Due to the increased demand for freshly caught fish and considering the imminent overfishing of the oceans, aquacultures attach growing importance while there are different types of aquaculture installations.
For instance, aquaculture can be found in stagnant or streaming waters under open air (outdoor fish farming), in net compounds in the sea (sea farming) or in indoor fish farms. All systems with “closed” water cycles have one thing in common: they make high requirements to the applied water treatment technologies – for this reason, the German company Multi Umwelttechnologie AG developed the “Mutag BioChip™ RAS Process”.
Principle of the RAS (Recirculating Aquaculture System)
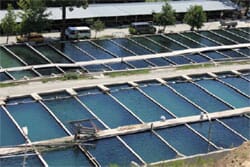
Due to the supply with food, the water is permanently contaminated with organic components and nitrogenous compounds from the natural excrements of the fish. In open-cycle installations, the contaminated water is conducted out of the system and replaced by fresh water, while there is only little fresh water conveyed to closed-cycle installations; the majority of the water available in this type of system is treated and subsequently returned to the breeding tank.
Due to the permanent transfer of water from the breeding tank to the treatment tanks and back, this particular type is called recirculating aquaculture system, briefly RAS. Taking into consideration the increasing scarcity of water in many parts of the world as well as the increasingly stringent regulations imposed by authorities and the current quality requirements to food fish, those closed systems are ecologically and economically useful alternatives compared to open-cycle aquaculture installations, whereas they have to comply with the highest requirements in terms of the applied technologies and notably of the water quality.
Mutag BioChip™ RAS Process
In order to comply with the water quality required by fish or other aquatic creatures, the organic contaminants and the nitrogen compounds to be found in the water mainly as ammonium have to be removed. Hence, the reduction of nitrogen down to a level which is nonhazardous to the fish is one of the major tasks of the treatment system in recirculating aquaculture systems. The “Mutag BioChip™ RAS Process” is perfectly suitable for this purpose.
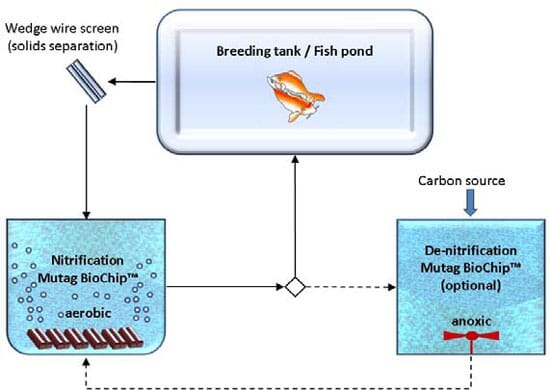
Basing on the carrier medium for immobilisation of microorganisms called Mutag BioChip™, which has a protected effective surface of 3,000 2/3 and is therefore the carrier medium with the currently largest surface on the global market, the Mutag BioChip™ RAS Process offers removal rates more than 5 times higher than the ones of similarly arranged systems.
Within this process, the volume flow to be treated is conveyed from the breeding tank to the treatment tank using Mutag BioChip™. This tank is based on the MBBR principle (MBBR = Moving Bed Biofilm Reactor; also called fluidized bed process) characterized by sessile microorganisms colonizing the surface of the carrier media and therefore establishing a thin biofilm while the single carriers can move freely in the water and are kept in suspension either by process air provided by tube aerators installed at the tank bottom or by mixers. In the first, aerated MBBR tank the nitrifying microorganisms immobilized on the carrier surface transform the ammonium nitrogen (NH4-N) to nitrite (NO2) and subsequently to nitrate (NO3). This process is called nitrification.
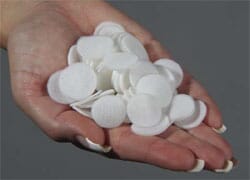
Usually, the water which has been biologically treated in the abovementioned way is taken back to the breeding tank.
Optionally, in the case of high nitrate concentrations, a partial volume flow of water can subsequently be conducted from the nitrification stage to a second, un-aerated MBBR with mixers. Due to the conditions adjusted in this tank which is also equipped with Mutag BioChip™, the anoxic de-nitrification process takes place whereas the nitrate (NO3) is transformed into elemental nitrogen (N2) which is released into the atmosphere as harmless gas. Subsequently, the denitrified partial volume flow can be recycled from the de-nitrification tank back to the nitrification stage.
Comparative study: Mutag BioChip™ RAS Process
In the German aquaculture company Fischzucht Langwald the Mutag BioChip™ is used since spring 2010 for nitrification purpose in a sturgeon farm (RAS). In the scope of an experimental trial a “conventional” carrier medium with a mathematically defined protected active surface of 900 m2/m3 was compared with Mutag BioChip™ (3,000 m2/m3) under identical conditions; i. e. similar tank volumes, the same water and similar volume flows had been used.
The volume of both breeding tanks was 6 m3 each while the active volume of both MBBR tanks for the water treatment accounted for 600 litres each. The two types of carrier media were applied at the same total surface whereas, due to the different sizes of the specific surfaces, the media filling level for the conventional carrier was 25 per cent (150 litres) and for Mutag BioChip™ 7.3 per cent (44 litres).
At the beginning of February 2010, the initially low supply with fish food was adapted to the very low water temperature of 10°C while the temperature-dependent growth of the nitrifying bacteria on the carrier surface took several weeks. The activity of the biofilms could be observed to increase accordingly to the rising temperature and the correspondingly augmented food supply.
In the MBBR using the Mutag BioChip™ RAS Process the NH4 concentrations accounted permanently for 0.1 to 0.2 mg/L at water temperatures of 21°C in average and 25°C in peak while the daily food supply was 500 g. Since in those trials only the nitrification performance was observed and due to no second MBBR installed for de-nitrification, in order to keep the NO3 level low enough to prevent damage to the fish the water exchange was kept between 5 and 15 per cent of the system per day.
The specific NH4 removal rates provided by the Mutag BioChip™ carrier were measured to be up to 0.24 kg NH4-N/m3 of media per day whereas the biomass immobilized on the carriers in both MBBR tanks was identical despite the lower media filling level in the tank using Mutag BioChip™.
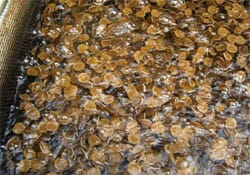
The percentage of biomass on the conventional carrier media fluctuated due to reasons not yet clearly explainable; simultaneously to these fluctuations there could be observed increases in the NH4 content in the water. Contrarily, suchlike fluctuations could not be observed with the Mutag BioChip™.
The analysis of the results showed that even if applied at a significantly lower carrier bulk volume, the Mutag BioChip™ RAS Process does not only work highly efficiently within aquaculture water treatment but is also characterized by maximum process stability and consequently provides high reliability in removal performance.
August 2014