The rise of automation and AI is changing our lives in a multitude of ways. Apps on our mobile devices make recommendations based on our habits. Computer-generated language translations help us understand each other without being bilingual ourselves. One day, our roads may even be filled by vehicles driven solely by software. Whilst the era of self-driving cars might still be a way off, automated aquaculture may arrive much sooner than you think.
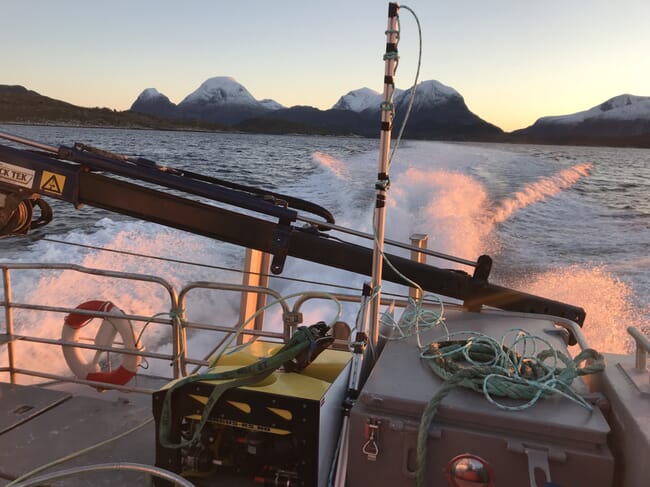
© SINTEF Ocean and Maritime Robotics
As every aquaculturalist knows, performing even the most routine of tasks can be hazardous. “If you have a half-metre wave height and you are walking around a cage, you will feel that. If it is one metre or one-and-a-half metres, it becomes almost a rollercoaster,” explains Walter Caharija, a research scientist with SINTEF in Norway.
With aquaculture operations expanding in coastal areas as well as further offshore, and the changing climate increasing wave strength, finding safer solutions for routine activities could not come at a better time. Enter SINTEF’s project ARTIFEX.
Currently in development, ARTIFEX combines the power of unmanned surface vehicles (USVs), remotely operated vehicles (ROVs) and remotely piloted aircraft systems (RPAS) to perform inspections and even execute maintenance and repair tasks. The USV’s primary role is to carry the ROV and RPAS out to the farms and return them back to the land, whilst the RPAS and ROV carry out farm inspections. If some maintenance or light repair work is needed, the plan is to have the ROV complete those tasks. The degree of automation these vehicles will have will vary, but the whole operation will be overseen by a single person, sitting safely onshore. For Caharija, this kind of technology is not just a luxury good.
“You want that because you don’t want to expose people to harsh weather and the risk,” he says.
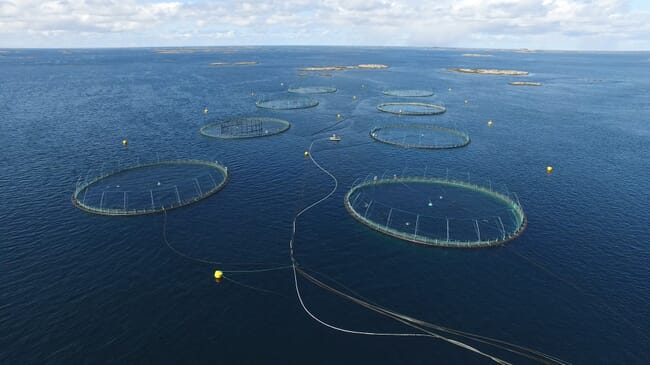
© SINTEF Ocean and Maritime Robotics
Whilst ARTIFEX looks to improve people’s welfare by taking them out of danger, Norwegian start-up BioSort AS is working with Cermaq to improve fish welfare with iFarm.
Essentially, iFarm is a system for monitoring growth, sea-lice, deformities and other health indicators. What makes iFarm unique is that it combines a suite of sensors with AI to identify individual salmon. The technology is not so different from facial recognition technology in security software for our mobile devices, but instead of scanning human faces iFarm scans salmon’s spots.
“This ability to follow each individual fish opens a lot of possibilities,” says Geir Stang Hauge, CEO of BioSort. For example, the regular monitoring of individual growth rates and other health indicators helps farmers spot health issues early – and even monitor treatment effectiveness.
Hauge illustrates how this power to track a single fish might be used: “Is [the fish] improving or is it getting worse? Is it a fish that has no future, or is it a fish that actually is recovering from, for example, a winter ulcer?”
iFarm doesn’t stop at individual medical records – it also selectively removes individuals from pens for treatment. “As far as we know, nobody else is working on removing individual fish from pens based on health,” says Hauge.
Taking sea lice as an example, typically not all salmon in a farm will be infected, yet if there is an infestation, all end up being treated. Individual selection, on the other hand, allows for more targeted treatment options.
Whilst continuing software and AI development is important, some of the biggest challenges for automating aquaculture come down to engineering the infrastructure that the software will actually use to complete tasks. iFarm, for example, requires more than a series of sensors and an artificial neural network – it involves a whole-cage system design. Every salmon must pass a suite of scanners that ID the individual, take its measurements and check for sea lice and skin abnormalities. To achieve this, BioSort takes advantage of a key part of salmon’s biology – their need for air.
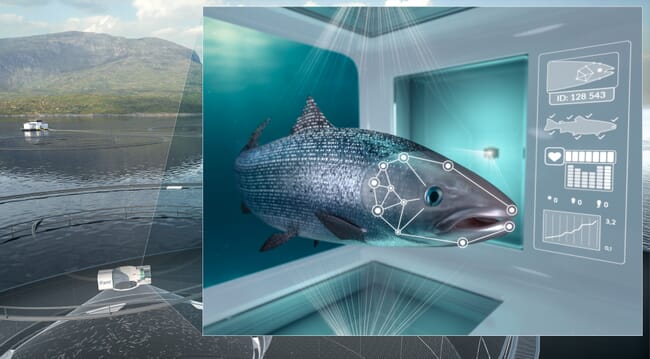
© BioSort
Salmon need to refill their swim bladders with air from the surface every four days or so. Rather than allow salmon to access the surface anywhere in the cage, iFarm limits access via a sensor-equipped funnel. Since the sensors cannot work in darkness, a lighting system is also needed. Then the salmon need to be sorted, which means physical infrastructure that either allows salmon back into the pen or redirects them to a separate area for treatment. Whilst each piece may seem relatively straightforward to produce, the key is to have all the components – the software, the mechanical components, the lighting, the optics – all working in synergy, all, Hauge notes, whilst keeping the salmon’s behaviour, natural preferences and welfare in mind.
Like ARTIFEX, iFarm is in development, but so far testing has gone well, and the next phase is not far off.
“We’ve done small-scale trials, but we have never tried this with 150,000 fish, 200,000 fish,” says Hauge. Alongside upscaling to larger numbers of fish, BioSort aims to spot sea lice as small as 1mm or 2mm in size, with optics that could be up to one metre away from the fish.
Hauge acknowledges that this is ambitious, but the idea is to allow aquaculturalists to keep as far ahead as they can of any potential outbreaks. Meanwhile, ARTIFEX is looking to put the various components that make up the vehicles through their paces at farms based in SINTEF ACE’s full-scale laboratory facilities.
“From the technical-solutions point of view, we’ve got everything on paper but it is going to be learning by doing,” Caharija says.
So, could there be a time when aquaculture is fully controlled by computers, and human input no longer needed? Caharija and Hauge agree there will always be a need for people, but some of the roles may change.
“You wouldn’t necessarily need every location to be manned all the time. You could have people who operate multiple locations,” suggests Hauge.
Then, as Caharija, highlights, while some processes can be automated there are others that can’t. “There is a lot of maintenance that is needed on the mechanical side and the electronic side, and so on,” he notes.
As both Caharija and Hauge agree, ultimately people will always be needed to make key decisions.