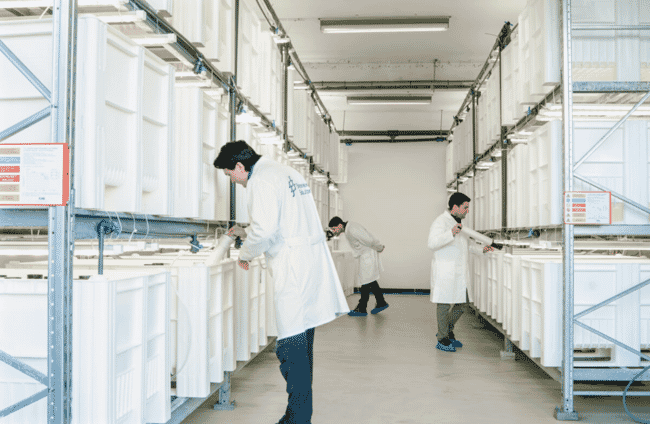
© Seaweed Solutions
Almost every industry at some point is disrupted by ideas that most people dismiss as impractical, unfeasible or impossible.
Technologies that are now widespread – such as radar, commercial jet planes, the internet and smart phones – were all ridiculed at some point. Such revolutionary ideas are often referred as “moonshots”, “loonshots”, or “disruptive innovations”. They are ideas that go against the accepted ways of doing things, but this is what gives them the power to revolutionise or disrupt entire industries.
In seaweed farming, direct seeding is sometimes seen as one such innovation, with the potential to replace the more traditional nursery incubation approach to seeding. Its proponents are adamant that this technique will drastically reduce seeding costs, improve logistics and help scale-up the industry. However, not all “moonshots” succeed – they are risky by definition. So here I will assess how likely I think direct seeding is to revolutionise the seaweed industry.
First though, some background information. Nursery incubation of seaweed is the process of producing small seedlings on rope (or any other substrate) in a controlled nursery environment prior to deployment at sea. Twine seeding is the most common sub-category of this method, where seedlings are grown on a thin rope (twine) that is later transferred to a thicker rope prior to deployment at sea. Other substrates can be incubated, however, including the cultivation rope itself – a method which uses more nursery space due to the added thickness of these ropes.
In direct seeding, on the other hand, the nursery stage is skipped entirely. Miniature seedlings (sporophytes) are instead “glued” to the cultivation rope a few hours prior to deployment. So, both methods require the production of seeds (gametophytes), and that is a labour-intensive process, but direct seeding avoids the multi-week nursery stage (see below) and therefore, the material and infrastructure costs associated with it – spools, twine, space, electricity, seawater and labour.
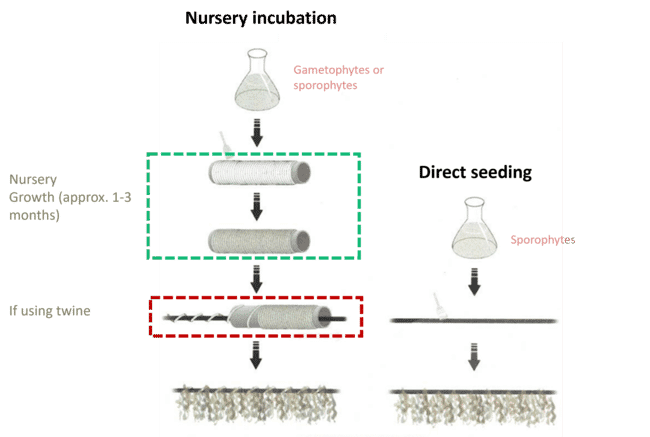
© Hortimare (modified)
All things considered, direct seeding usually beats nursery incubation when it comes to seedling production costs, but this is not always the case. Exact costs are hard to discuss, however, as these vary depending on several factors – including the seedling supplier, seeding density, seedling shipping and delivery logistics, reuse of ropes, and the size of the order. The potential to reduce seeding costs will only be fully realised at large scale, with low seeding densities and re-use of rope.
However, the key question is not whether nursery incubation costs are too high, but whether those costs are worth it in terms of reliability and yield, bearing in mind that the current market price for kelp is currently around €2-3 per kg.. Other important questions are how much room there is to reduce the costs of each method in the future, and whether the methods can scale up for industrial production.
Reliability
Direct seeding fails more often than twine, but we do not have good data on the exact failure rates of both methods as: a) reasons for failure can be hard to determine, and are further complicated by seedling suppliers and seedling customers blaming each other for lack of success; and b) known failures often go unreported in a world where admitting to slip-ups can cost you potential investment.
What I have noticed anecdotally is that many seaweed farmers have tried direct seeding and had very disappointing results, often over several years. This has been the case for large companies such as Lerøy Ocean Forest: Norway’s largest seaweed cultivator by biomass. It has also been the case for countless other smaller companies in Europe. Yet there are also several success stories, with Ocean Rainforest standing out in particular, and both Hortimare and Arctic Seaweed claiming they have made breakthroughs with the reliability of this method over the last few years.
One reason for the reduced reliability of direct seeding is that it’s inherently more vulnerable to a variety of factors, specifically those in the environment. To truly understand why, we need to look at the processes involved from the moment of seeding.
The first process is catchment – the initial sticking of the seedlings to the substrate, be it rope, twine, or any other material or structure. This is a physical phenomenon and is determined by the substrate properties, including its composition and “roughness”. To assist this process in direct seeding, a binder is commonly used which essentially acts as a glue.
Catchment is followed by attachment: a biological process in which the holdfast of the seaweed grabs the substrate after around 14 days. In nursery incubation, this happens in the controlled nursery environment, but in direct seeding this happens at sea. So here we have the first vulnerability of direct seeding, as adverse sea conditions can potentially wash away the binder, and with it, the valuable seedlings – valuable both in terms of upfront costs and for their future harvest potential.
Following on from catchment and attachment, the seaweed then progresses from early-stage growth to late-stage growth over several months, where it becomes more and more resilient to both dislodgement and competition from other biofouling organisms. Biofouling of seeded line is a big problem for seaweed farmers. This involves other organisms, commonly other algae or small jelly-like invertebrates called hydroids, fighting for space and competing with the seaweed. This can result in low yields, poor quality or even total crop failure. In nursery incubation, attachment and early-stage growth are performed under controlled nursery conditions, free from other competing organisms, which provides a certain degree of protection to the seedlings while they get established. In direct seeding, the seedlings are much smaller and therefore a lot more vulnerable to competition.
You can see the above ideas conceptualised in the diagram below, which shows how both seedling loss and biofouling risk reduce as the seedling progresses from the early catchment stage through to late-stage growth.
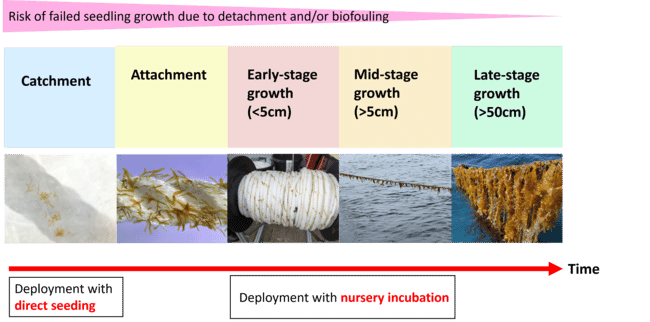
© SINTEF Ocean
Yield
The most effective way to maximise yield in temperate seaweed farming is to give seedlings the longest growth season possible. Autumn is usually the earliest you can deploy because the cooling water column is becoming more mixed, which brings nutrients to the surface – without these nutrients, the seedlings will not grow and may even perish during summer. However, these extra nutrients lead to a surge in phytoplankton which in turn feeds many other organisms. These organisms therefore pose a biofouling risk to any deployed seedlings, and also a dilemma: deploy early and maximise yield, but at the risk of fouling the seeded lines; or wait a bit for these organisms to die-off (which happens as winter approaches), reducing this risk but sacrificing yield.
As discussed above, the small size of seedlings used in direct seeding makes the lines inherently vulnerable to biofouling. This vulnerability pushes users towards later deployment and lower yields in order to manage that risk. On the other hand, with nursery incubation, farmers can deploy larger seedlings slightly earlier, and that double whammy should provide a more favourable yield at harvest. As kelp grow exponentially under ideal conditions, small differences at deployment translate to large differences at harvest, which is why yields from nursery incubation can be many times higher than direct seeding. This is something we see time and time again in the scientific literature. That is before looking at potential Western adoption of Asian techniques for deploying larger “summer seedlings”: 10-20 cm sporophytes that are cultivated in nurseries over the summer in order to get a head start and achieve even greater yields.
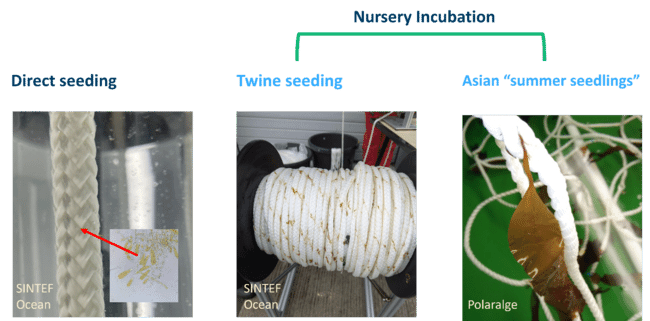
© David Aldridge
Scalability
The only scaled seaweed industry (Asia) is based on nursery incubation (albeit combined with intensive labour). I would argue that as nurseries in the West increase in size, in response to growing market demand, there will be a large reduction in seedling prices, bringing the costs closer to those of direct seeding. This is because nurseries require high capital expenditure to build, maintain and run. However, many of these costs are fixed regardless of production volumes.
So, while these fixed costs currently constitute around 30-60 percent of the costs of nursery incubation, an increase in production volumes by an order of magnitude could see those costs drop to less than 5 percent. That is without even considering innovations which could reduce twine/seedling use. “Splice seeding” in Asia inserts small pieces (3 cm) of twine into the cultivation rope at 20 cm intervals in order to control canopy density and optimise yields. That innovation alone would result in a seven-fold reduction in seedling costs with twine.
One challenge in bringing down the costs of direct seeding is that a high number of seedlings often needs to be used. This is to improve reliability by compensating for losses that occur at deployment. With nursery incubation, seedling losses are much lower, so it is easier to reduce densities closer to those optimal for achieving the best yield. Certain innovations, such as bioreactors, will help with direct seeding costs. However, they will also bring down the cost of nursery incubation, as both seeding methods rely on this initial stage of seed production.
When it comes to deployment logistics and speed, there is little difference between methods. The speed of direct seeding of rope using machines such as the SEASEEDER (developed by SEAWISER), is similar to wrapping seeded twine around cultivation rope (1-3 km/hr). The difference is that in direct seeding there has commonly been a gap of a few hours between seeding and deployment to allow the rope to absorb the seedlings and binder, so this first step is almost always done on land.
The reported deployment speeds for direct seeding often fail to take into account this work on land, which can be very labour-intensive. With twine seeding, it is also possible to create a two-step process: wrapping of twine on land, followed by deploying of substrate at sea. So in that respect, operations at sea are basically comparable and systems for deployment are usually interchangeable. One advantage of twine, however, is that once it has been wrapped around the carrying rope it can be kept for very long periods of time in a healthy state, so long as it is submerged in seawater. This gives flexibility when logistics or weather forecasts change. Once rope has been direct seeded, it has a much shorter shelf life and must be deployed within a matter of days, according to most seedling suppliers.
Potential innovations
Current innovations focus on the seeding binder, and the development of more effective ways to catch the seeds prior to attachment of the holdfast. At SINTEF Ocean (together with The Norwegian Seaweed Centre)we are developing such a binder together with the company Sirputis and testing it as part of the a direct seeding focused project called DIREKTE (funded by the Norwegian Seafood Research Fund), where we are looking at several ways to improve direct seeding protocols – from improving seedling production techniques, to refining seeding methods, substrate and binder choice, together with storage and deployment protocols.
Additionally, the European seaweed pioneer and Hortimare founder, Job Schipper, has also been championing a new binder via his consultancy company, SEAWISER. There have been previous unsuccessful attempts, notably from WL Gore, to do away with binders by making ropes which better catch and trap the seeds, but this may also be an area for future innovation.
However, binder innovations can only account for the optimisation of the catchment process, and also the efficient use of seedlings; they cannot easily solve these other issues related to biological vulnerability of small seedlings in an ocean full of competing life. To overcome this, research could focus on biofouling-resistant cultivation rope/substrates or using larger seedlings. Larger seedlings are, however, less sticky and also more prone to dislodgement. This presents problems in developing a binder that is strong enough to hold large seedlings in place without either damaging them or reducing the exchange of vital gases and nutrients. Hortimare recently presented at Seagriculture Asia the idea of selectively breeding for faster early growth and attachment, and this could be another area for exploration.
The most realistic short-term solution is perhaps for farmers to better understand what is going on in the environment in terms of variables such as temperature, nutrients, fouling organisms and current velocity to nail the deployment window and give the seedlings the best chance of survival possible, while also optimising yield. This could be aided by real time sensors and water quality monitoring in order to act quickly and deploy when conditions are favourable.
Another research requirement, from both a cost and sustainability point of view, is re-use of the cultivation rope. With twine seeding, it is possible to re-use this rope for several years, with minimal reduction in yield. In direct seeding, which is highly dependent on the rope’s surface structure for capturing seedlings, this must be replaced frequently (usually every year). With a cost of around 1 Euro/m, that is an often overlooked yet significant additional cost to this method.
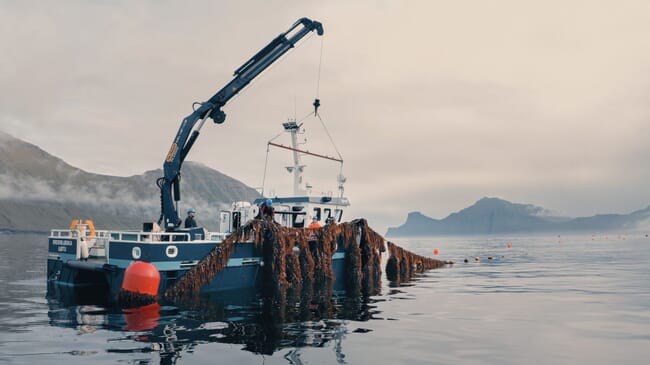
© Ocean Rainforest
Examples of successful direct seeding
There are both current and future use cases for direct seeding that make a lot of sense. Ocean Rainforest have been successfully using this technology for many years in the Faroe Islands. The key here might be their unique cultivation location, which allows multiple harvests over several years via “cropping” (cutting the kelp above the meristem to allow regrowth). This presumably allows them to seed later in the autumn/winter and pick a deployment time that reduces the risk of biofouling, as they are not so reliant on that first harvest yield.
Seeding of novel structures (such as sheets, bands, carriers or nets) has generated much hype over the years, but none of these alternative substrates have ever materialised due to the complexities of both seeding and harvesting them.
Conclusions
Direct seeding will likely continue to play a key role as a seeding technique in certain locations and for novel substrates, but there are several challenges that need to be solved before it reaches moonshot status in my opinion. Reliability is seemingly improving and will likely continue to do so with new innovations arising from research efforts. Research into reducing costs via improvements to the protocols are also underway and will help with the scalability of this method. However, the issue of low yield (up to 4 times lower in some locations) is currently the hardest hurdle to overcome due to the head start in seedling size that is possible with nursery incubation.
Moonshots by their nature are high risk but high reward, and until the issue of yield is addressed then it is hard to classify direct seeding as a moonshot technology, unless overall costs fall so much that this compensates for the reduced biomass. While unforeseen technological developments may change this, we should not overlook the possibility that a seeding moonshot may come from innovations related to nursery incubation and twine. There are many existing methods used in Asia, such as splicing of twine and the use of summer seedlings, that have yet to be adopted here in the West and yet have the potential to have much greater impacts on both biomass yield and seedling costs.