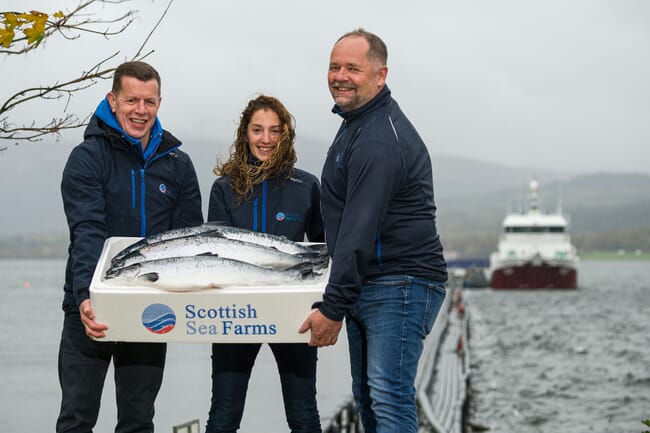
© Scottish Sea Farms
The fish were transferred a year ago from the £58 million hatchery at Barcaldine to a site in Loch Nevis for on-growing. The smolts had an average weight of 178g when put to sea – more than double the weight Scottish Sea Farms would expect to achieve via traditional hatchery methods – and required two months less in the marine environment to reach market size.
Freshwater manager Pål Tangvik said: “Thanks to its state-of-the-art recirculating aquaculture system – or RAS for short – we now have much greater control over the key growth factors of water quality, oxygen levels, temperature, light and speed of flow.
“This creates a more stable environment compared to conventional flow-through hatcheries which, due to the fact they draw in freshwater from rivers or lochs, can be subject to changes in weather.
“We’re also able to keep each generation of fish completely separate and bio-secure, meaning we can maintain peak health throughout the freshwater cycle.
“Combine this with our hugely talented fish husbandry and technical teams, and what we’re seeing is bigger, healthier smolts which not only require less time at sea but are better able to withstand the natural challenges of the marine environment."
The 17,500 m2 hatchery has scope to produce up to 10 million smolts annually. Its coastal location means that they can be transferred directly to a wellboat via a pipeline then transported on to one of the salmon grower’s 42 marine farms around Scotland’s west coast, Orkney and Shetland.
Sustainability
Of the 5,200m3 of freshwater required per day, up to 99 per cent is recirculated, equating to a saving of over 20 times the freshwater consumption of conventional methods.
This water is cleaned every 30 minutes via a complex system of filters and UV light (no chemicals) and maintained at a constant temperature via a combination of heat pumps and heat exchangers. These use less energy than traditional kerosene boilers or electric chillers and can also recover heat from waste-water for re-use.
Meanwhile, a biomass system run on locally sourced wood chip provides heating and hot water throughout the rest of the facility and the waste from the facility is processed for use as agricultural fertiliser.