The production of micro-algae to feed the mussel and oyster larvae is a key activity in a shellfish hatchery. Cawthron employs Liz, Cara and Nicky to produce the algae and develop improved culture methods.
Microscopically small algae are grown as the first food for the mussel and oyster larvae. These algae need to be nutritious and small enough to fit through the mouth of the 0.03-mm long shellfish larvae.
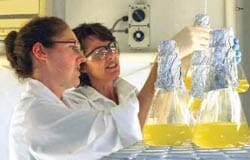
Tuesday morning, eight o'clock. Liz arrives and goes immediately to her first task. She swirls the stock cultures that grow in half-litre flasks in an incubator where light and temperature are controlled.
Liz said: "Growing algae is a bit like cooking, follow the recipe and the methods and from time to time you have to stir the cultures in order to get good mixing and a good product."
After that, Liz, Cara and Nicky look at the work planner and determine what they need to do and in which order.
Liz and Cara will start with the check-in to ascertain whether all the systems function correctly.
Cara explained: "For optimal algae growth, it is very important that the temperature is correct, the light intensity is OK and air flow, carbon dioxide concentration, and nutrient concentration are just right."
In many ways, the algae lab is similar to a microbiology lab. For example, every day new cultures are started from stock cultures. It is very important that the growth medium of the algae is free of bacteria (sterile) because bacteria can harm the algae and reduce their food quality for the shellfish larvae.
Nicky is preparing everything for the transfer of the algae from stock cultures to flasks and carboys. To avoid bacterial contamination, she heats the flasks and the carboys containing sea-water and nutrients in the autoclave to 121°C a few days prior to use. To ensure that the growth media in the containers reach the desired 121°C, Nicky puts an indicator into a flask.
Nicky said: "When the indicator has changed colour and melted, we know that the glassware is ready for use."
After lunch, the algae technicians start the transfers. First, they transfer the algae from a 500-ml flask to the three-litre flasks in the laminar flow hood.
She continued: "We always transfer in the back of the laminar flow hood, to make sure only filter-sterilised air enters the flasks. We also spray our hands with ethanol and flame the necks of the flasks with the Bunsen burner between each transfer. Clean and systematic work is very important. If a flask or other equipment is not clean and sterilised, the algae will not meet the quality requirements."
When the flasks are inoculated, it is time to do the transfers into the 20-litre carboys. "To avoid back injury we always have two people lifting these carboys." When all transfers are done, Liz and Cara take the carboys and the flasks to the algae room where they attach them to their individual sterilised air supply.
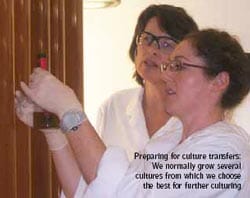
It is about 3 o'clock when the transferring is finished. After a cup of tea and a biscuit, the algae technicians make bags for the continuous algae production system.
Nicky explained: "We make these bags ourselves using special plastic. Each of these bags will be used for two to four months and in that time produce between 1,200 and 2,400 litres of algae culture. The continuous system can produce more than 2,000 litres of algae culture per day, which is sufficient for a commercial-scale hatchery."
After the 40-litre bags are prepared, they are hung on metal racks and then inoculated with algae from a carboy before being hooked up to the continuous supplies of sea-water, nutrients and air enriched with carbon dioxide.
At the end of the day Cara replaces the nutrient carboy and the carbon dioxide bottle that are attached to the continuous algae production system.
Cara explained: "The continuous system allows us to be more cost-effective than the carboy method, but it is technically more demanding. We have to ensure that all parts of the system work continuously to the specifications."
In addition to his usual high school studies, Lars Bannenberg is studying English towards the International Baccalaureate in English. An internship in an English-speaking environment is part of the curriculum. Lars did this internship at Cawthron.
October 2009