 - 4 rectangular ponds, with circular ponds it will likely contain 10 - 20 units, potentially making it more labour intensive.
"But also, because the pond is divided into several units, shrimp culture practices become relatively safe, because when a disease strikes, fewer shrimp are affected. So we can reduce the risk," he notes.
Risky is aware that the most important thing is to stay profitable. Instead of applying the latest technology to his circular ponds straight away, he actually started with a lower level until he found the optimal system. He hasn't yet invested in digitisation and IoT-related tech.
As a result, he is currently stocking the shrimp with a density of 150 PL (post-larvae)/m2. With this density, the production target he wants to achieve is 1.3 tonnes per pond in 90 days – the equivalent of 41 tonnes per hectare.
For water quality management, he has adopted similar practices to conventional ponds, changing the water every day, as needed. He also did a little research to find the best way to maintain the dissolved oxygen level, trialling various combinations, including the use of 1 paddle wheel with 1 blower, 2 paddle wheels with 1 blower, and 1 paddle wheel with 1 nanojet.
"So far, by using one paddle wheel we can make sludge collect in the centre of the pond. So, we will use this method for the next cycle," he says.
Feed management is also almost the same as in large ponds and he uses Profeeder auto-feeders, which are made by Aquaculture Innovation Indonesia, for gaining efficient and effective results. With this system, he can get an average feed conversion ratio (FCR) of below 1.2.
Rizky predicts that circular ponds will become increasingly popular in Indonesia. Several farmers who are members of the PMI have also started to develop it. He admits that he had been asked several times for his opinion regarding the construction of this system.
"Other farmers have developed their own designs, which I have also visited and studied,” he says.
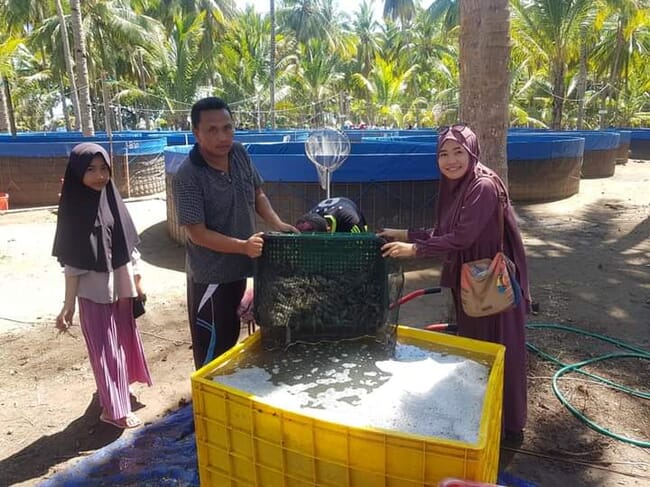
© Nonot Tri Waluyo
The opportunity for small farmers
The circular pond system was also initiated by Nonot Tri Waluyo, a shrimp producer from an integrated fisheries company, Central Proteina Prima (CPP). Through his company, he targets farmers who have limited resources, such as capital and land, to become his partners. According to him, the advantages of the circular pond concept include being efficient in terms of land use, more practical, lower cost and suitable for small scale producers. He also notes that these ponds can be built in only 48 hours.
The circular ponds owned by the partners of CPP have diameters starting at 15 metres. However, according to Nonot, most have a diameter of 28 - 30 metres. For optimal performance, a 30 metre pond needs three paddle wheels to maintain its dissolved oxygen levels.
The stocking density with this system can be pushed up to 200 PL/m2, but of course the farm management will be more challenging at higher densities. For household scale, according to Nonot, the density of 100 - 125 PL/m2, which is quite profitable and it’s realistic to achieve a shrimp survival rate of 80 - 90 percent.
Nonot believes that water quality management in circular ponds is easier, because the organic waste can be concentrated in the centre of the pond and easily removed through a central drain. Therefore, the "playroom" for shrimp is also getting wider. This situation can reduce shrimp stress level and make them healthier.
Nonot and CPP have initiated this circular shrimp pond in various regions, including Lampung, Central Java, East Java and West and East Nusa Tenggara.
© MMAF
Millennial shrimp farming (MSF)
The circular shrimp project was also developed by the Ministry of Marine Affairs and Fisheries (MMAF) through several of its research centres. This style of pond was built as a pilot project and learning facility for young farmers who want to get involved in shrimp aquaculture. As a result the project is called Millennial Shrimp Farming (MSF). It was uninitiated by MMAF and Digifish Network, an Indonesian fisheries start-up network.
Through MSF, the government is targeting the growth of young farmers in Indonesia, which is expected to be one of the contributors for national shrimp production and can help to increase the country’s shrimp export value by up to 250 percent between 2020 (when it was worth $2 billion) and 2024.
The MSF pilot farms use the latest technologies, such as digitalisation and IoT, to speed up decision making and minimise losses should an outbreak of disease occur.
One of the latest technology applications being trialled at MSF facilities is Oxygen-Mixed (Oxy-Mix) Fine Bubble, which is produced by Wendy Prabowo, a researcher at UTP in East Java. These are capable of producing oxygen from two sources, namely from free air and liquid oxygen. This combination can produce oxygen in the form of nano and micro bubbles which can maintain oxygen levels in the water properly.
"MSF is one of the MMAF's featured programmes, in order to promote shrimp farming to improve local economies. Pilot MSF installations have been built in two locations of the Technical Implementation Units (Unit Pelaksana Teknis/UPT) of the Directorate General of Aquaculture, namely in Jepara and Situbondo," said director general of aquaculture of MMAF, Slamet Soebjakto recently.