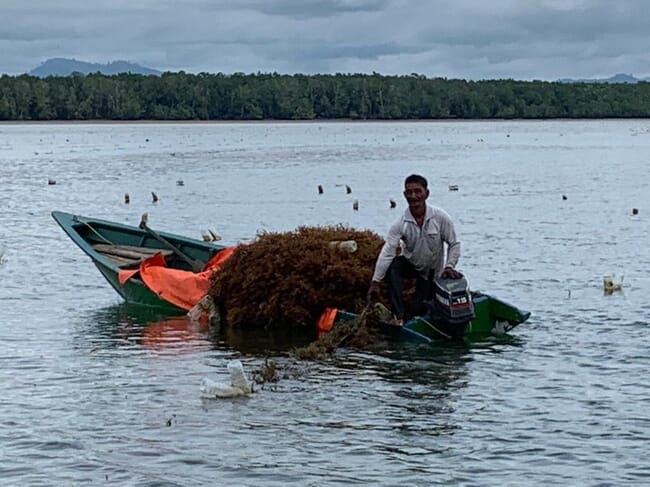
© Rhodomaxx
Can you tell us a little bit about your background?
I am a local Sabahan whose family has been involved in the production of semi-refined carrageenan in the region for more than 20 years.
After graduating in international food and agribusiness from HAS Hogeschool in the Netherlands, I decided to return to Sabah to explore the opportunity of seaweed as a biomass of the future with a fresh new focus on sustainability. Focusing on solving the plastics and greenhouse gas (GHG) problem in the consumer and agriculture sector respectively.
What inspired you to start working with seaweed?
The fact that seaweed really does not require any input, fresh water and land for cultivation itself is a huge reason why we decided to look at it from an alternative angle as a feedstock for the bio-based economy of the future.
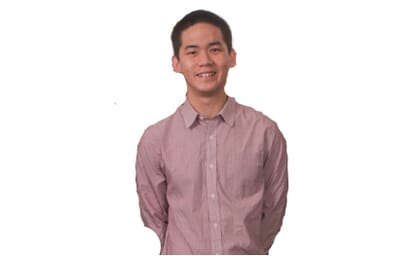
How do you differ from the competition in this field?
Rhodomaxx is different because of the way we look at seaweed. Many of the competitors look at it as a raw material for their innovation to solve a specific problem – for example as a yarn, a bio-plastic or an agricultural input. We look at seaweed as a system rather than just a part – because we already knew what characteristics Kappaphycus alvarezii can do from our semi-refined carrageenan experience.
That is why when you look at our innovation it’s not just one specific seaweed product but an integrated innovation system that maximises seaweed’s potential to produce bio-degradable plastics, vegan leather, seaweed yarn, fertiliser and the conventional semi-refined carrageenan.
Our technological readiness level (TRL) – particularly with our bioplastics and seaweed fertiliser – is also important. We are at our final stages and testing the bioplastics pilot machinery should be completed by mid-September, while our fertiliser side is already at full scale production.
Why did you decide on using Kappaphycus alvarezii as your prime candidate?
We have the experience in dealing with this type of seaweed, it’s hugely scalable and simple to cultivate – it’s already been cultivated for 50 years in the Southeast Asian region. The infrastructure is in place and it’s not as complicated as micro-algae, which require a bioreactor.
© Rhodomaxx
Do you work in seaweed cultivation too, or will you look to source your raw materials from existing seaweed producers?
We’re currently focused on downstream work but plan to enter the cultivation sector once we have suitable funders and also partners to change the traditional planting sector – from just being a crop cultivated by smallholder farmers to actual plantations, changing the whole idea of seaweed farming from novel crop to commodity crop.
The reason we also need to enter the planting side is also to carry out proper environmental impact assessment of seaweed cultivation in the region – as it’s not really been done before. So, for example, if you were to ask me now how much carbon is being sequestered by the seaweed cultivated or how does it affect nutrient flows and the ecosystem we don’t really know. Therefore, we do really need partners in helping us answer these questions.
What results have you obtained in the alternative plastic and cotton space to date?
We’re on the cusp of producing the first machine to rollout the bio-plastics at scale. On the apparel side we’re working with another partner who is looking to use the vegan leather we developed as a raw material for some major labels.
When do you think it might be possible to match plastic, cotton and leather from a price perspective?
Firstly, the raw material prices have to be lowered and that is where we think farming partners will be really needed to help push production volumes. Secondly, we really need investors who are willing to look at this project from a long-term perspective and can invest in production assets that can scale to meet demands rather than thinking of making a quick flip.
Even the petroleum industry took a few years to be where it is now. So we do believe that with enough time and the right partners we will be able to compete with plastics within 7 to 10 years.
As for cotton and leather we believe that the market is willing to make a more conscious decision on their purchasing behaviour and pay the premium we are charging for a more sustainable alternative. As the story of the material being worn or used by consumers are much closer to them instead of just being something that is wrapped around something that you want - ie packaging.
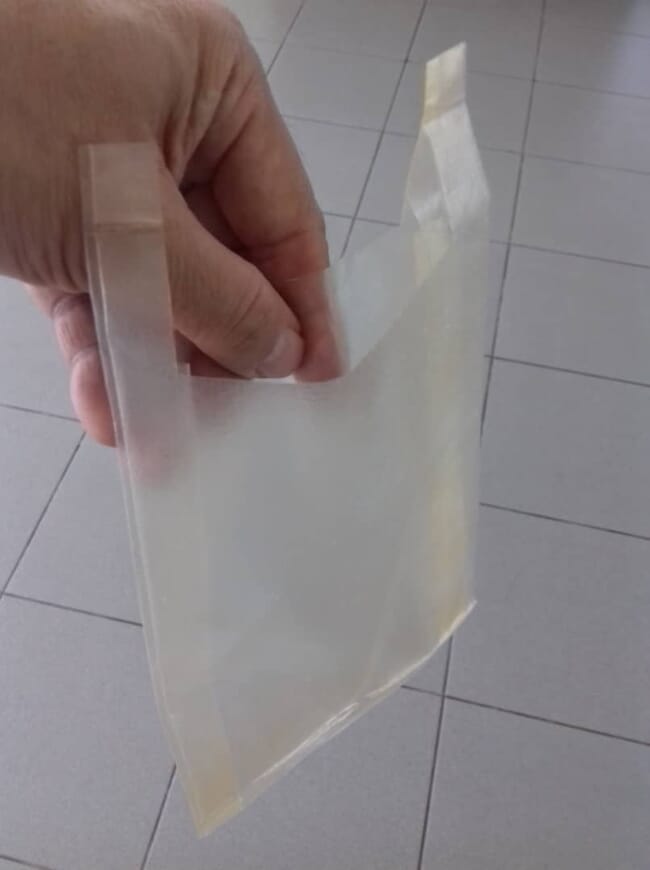
What demand is there for vegan alternatives to leather?
We stumbled upon vegan leather as a potential use when we were developing our yarn. We noticed that companies were beginning to look at sustainability as a core issue in their apparel production cycle. That’s why in 2019 the Fashion Pact was formed under French President Emmanuel Macron, which includes brands like Adidas, Hermes and many more.
Therefore, the innovations and raw materials that were once conventionally supplied to name brands are being re-evaluated and companies are facing constant pressure to find new alternatives to conventional raw materials, such as cotton, nylon, leather and polyester.
What’s the planned capacity for your first pilot plant and which of your various products are you going to prioritise?
We are planning to rollout 756,000m2 of bioplastics in year one, after the pilot machinery has been developed. This will be our main priority but, as previously mentioned, the fertiliser is up-and-running so if anyone is interested just feel free to contact us via zhun@rhodomaxx.com