Due to relatively small herds, large distances and low energy prices, costs are a challenge when constructing biogas plants on farm level in Norway. Residues from food industry may be an option to increase the biogas output. In Tingvoll, ca 120 km southwest of Trondheim, a pilot biogas plant for treatment of animal manure will be built on an organic research farm during 2010.
Locally available food waste includes residues from fish oil production. Wax, soap and bleaching earth is available. Wax may also be utilised to replace fossil oil in heating boilers, and may hence be less relevant for biogas purposes. On the other side, bleaching soil and soap may contain elements that are not feasible for the biogas process, or for the biogas residue as a soil conditioner. Hence, wax was selected as the first residue to test for its biogas potential.
Purpose
The project aims to examine the suitability of the co-digestion of fish wax (stearin) with cattle manure to produce biogas. Stearin was mixed with cattle manure at 0, 2.5 per cent, five per cent and 10 per cent w/w as this was estimated to be a range that would be realistic in practice and to provide a comparison with manure alone.
Method
The work was carried out as batch experiments for a period of 42 days. All samples were measured in triplicate.
The batch experiments were conducted in glass infusion bottles of 1100mL. Each batch was inoculated with 400 g of de-gassed digestate from a stable anaerobic digester (University of Aarhus Biogas plant, Research Centre Foulum).
The de-gassing process consists of incubating the inoculum at 35 °C for a period of 1 week prior to the batch assay to remove as much of the residual methane potential as possible yet still retain a large active microbial community. De-gassing therefore reduces the biogas contribution of the inoculum during the assay and thus allows for more accurate measurement of the biogas produced by the studied substrates.
The substrates to be studied were added to the inoculated infusion bottles at a total mass of 50 g. One set of triplicate bottles were inoculum only as a blind control. The cattle manure was mixed well before adding to the inoculum by pouring from a plastic container. The stearin was warmed slightly to melt it and was then added to the manure and inoculum mix using a Pasteur pipette. The small mass of stearin used and the tendency for it to form droplets meant that the stearin additions varied by approximately five per cent between replicates, although these masses were recorded and the gas yield calculations were based on the exact data.
The infusion bottles were then sealed with butyl rubber tops and flushed with nitrogen for two minutes to remove as much oxygen as possible. The nitrogen was added through a hypodermic needle which pierced the butyl cap, the gas left the bottles through a similar needle that was open to the atmosphere (Figure 1). The bottles were then incubated at 35 °C in complete darkness (Figure 2).
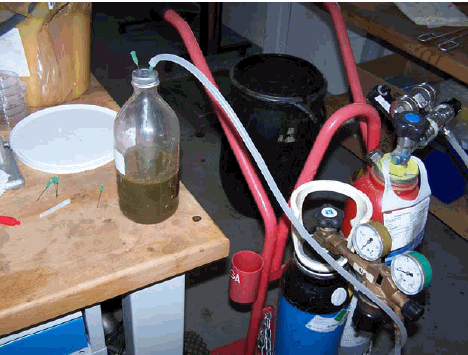
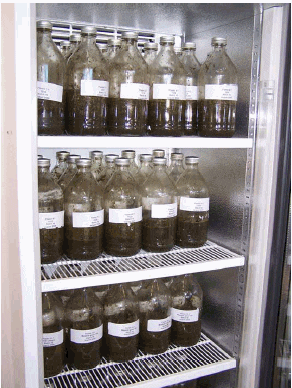
The biogas produced by the activity of a consortium of microorganisms consists largely of methane (50-70 per cent) with the remainder being carbon dioxide (30-50 per cent) and a large number of other gases such as water vapour, hydrogen and hydrogen sulphide in small and often highly variable quantities. The produced biogas was measured periodically, as and when the pressure needed to be released based on a visual observation of the degree of swelling of the butyl stoppers. The bottles were shaken well by hand before measurement but any other form of mixing was absent. The gas volume was measured by acidified water displacement (Figure 3). Acidification was necessary to reduce the solubility and subsequent loss of CO2.
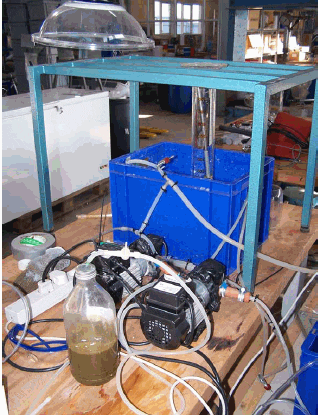
The biogas composition in terms of CH4 and CO2 was determined by gas chromatograph (GC), gas samples were collected each time the volume was measured. Based on previous experience it was considered necessary to only measure the gas composition in one of each set of triplicate samples. The gas composition had to be calculated from the GC results as the nitrogen used to flush the bottles contaminates the biogas, although this contamination becomes less throughout the experiment.
The calculation method as7 sumes that CH4 + CO2 = 100 per cent of the biogas, other biogas components such as H2S and H2 are likely to constitute perhaps 0.1 per cent of the total volume and hence these were not measured in this study. The aim of the calculation is to eliminate the nitrogen used in the initial flushing by considering the measured CH4 and CO2 as constituting the entire biogas, as shown in Equation 1.
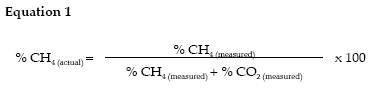
Biogas and methane yield calculations required the measurement of both dry matter and volatile solids (VS) of the inoculum and the studied substrates. Volatile solids are organic compounds, as opposed to fixed solids such as mineral material. The biogas and methane yields are expressed as litres of the biologically produced gas (of mixed composition) and litres of methane produced per kg of volatile solids, respectively. Dry matter was measured by drying for 24 hours at 105 °C and the volatile solids by incineration at 550 °C for 2 hours. The gas yields were calculated by measuring the gas production of the tested samples, then subtracting the gas production of the inoculum-only blind control.
Results
Dry matter and volatile solids
The dry matter and volatile solids of all materials are shown in Table 1. It was found that the stearin contained less than 1 per cent water and no measurable inorganic matter, i.e. there was no residue left after incineration at 550 °C.
Material | Dry matter per cent | VS per cent of dry matter | VS per cent of fresh weight |
---|---|---|---|
Inoculum | 4.26 | 76.18 | 3.2453 |
Cattle manure | 8.19 | 89.2 | 7.3055 |
Stearin | 99.19 | 100 | 99.1900 |
Biogas yields
The biogas yields of the four measured samples are shown in Figure 4 with the totals after 42 days summarized in Table 2. The yields are the result of gas production minus mean blind control gas production per kg of sample volatile solids. It is clear that the addition of stearin to cattle manure significantly increases biogas yield. The cattle manure and the 2.5 per cent and five per cent stearin mix samples appeared to have very nearly ceased in terms of gas production by day 42, based on the flattening of the curves. It is unlikely any extension of the assay time period would have given significantly more gas for these samples as previous experience has shown that the flattening of the curve indicates that the gas production is slowing to a stop.
Methane yields were calculated from the biogas yield obtained after 42 days and the mean methane percentage in the biogas throughout the experiment. The methane yields were 256, 425, 542 and 629 L/kgVS for cattle manure, manure with 2.5 per cent stearin, manure with five per cent stearin and manure with 10 per cent stearin respectively (Table 2). These values are based on the biogas yields and the mean methane percentage values through the experiment.
Substrate | Biogas yield (L/kgVS) | Methane yield (L/kgVS) |
---|---|---|
Cattle manure | 427 | 256 |
Cattle manure + 2.5 per cent stearin | 686 | 425 |
Cattle manure + five per cent stearin | 861 | 542 |
Cattle manure + 10 per cent stearin | 999 | 629 |
The yields are considered to be the maximum possible by biological conversion and, in the case of methane yield, are known as the ultimate methane yield, B0. This number is considerably less than the theoretical methane yield, Bu, derived from the Buswell equation which estimates yield based on the chemical composition in terms of C, H, N and S (Buswell, 1936).
An indication of the biogas and methane yields and the expected methane fraction of the biogas for single materials is shown in Table 3. In the case of single materials such as these complete degradation can be expected and therefore B0 and Bu are the same.
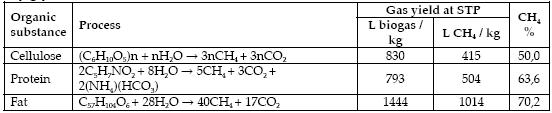
The 10 per cent stearin mix gave a lower gas yield for the first three weeks of the experiment but then overtook all other samples. The gas production of the 10 per cent stearin mix was still increasing significantly at day 42 and this sample would have benefited from a longer assay period. The initial lag in gas production was attributed to inhibition, although the exact method of inhibition is unknown as the bottles are not opened for analysis of the digestate during the assay. It is possible that the high proportion of stearin very quickly produced either or both long and short chain fatty acids which are inhibitory to biogas production in high concentrations. Another possibility is that the stearin formed an oily coating on key microorganisms, thus reducing their function. The greater variation in gas yield from the 10 per cent stearin mix also suggests inhibition and an unstable process. Examination of Figure 4 suggests that the five per cent stearin mix was also mildly inhibiting because the gas yield is slightly lower than the 2.5 per cent mix at the start of the experiment.
Although this experiment did not specifically measure the biogas yield of fish stearin alone, this can be calculated by subtracting the gas produced by the cattle manure alone in a similar way to that in which the yields are normally calculated by subtracting the blind control. The calculated biogas yields were 1425 and 1491 L/kgVS from the 2.5 per cent and five per cent addition experiments respectively. These two values were considered similar enough to average them for a final biogas yield of 1458 L/kgVS, almost exactly the value calculated for glycerol trioleic acid in Table 2, suggesting complete digestion of the stearin and a B0 value close to the Bu value. The biogas yield value obtained when calculating backwards from the 10 per cent stearin addition was 1381 L/kgVS but as this assay appeared to be incomplete after 42 days this value was not included in the average. The methane yield can only be estimated due to the lack of data regarding the gas composition of a stearin only experiment. Using the mean methane percentage values recorded for the mixture experiments (63 per cent) gives a methane yield of 919 L/kgVS, whereas using the methane percentage from Table 3 for fat digestion (70,2 per ent) gives a methane yield of 1023 L/kgVS., Both these values are very close to the theoretical maximum.
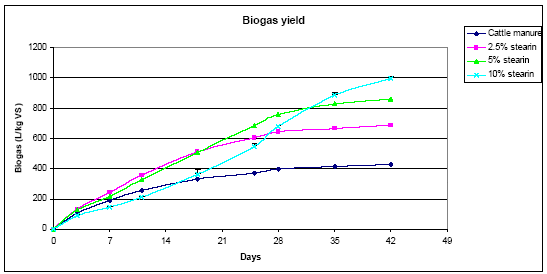
The mean methane percentages of the samples were 60 per cent for cattle manure, 62 per cent for the 2.5 per cent mix and 63 per cent for five per cent and 10 per cent mixes. The methane percentages throughout the experiment are shown in Figure 5. The 10 per cent stearin sample started with the lowest methane percentage but finished the experiment with the highest, at one point reaching 72 per cent methane (Figure 4). The variation in the 10 per cent stearin sample was attributed to the initial inhibition described previously.
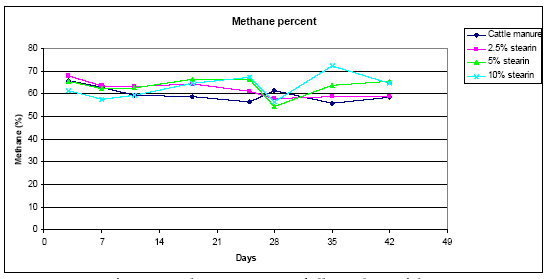
Conclusions
The data presented above suggest that stearin is a good substrate for biogas production with a very high biogas yield of 1458 and methane yields of between 919 and 1023 L/kgVS. Another advantage of stearin is the very high dry matter value and no measurable inorganic matter, making it a very concentrated feedstock. However, high yielding materials are often materials which are quickly and almost completely mineralised within a reactor. This may appear to be an ideal situation but in reality the microbial community within a reactor cannot cope with such a concentrated feedstock and inhibition is likely to occur. This was seen with the 10 per cent stearin mix and to a lesser extent the five per cent mix where biogas yield was inhibited at first to levels below that of the other tested substrates.
The recommendation for using stearin as a biogas substrate is to use it as was the case in this study as a co-substrate with manure which has a high buffering capacity to minimize inhibition due to pH changes resulting from acid accumulation. It is difficult to transfer the batch assay data to a continuous process as the batch assay operates because the batch assay has a single addition of substrate at a substrate to inoculum ratio which is much higher than a normal continuous reactor would receive in a single day. It is fairly safe to assume, however, that the 10 per cent stearin mix is too high for a stable continuous process and it is our suggestion that a biogas plant digesting stearin with cattle manure starts at a low stearin concentration of 2.5 per cent maximum and gradually build up to a slightly higher concentration if desired. This is especially true for a new biogas plant that has yet to stabilize where stearin would be best introduced after some period of initial stabilization during which the digester was fed manure alone.
It is possible to calculate the energy value of stearin when used for biogas production. Due to the uncertainty of the biogas composition from stearin alone, we can use approximate energy values of between 5.8 and 6.5 kWh per m3 of biogas to give a total energy of between 8.39 and 9.40 kWh per kg of stearin.